Gene Kimmi
KNIFE MAKER
I've been wanting to experiment with different things to dress up the handles on my knives. Tonight I had some free time, so I practiced doing an inlay. I cut a groove with a 3/8" end mill then sanded a piece of walnut to fit. Then I decided to try checkering for the first time.
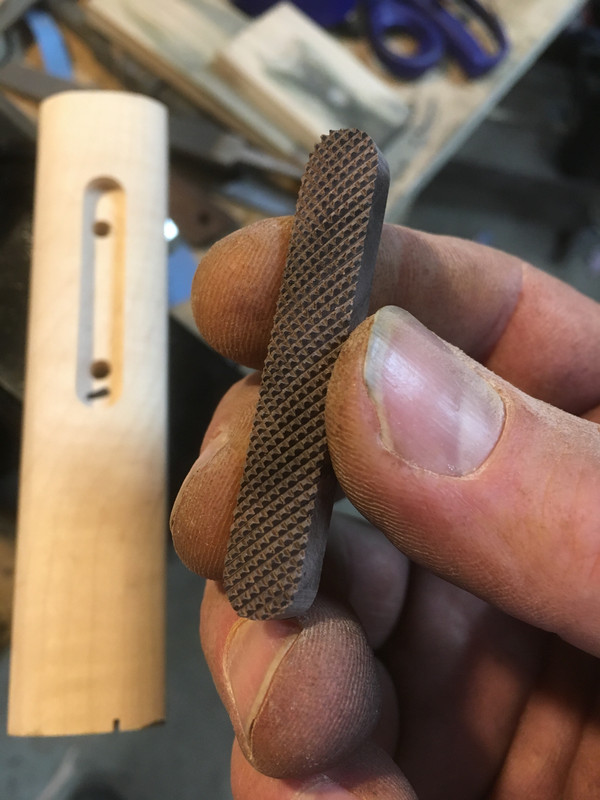
018-01-24_22.41.29.jpg[/img][/url]
Now to see how many handles I can destroy before I get one done right.
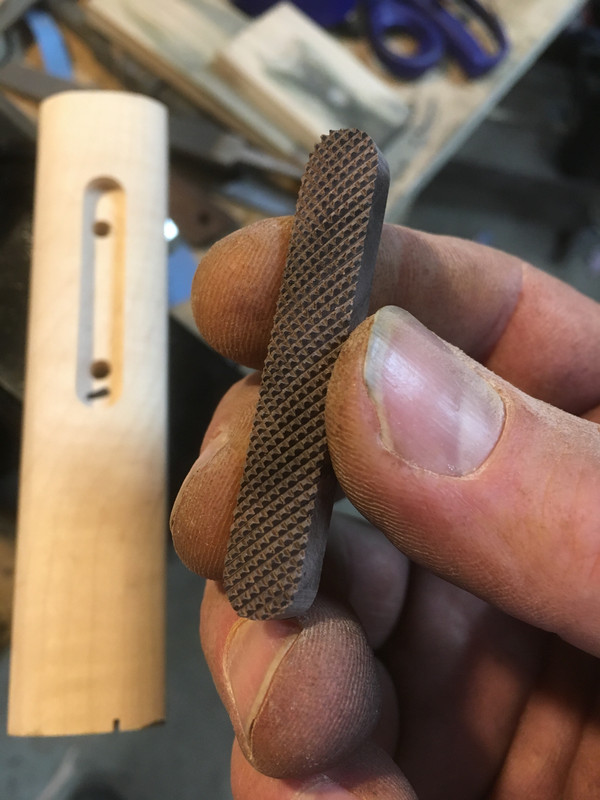

Now to see how many handles I can destroy before I get one done right.
Last edited: