MTBob
Well-Known Member
Actually Polymorph Plastic - Sorry for the cheesy click bait subject line, couldn't resist.
Here's the story. Long ago I purchased a Japanese cleaver and over the years it has suffered from heavy use and eventually a broken handle. To repair this I want to make a WA Style handle with a solid brass end fitting. This seemed pretty simple until I closely looked at the tang and found it to be both tapered lengthwise and had an irregular trapezoidal-like cross section. That prohibited any kind of symmetrical / parallel layout of the hole. After a lot of head scratching I though of the jar of Polymorph Plastic that has been banging around the shop for years and never used. This plastic is also called Thermoplastic, Moldable Plastic, InstaMorph, etc. - See Amazon for a bunch of inexpensive purchase options.
It is almost rock hard at room temperature but becomes very moldable by hand at 150F. I submerge the plastic polymorph (comes in tiny pellets) in water and microwave them for about a minute. Check out YouTube for details of how to work with this stuff - it's really simple.
Here's the method I used to get a profile of the knife tang:
First, to test the plastic's strength, I made a razor blade holder. Once cooled to room temp the handle is very hard and holds the blade solid.
To get the shape of the cross section I pushed a chunk of warm plastic over the tang and let it cool (mostly)
c
While slightly soft, I sliced a section of the plastic (using my new razor blade knife) short of where the brass fitting will go. Now I have the outline of the tang shape.
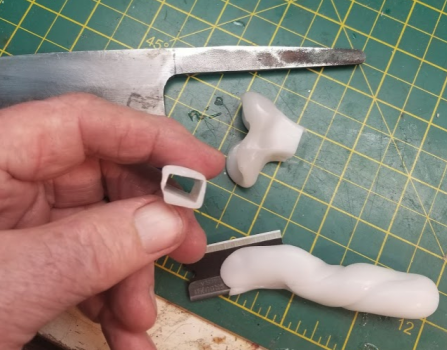
I then used that template to outline the position of the tang hole on the brass fitting.
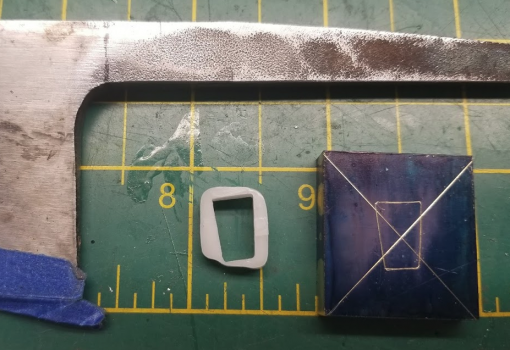
Then it's just a matter of milling out the relief on the back side and roughing out the tang shape based on the scribe lines - then finishing with files and swagging to fit.
If the handle turns out satisfactorily I'll do a post of that later.
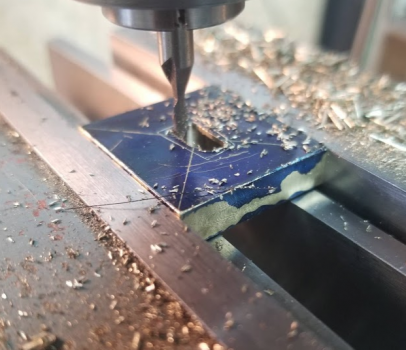
This moldable plastic is a tough, really cheap and reusable material for making or copying shapes. The applications are endless.
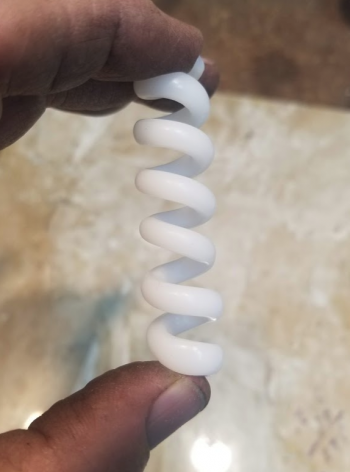
Here's the story. Long ago I purchased a Japanese cleaver and over the years it has suffered from heavy use and eventually a broken handle. To repair this I want to make a WA Style handle with a solid brass end fitting. This seemed pretty simple until I closely looked at the tang and found it to be both tapered lengthwise and had an irregular trapezoidal-like cross section. That prohibited any kind of symmetrical / parallel layout of the hole. After a lot of head scratching I though of the jar of Polymorph Plastic that has been banging around the shop for years and never used. This plastic is also called Thermoplastic, Moldable Plastic, InstaMorph, etc. - See Amazon for a bunch of inexpensive purchase options.
It is almost rock hard at room temperature but becomes very moldable by hand at 150F. I submerge the plastic polymorph (comes in tiny pellets) in water and microwave them for about a minute. Check out YouTube for details of how to work with this stuff - it's really simple.
Here's the method I used to get a profile of the knife tang:
First, to test the plastic's strength, I made a razor blade holder. Once cooled to room temp the handle is very hard and holds the blade solid.
To get the shape of the cross section I pushed a chunk of warm plastic over the tang and let it cool (mostly)
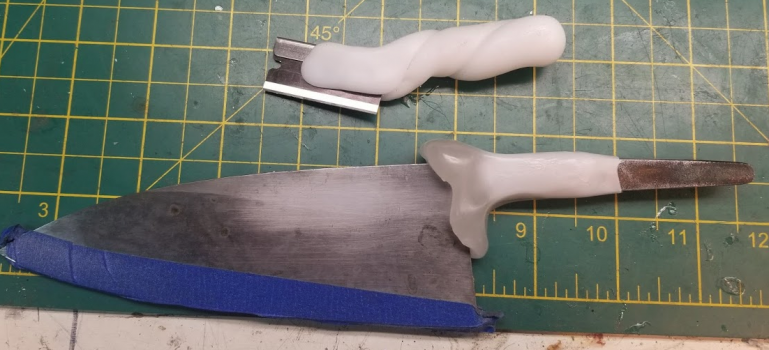
While slightly soft, I sliced a section of the plastic (using my new razor blade knife) short of where the brass fitting will go. Now I have the outline of the tang shape.
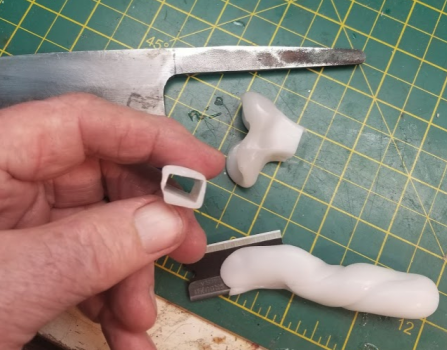
I then used that template to outline the position of the tang hole on the brass fitting.
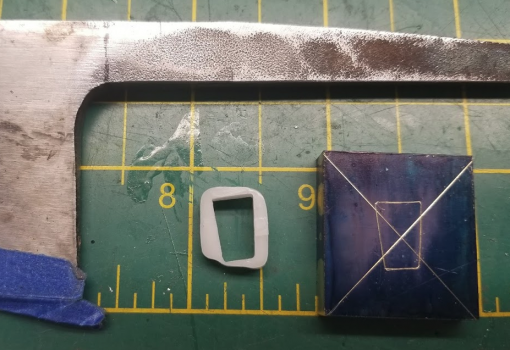
Then it's just a matter of milling out the relief on the back side and roughing out the tang shape based on the scribe lines - then finishing with files and swagging to fit.
If the handle turns out satisfactorily I'll do a post of that later.
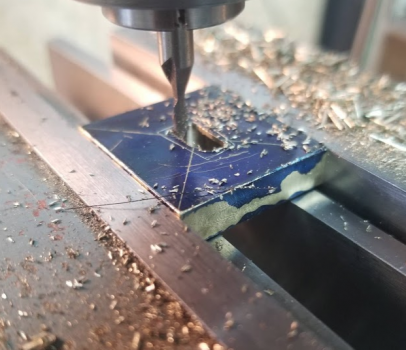
This moldable plastic is a tough, really cheap and reusable material for making or copying shapes. The applications are endless.
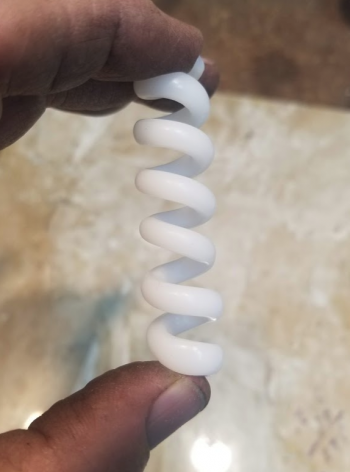