ArtinNC
Well-Known Member
Hey ArtinNC,I dont see nothing wrong with either one of those grinders.
Now get to grinding
God bless,Keith
I have been but don't you think I should finish some first???
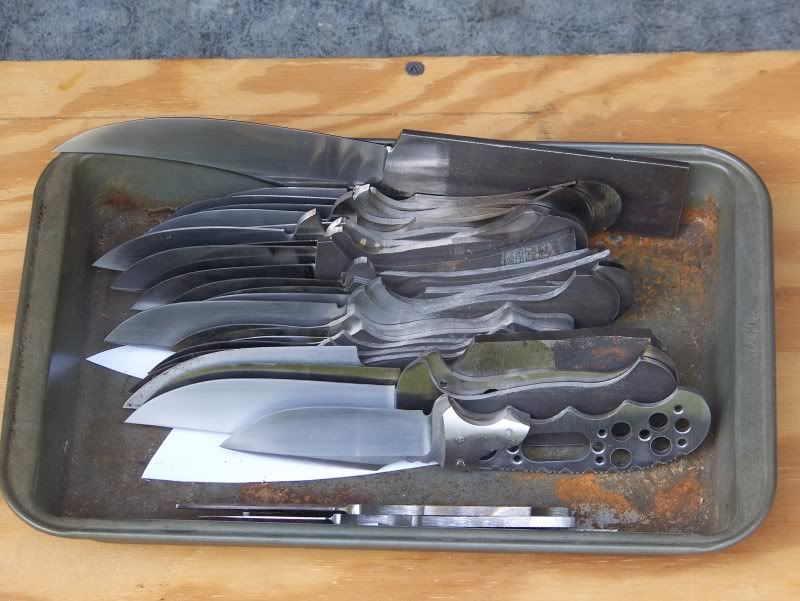
Hey ArtinNC,I dont see nothing wrong with either one of those grinders.
Now get to grinding
God bless,Keith
My new variable speed 2x72 grinder. Just finished building it at my friend's fab shop. (Quill Hyde, he's a whiz with design and fab.) The main parts were cut out on a CNC plasma torch, with a graphic of a snake wrapped around a torch, (Promethean Knives) I used the big contact wheel off my old hollow grinder, which meant we had to bore it for bearings to work with a square tooling arm setup, which lead to the slightly funky spacing issues you see on the attachments. It does not affect performance or ease of use however, it tracks nice and has plenty of power. That is a 3 HP, 3PH Baldor motor with the Teco FM50 VFD. It's a sensitive brute, just like I like. The VFD mount on the grinder frame is temporary, I'm mounting the VFD on the wall soon and using remote controls to keep it out of harm's way. The attachments all work great, the small wheel is just UHMW but would grind a little smoother with a rubber tire... I'm going to get a KMG small wheel fork for it eventually, though. I turned the tracking and idler wheels out of UHMW too, if it works for Bob Dozier it's good enough for me. I'm STOKED on this machine!
I'm sure most of you already know about this grinders pics collection... there are a lot of good ideas and some of them are really fancy and "super-machined".
http://gonza-rytec.rajce.idnes.cz/brusky/#album
PS:ehi! this is my first post on this forum! :steve:
I never saw that link.I'm sure most of you already know about this grinders pics collection... there are a lot of good ideas and some of them are really fancy and "super-machined".
http://gonza-rytec.rajce.idnes.cz/brusky/#album
PS:ehi! this is my first post on this forum! :steve: