Dennis Morland
KNIFE MAKER
Back side is cleaned up.
Looks good with the handle in place.
I got the edge cleaned up, also. I will get a picture when I get the front cleaned up. Tomorrow??
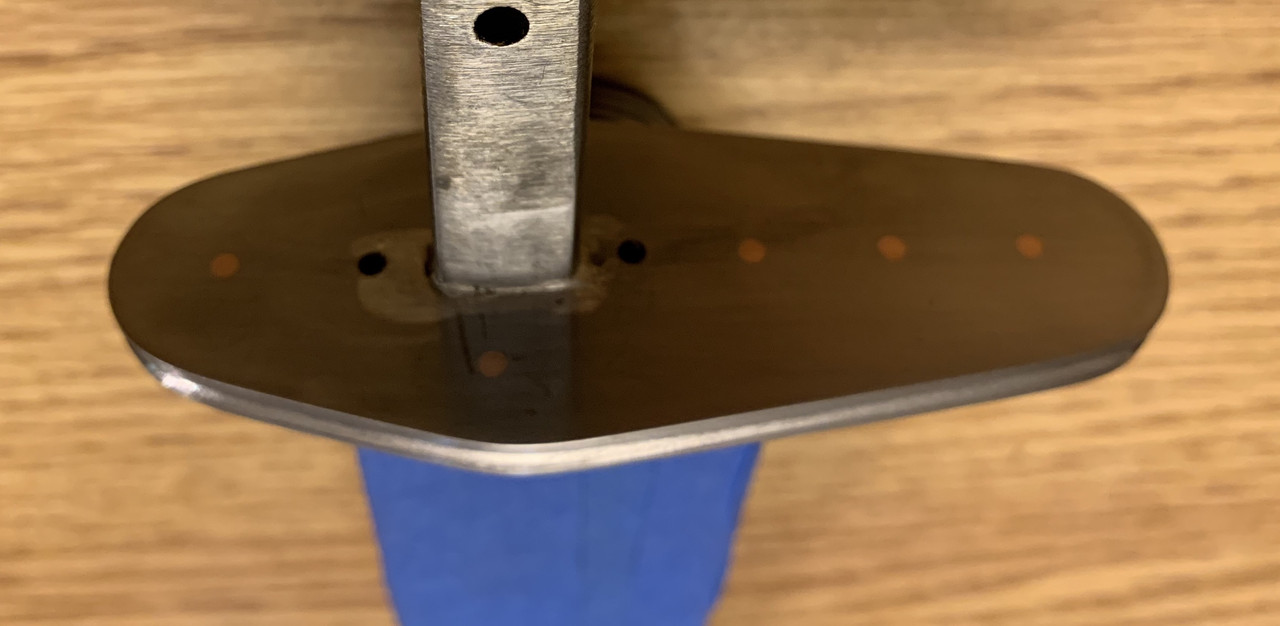
Looks good with the handle in place.
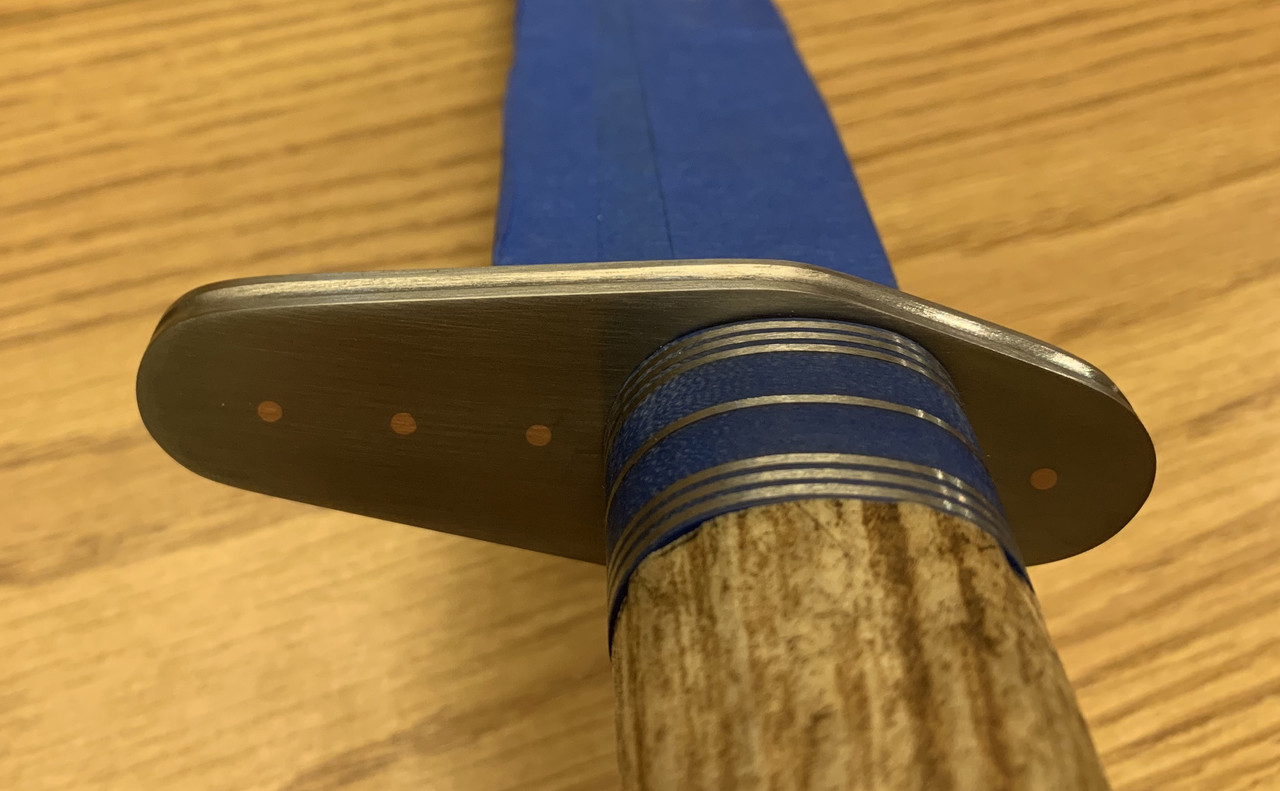
I got the edge cleaned up, also. I will get a picture when I get the front cleaned up. Tomorrow??