I am keen to get comfortable making framelock folders so thought that sharing some WIP would both help me to document my process but also allow comment tips and critique so please let me know your thoughts as this goes on. It won’t be quick as I will need to get a few blades ready for HT as I will be send them out and cost is same for 1 as it is for 5 blades. So it will be a couple of months I think before I get to finishing stage but I figure that speed is not the name of the game here and time in the shed is limited both by the weather (heat) and life!
So I started out with paper and French curves to work out my design, using a pin for pivot point and making various changes until I think I have a design that will both work and is in a style I like.
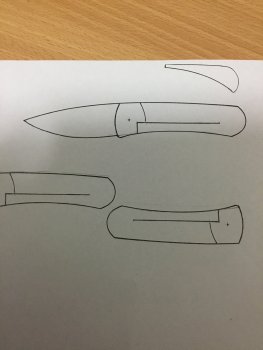
So I started out with paper and French curves to work out my design, using a pin for pivot point and making various changes until I think I have a design that will both work and is in a style I like.
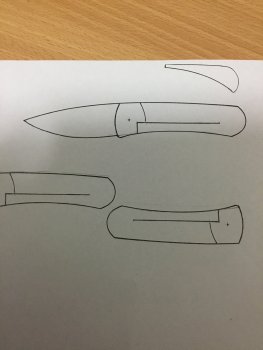