For years I have wanted to get into auto folders. I am finally getting started.
This will be a dual action using a bar lever. Dual action is one you can open manually, just like any other liner lock or open using the button (or lever bar in this case) an it will open like an auto. I hear this often called a double action and I could be wrong but that is more correctly used to describe an out the front that will be both open and close the knife by a slide bar.
the top drawing is for the lever bar. Peter Martin sent me a hand sketch of what he has used so I put it into CAD just to have a reference. I do not have anything figured out for the lever bar pivot pin lugs yet. I will probably make some lugs that screw into the liner. I will try TIG welding some lugs onto scrap and see how it works. Many guys solder the lugs in place also.
The bottom is a "sketch" (basically a solidworks term for not a finished, fully constrained drawing). I print these out, glue them onto pattern material and use the hardened pattern to make the actual pieces. The curved wire from the rear of the knife to the kick face on the blade is the leaf spring. That is held in place, when charged, by the button bar lug. When the knife is closed, the spring is charged and held open by the lug on the button bar. The blade can open and close manually with the spring held in place. The button can be activated, releasing the leaf spring, kicking the blade out. When you close the blade, the spring is charged again.
I am stepping up the detent ball to 3/32" from a 2mm ball because I think it will hold better. The detent ball does not hold the spring back so it all has to be clocked perfectly. I hope I don't screw this up ten times trying to get it figured out.
The two metal pieces just under the sketch are my pattern pieces I made and hardened yesterday.
The very bottom pieces are the liners I profiled, drilled tapped and screwed together to check alignment. The wire is .067" piano wire and will be the kick spring.
At this point I am guessing: I will get the liner lock working, then locate the lever bar and mount that, then work on tuning it, then locate and drill the detent ball socket. There is more but that is enough for now.
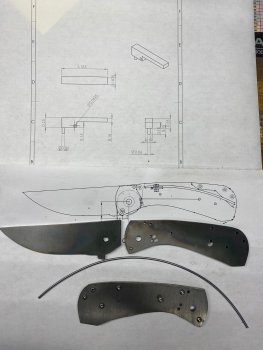