mixed bag post today.
I am working on finishing the auto knife.
It was stupidly heavy. I used a 3/8" end mill and hollowed out the handles. Huge improvement.
I needed to countersink the pivot head I plan on using and didn't have a counterbore to fit.
The pivot hole is already there so it acts like a pilot hole. I never hand hold anything when drilling over 1/4" and most of the time I don't hand hold 1/4" drill. I have learned this the hard way. Anyway, I drilled with a 3/8" drill bit just enough to get a lip to hold an end mill. I then switched to an end mill and plunged the hole to depth. Putting it in the jig and clamping it down helps with chatter. This is a fairly dodgy way to do things but it's quick and works well enough.
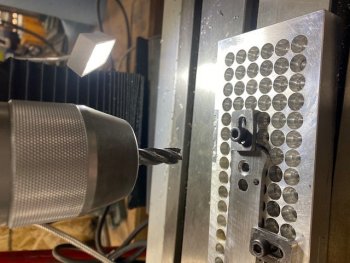
Using a height gauge I scribe the edge down .050". I am shocked I don't have solid blue fingers after using they Dykum.
These height gauges can be picked up for under a $100 and I seem to use it on every folder I do. Make sure it has a carbide point so you can use it to scribe your blade edge before grinding.
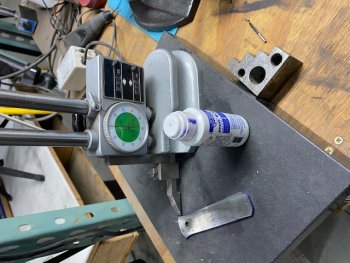
Now I need to convex the handles. I drilled and tapped a 1" piece of stock and screwed on a handle.
I can't do it and take a picture so basically I hold it like this to the flat platen and rotate it on the vertical axis.
and finally today, see the gooseneck light? It's called a sewing machine light. There are several kinds on Amazon. This one has 30 little LED lights, a magnetic base and 12" flexible goose neck. I think it was like $15. These are flat awesome. I have them on two grinders and my drill press here. Highly recommended.
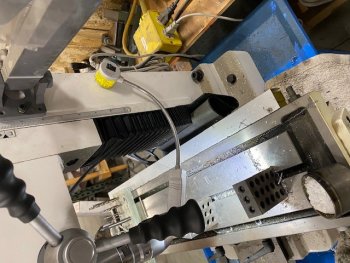