This whole exercise is just something I have wanted to try for a very long time and so I am trying it. I saw this technique used by Ron Lake 20 some years ago and never got around to it. Now I am. Better late than never.
This is a shot of the positive pattern and resulting end product. The g10 went in with a little hammer persuasion. There is a visible gap but I think that is me and not the process.
Here is what I ended up with. I will use the partial cut out as a grind to line. There is going to have to be some manual fitting. I can't see any way around that right now.
The positive pattern and g10 slug or insert material. The g10 is super glued to the support plate.
This is how it goes on the mill. you lower the spindle down and move the entire thing around the positive pattern. The cutter shank smooth part is used to rub against the pattern.
Top view.
Side view.
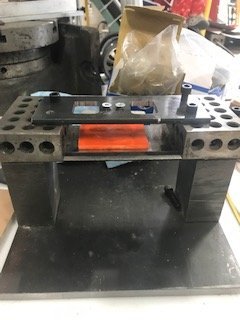
The Cerosafe positive. This was stupidly easy to cast. I set the negative pattern on top of a plate of steel and using a torch melted part of the cerosafe into the cavity. It popped right out with a hammer and punch.
Will this process work? Maybe. I still have to dial in a few things and do a couple more practice runs. I'm pretty confident about making the negative cavity. I'm less positive about the positive (hah!) pattern process. We'll see.
Before anyone suggests CNC. I have a full size CNC mill and could do this process with it until electricity runs out. That isn't the point. This is just one of those things on a list I made long ago and I want it to work or it's off the list.