Bruce Bump
Forum Owner-Moderator
I cut a set of oversized bolsters from 1/8" 410 stainless on the bandsaw, drilled a 3/32" hole through each, pinned them to the liner template and rough ground the profile very close to actual size. I pinned the two together and matched them on the scale side on the disc. They need to be exactly the same. Be sure to clean up the back side for a clean solder joint.
Next I "tinned" the back side of each bolster and the ends of each liner. "Tinning" simply means to flux and put a drop of solder with heat to be sure there is no contamination or voids in the joint. Simply flux and heat, use a solder brush to spread the flux and add some solder, spread the solder around and work it back and forth until the entire surface is tinned.
Run the same drill bit through the liner and bolster holes just to clean out any solder inside the holes. Using a sharpened high speed steel drill bit, rub a pencil on it to coat it with lead. Solder wont stick to lead, dont ask me why. Now simply pin the bolster to the liner with the leaded pin and clamp them being sure they are square with the liners. Add one drop of flux so it can seep inside the joint and heat slowly with a propane torch. No need for a big flame as this is only 400 degree silver solder. Rotate the assembly so its get even heat on all sides and watch for the solder to begin to melt. As the solder melts the clamp will automatically squeeze the two together and give a seamless joint. Use the solder brush to wisk away excess solder as it seeps out of the joint. Dont overheat, just take your time so its nice and even. No mental stress at all and perfect seam joint every time. When you are satisfied the excess solder is squeezed out of the joint quickly cool it under cold running water. The brass rod poked inside the golf ball is one of my most sophisticated tools and easily cleans off the remainder of the solder. Wash everything with soap and water to clean any flux that could be remaining on the parts. You dont need flux on anything as it can leave rusty finger prints everywhere you touch especially on the hand rubbed 2000 grit feather damascus blade.
note, if you paid enough attention you noticed that a couple of the photos are of Bruce Barnettes slippie bolsters he is making here. He is here for a week on his way back to Australia from the Blade Show.
Next I "tinned" the back side of each bolster and the ends of each liner. "Tinning" simply means to flux and put a drop of solder with heat to be sure there is no contamination or voids in the joint. Simply flux and heat, use a solder brush to spread the flux and add some solder, spread the solder around and work it back and forth until the entire surface is tinned.
Run the same drill bit through the liner and bolster holes just to clean out any solder inside the holes. Using a sharpened high speed steel drill bit, rub a pencil on it to coat it with lead. Solder wont stick to lead, dont ask me why. Now simply pin the bolster to the liner with the leaded pin and clamp them being sure they are square with the liners. Add one drop of flux so it can seep inside the joint and heat slowly with a propane torch. No need for a big flame as this is only 400 degree silver solder. Rotate the assembly so its get even heat on all sides and watch for the solder to begin to melt. As the solder melts the clamp will automatically squeeze the two together and give a seamless joint. Use the solder brush to wisk away excess solder as it seeps out of the joint. Dont overheat, just take your time so its nice and even. No mental stress at all and perfect seam joint every time. When you are satisfied the excess solder is squeezed out of the joint quickly cool it under cold running water. The brass rod poked inside the golf ball is one of my most sophisticated tools and easily cleans off the remainder of the solder. Wash everything with soap and water to clean any flux that could be remaining on the parts. You dont need flux on anything as it can leave rusty finger prints everywhere you touch especially on the hand rubbed 2000 grit feather damascus blade.
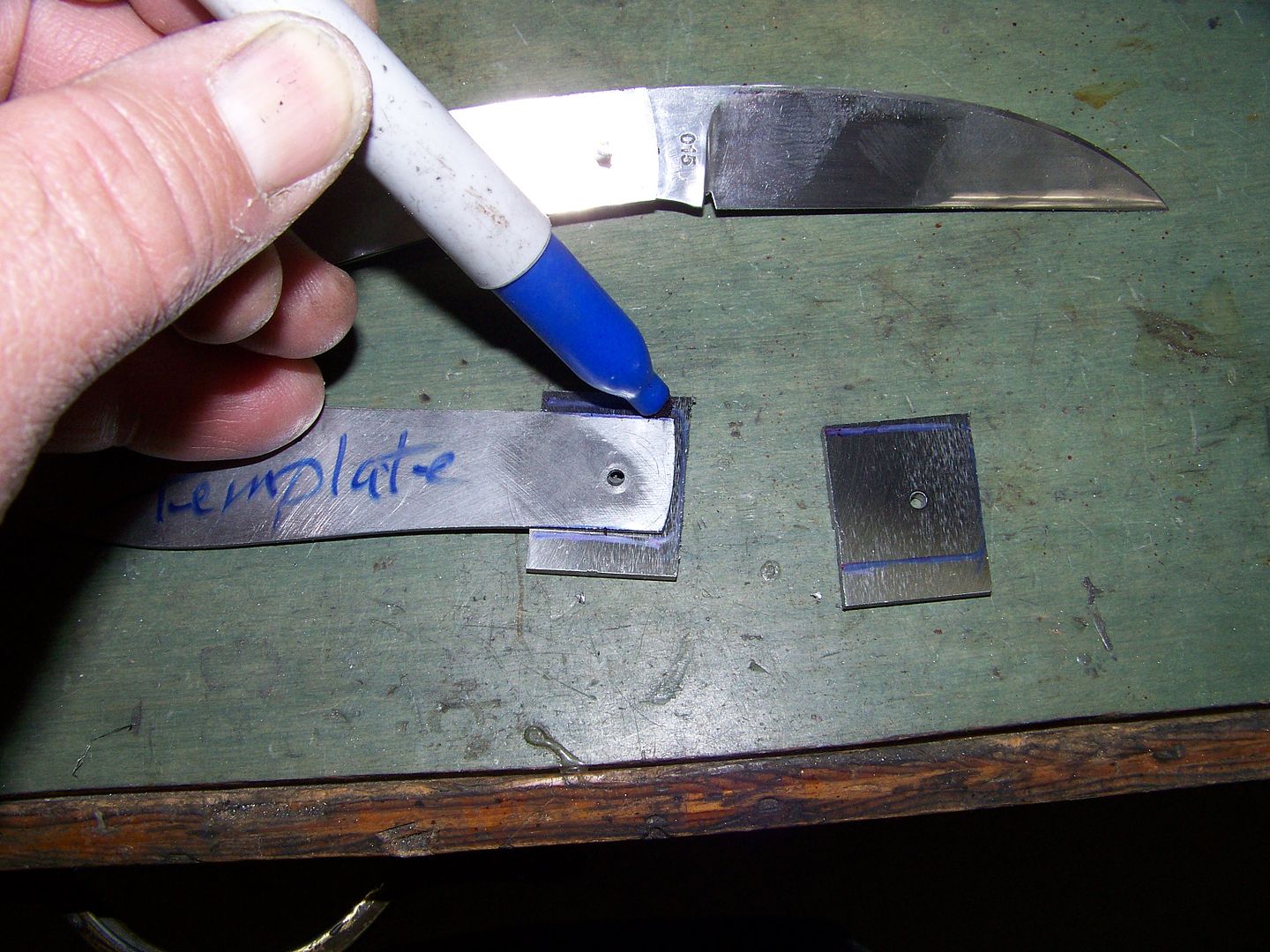
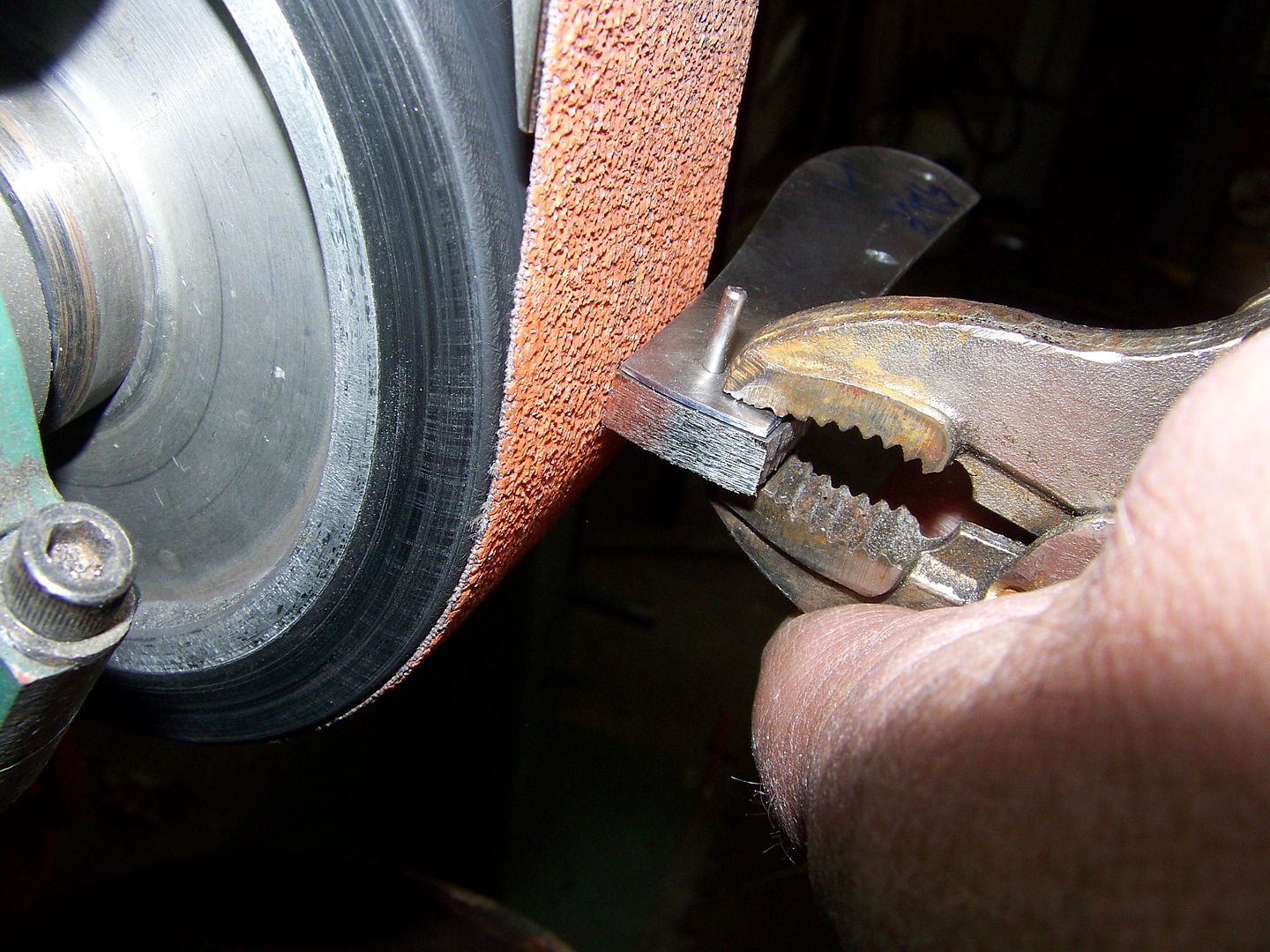
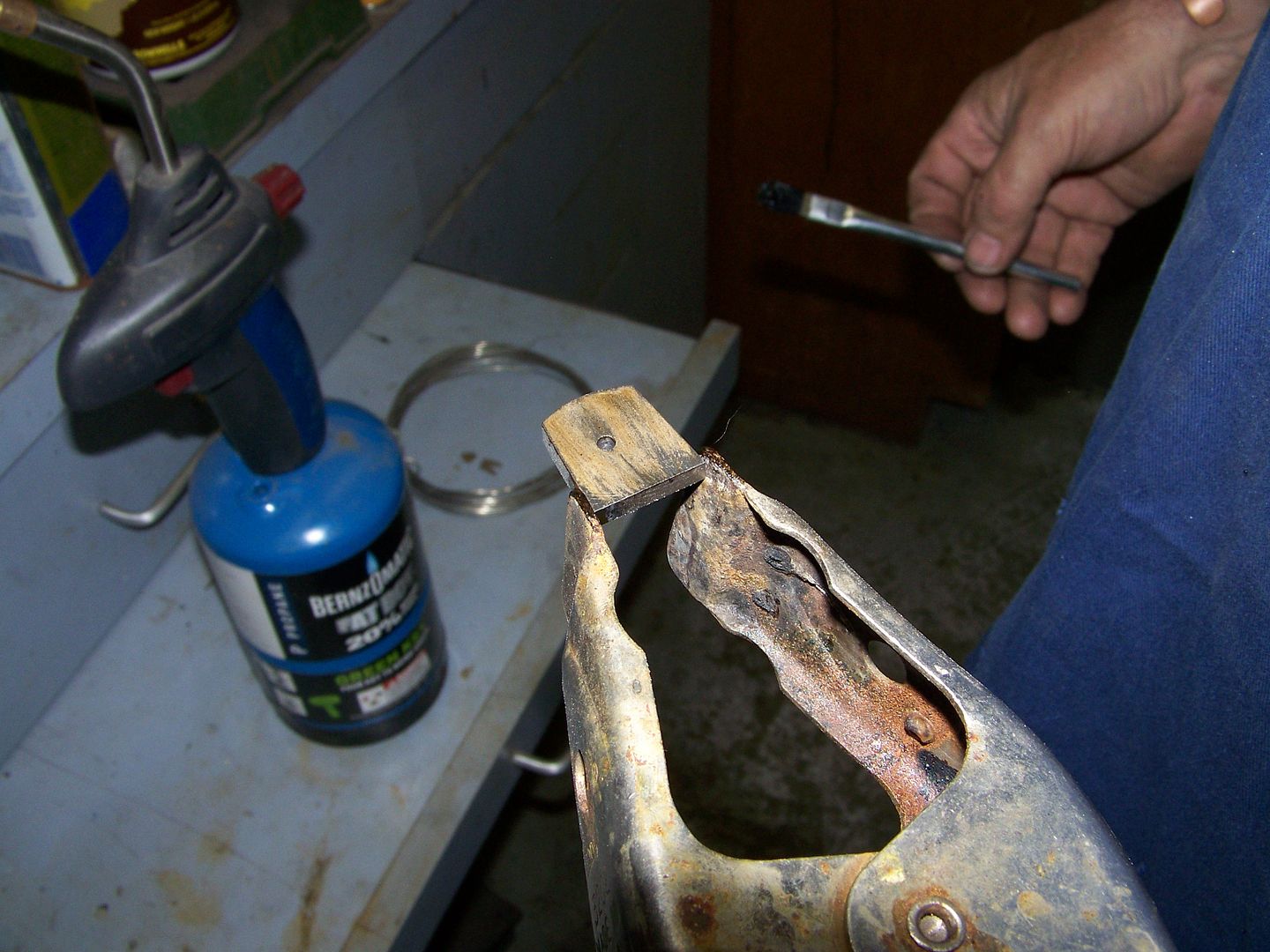
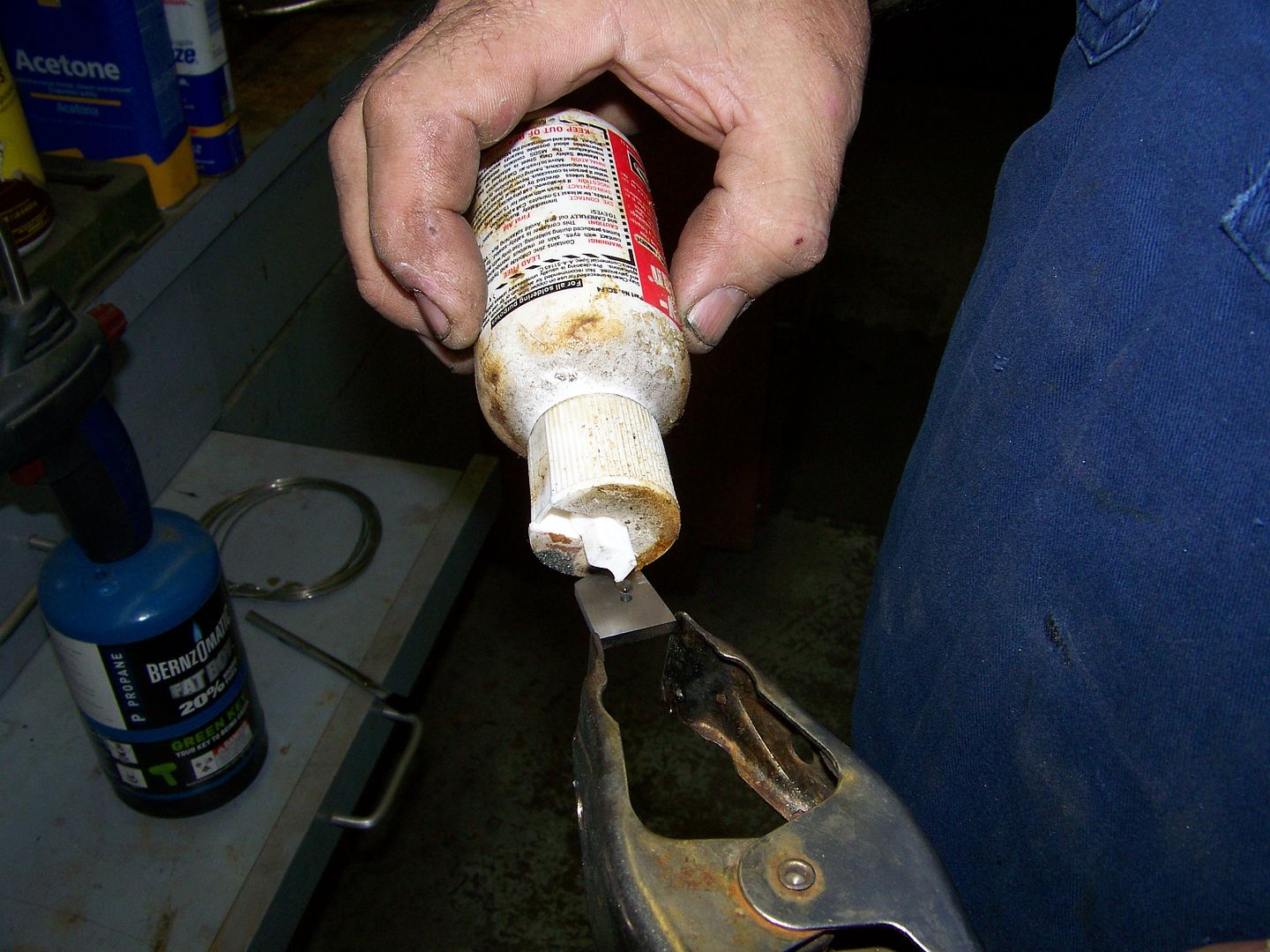
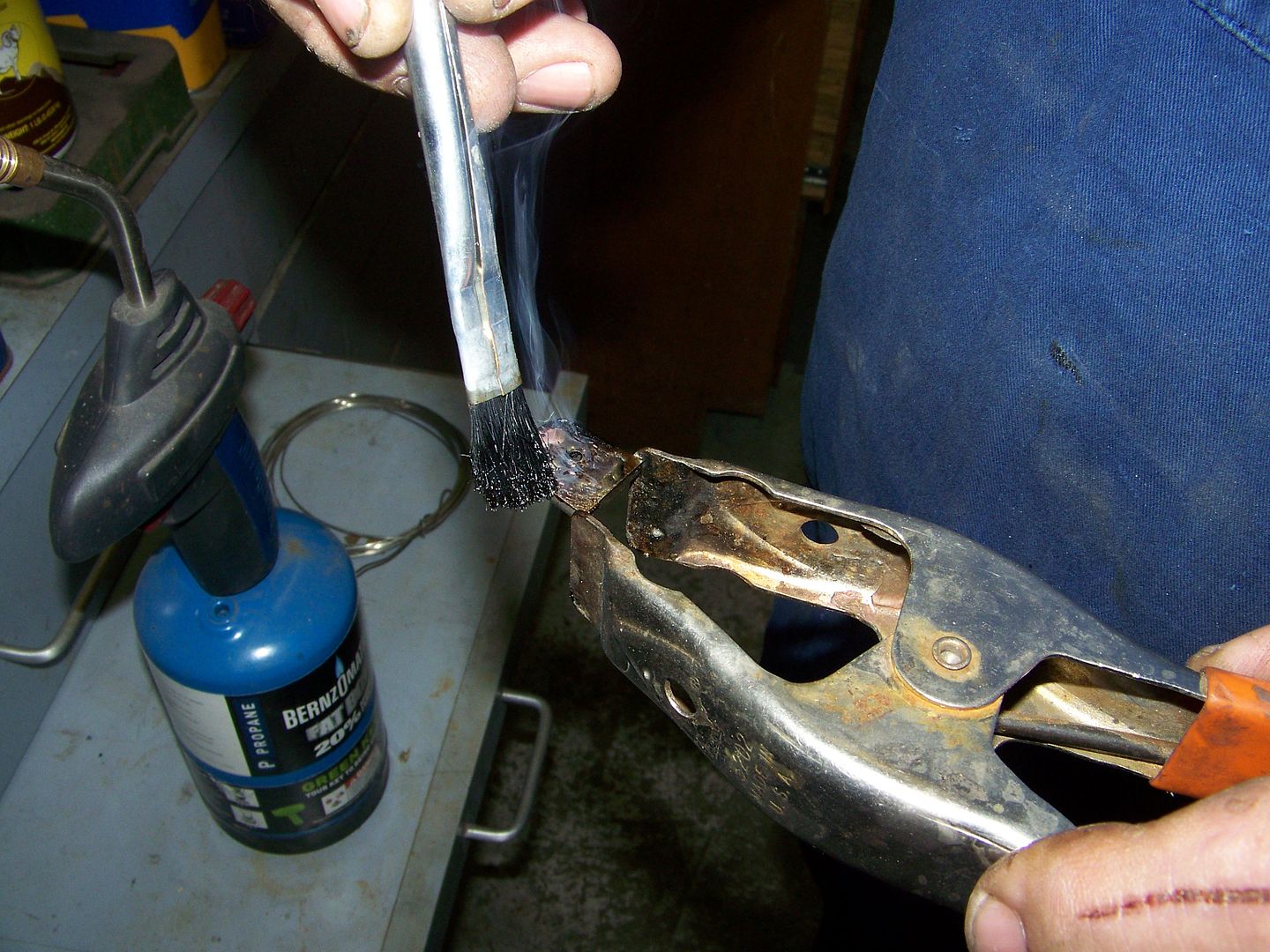
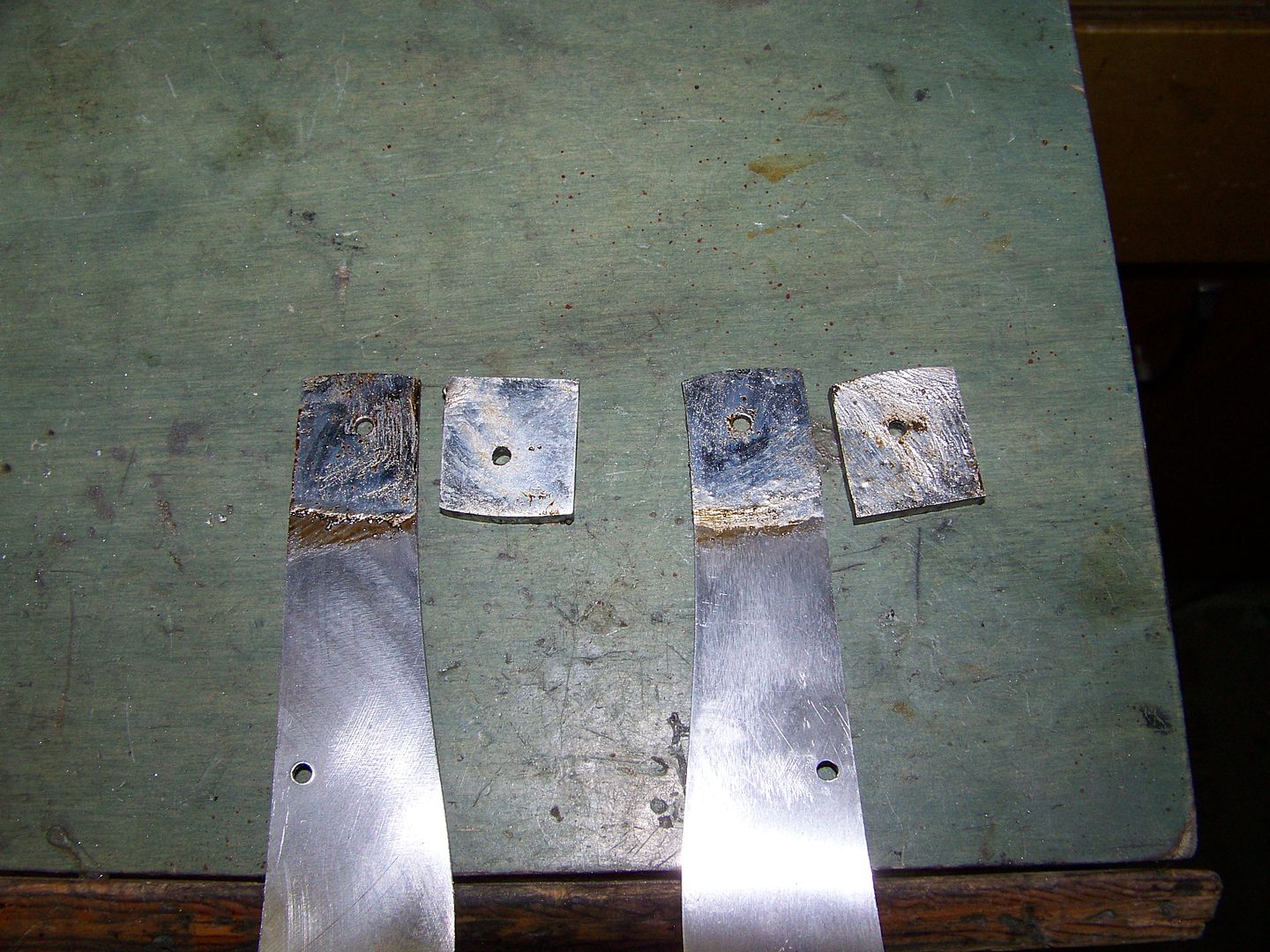
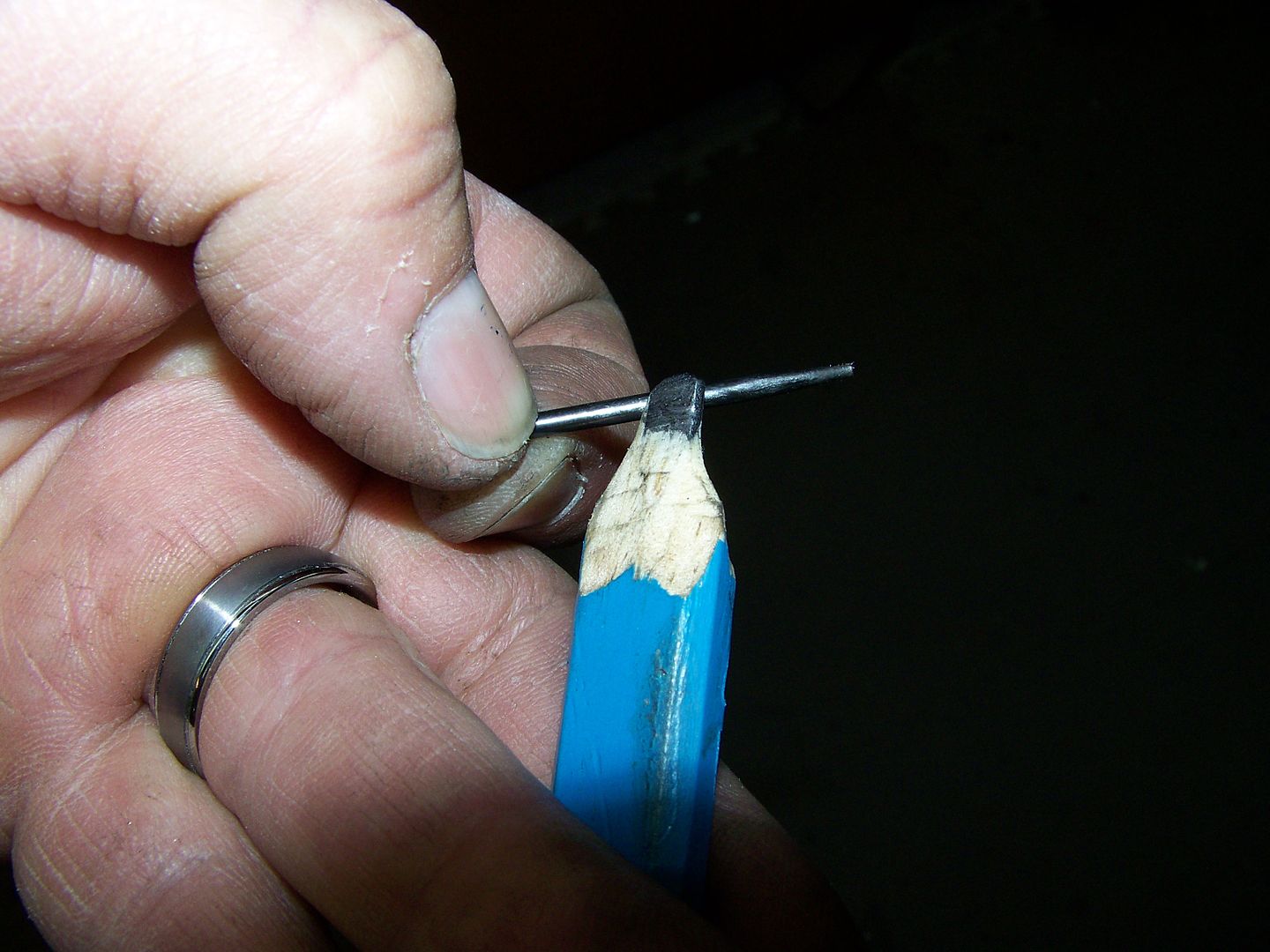
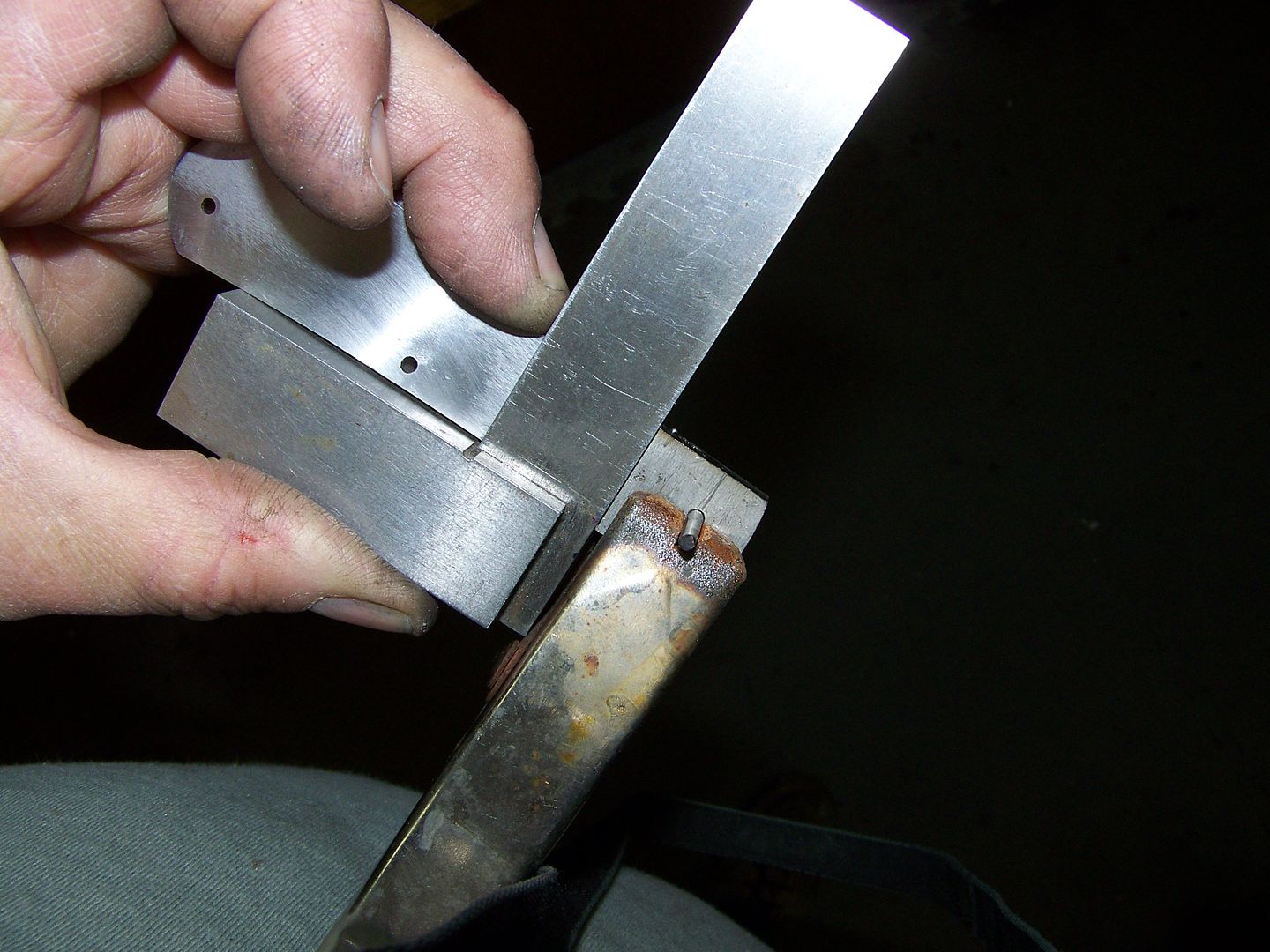
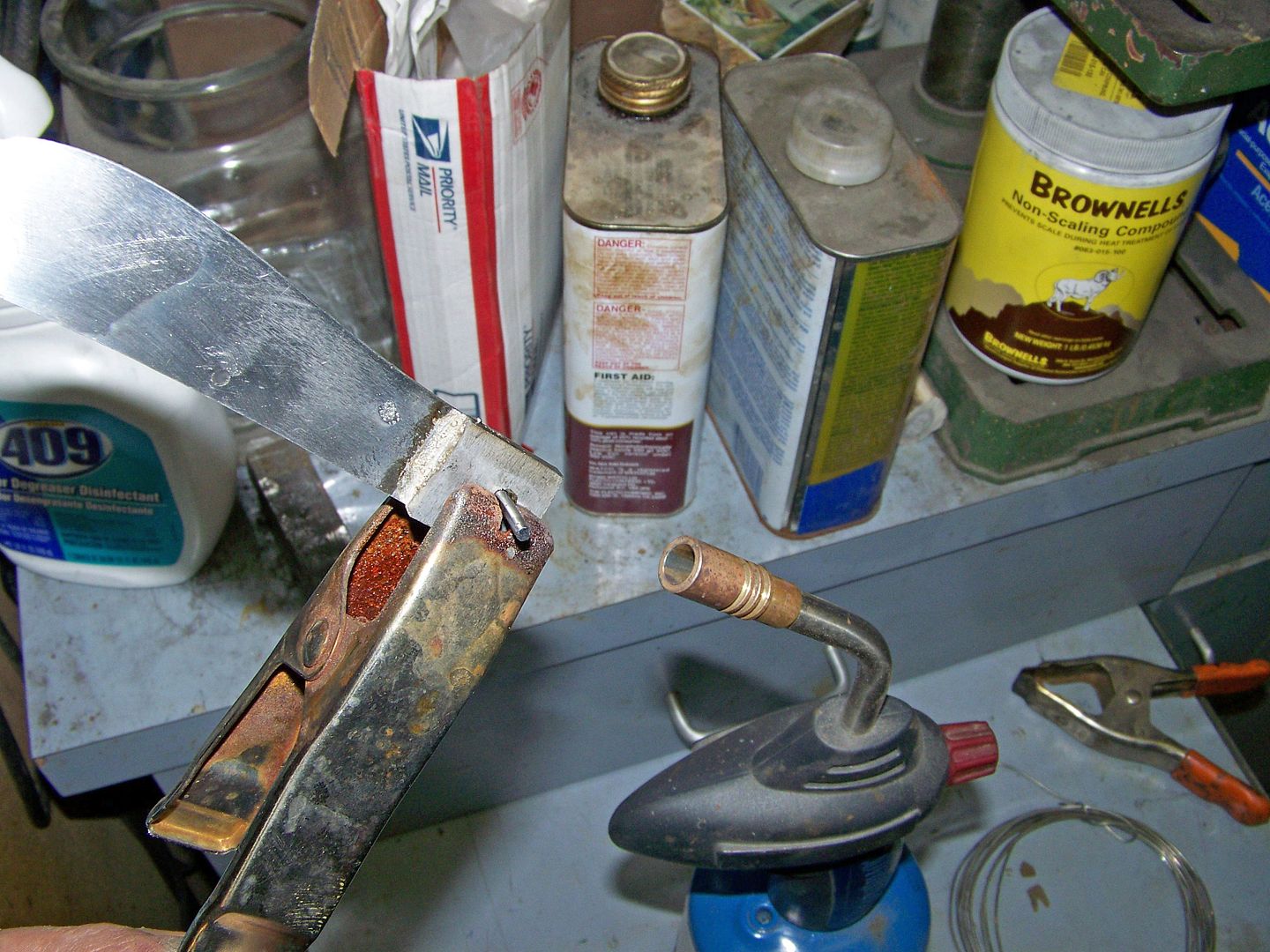
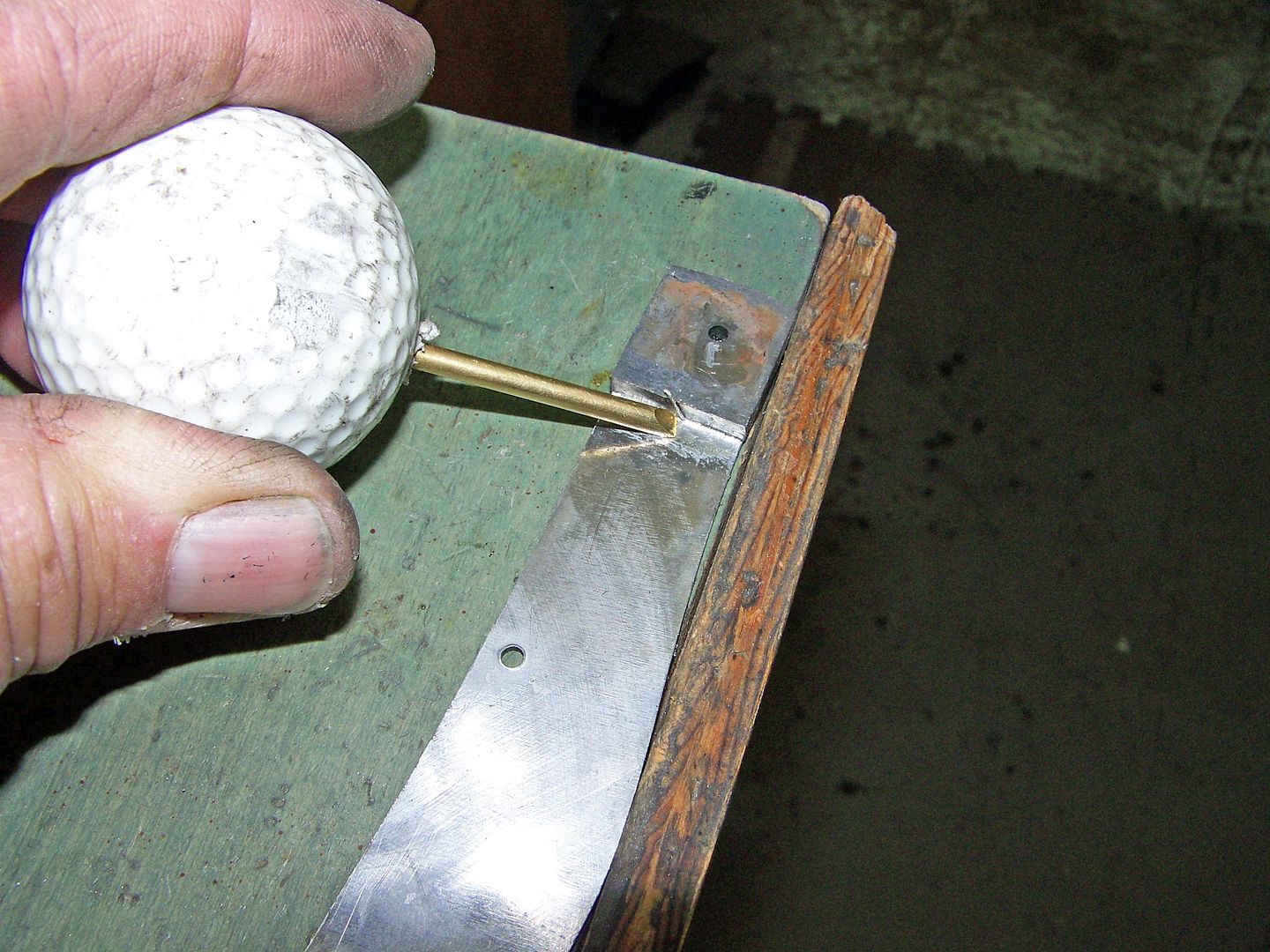
note, if you paid enough attention you noticed that a couple of the photos are of Bruce Barnettes slippie bolsters he is making here. He is here for a week on his way back to Australia from the Blade Show.
Last edited: