After taking the summer off from knife making to concentrate on fishing.... I am back at it since the boat is winterized and the lake isn't frozen yet.
Below is a scale release auto in progress. The green g10 chunk screwed to where the scale goes is simply something to give me a grip.
I had to re-solder one bolster since I found a gap when cleaning it up. I tried just filling in the gap but naturally that didn't work so I melted it off, cleaned it all up and re-soldered it. I think it will work.
Here is a peek inside. The spring is hardened and tempered 8670. The back lock bar is something stainless I made last spring. The blade is elmax and is my 3rd blade for this build since I screwed the first two up.
My coil is getting pretty beat up. I replaced this one. Here the coil fit's into a small groove in the blade to give it more clearance. The liner bolster wasn't thick enough to take the whole coil height. Try not to notice the horrible file work for the lock. I cleaned that up since this picture.
The coil was binding a bit so I added a very small washer that fit's inside of the ID of the coil. This gave me just enough clearance to reduce friction on the blade and liner.
Left to right: The slug (used as a washer), the little bali washer I added and the coil.
The "slug" is a piece of liner that tends to fall off the soldered bolster when you drill the pocket. It is usually saved and used as a thick washer.
I don't care for the geometry of the lock bar. I think the pivot screw (center) should move up a bit but I am going to finish this one and see how it works.
Here is the coil in the pocket with the slug and extra washer. As a coil is tightened, the ID shrinks so it has to be smaller than the ID under tension. You can see the circle wear marks from the blade tang where it rubbed prior to adding this .010" washer.
While the blade is in the oven I am working on the scales. This is elephant ivory I bartered with Howard Clark for last winter. It's been years since I messed with any ivory. I was scared to drill it as I normally mess up and put a hole in where it doesn't belong. I stared at these for sometime triple checking my work before I finally drilled the holes.
It stinks when you grind it.
Just after I had ground the profile down I stepped out of the shop because the dust/stink was still heavy. I walked back in and found Luke walking around sniffing for something that "smelled bad like burning".
It really stinks and I don't mind not using it that often.
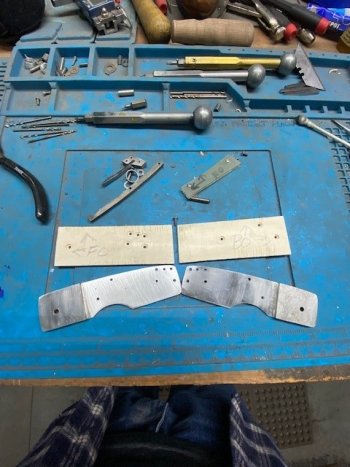