J. Doyle
Dealer - Purveyor
I have to catch a couple other blades up to this one before heat treating but I have a couple more pics and some commentary on some fine details about the ricasso area.
The ricasso area is the most important area, from a design standpoint, on a knife. Its an important area to focus on at different times, for different reasons during a build. This one has some cosmetic issues to my eye right now but I'll address them later and they serve a purpose now.
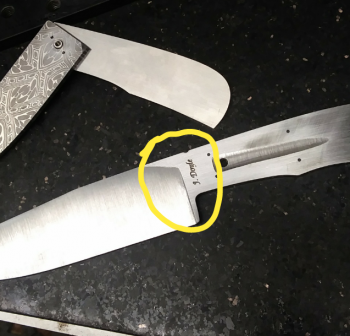
The ricasso area is the most important area, from a design standpoint, on a knife. Its an important area to focus on at different times, for different reasons during a build. This one has some cosmetic issues to my eye right now but I'll address them later and they serve a purpose now.
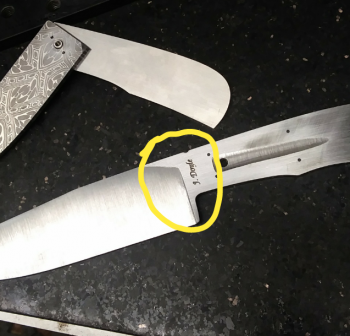