tkroenlein
Well-Known Member
Well, I finally got started. After much frittering around, I opted to use 80CrV2 for my wrought iron San-Mai blade. The frittering wasn't so much the steel choice but the size. I've got a pretty good selection of wrought iron to choose from, but I wasn't sure how successful I'd be drawing down much thicker or wider stuff as far as how many heats I'd have to do and risk degrading the steel and/or crack or delaminate.
With much uncertainty, I started with 3/16" x 1" x 8" blade steel and 1/8" x 1" wrought.
I MIG welded each side about 1" apart after slicking it all up real good.
I also welded welded fluxless, as that's all I've ever done. Wasn't sure if wrought needed flux or not, but I did put the time into prep and my forge (NC whisper low boy) seems to create a reducing atmosphere all on its own, so I went for it.
I did 3 "welding" heats, the first taking about 20 seconds out of the forge. On the second heat, it had that real satisfying welded feel under the hammer, and one more to make sure.
It took surprisingly few heats to get it drawn out considering how easy I went at it. I did about 10 heats or so before a used the rounding hammer, and I was done a few after that. Looks like the billet will clean up at about 1 1/4" x 10" x 1/4", with just about a 1/16" of wrought on each side, which should work out great.
I took the trouble to write all this part out because I found surprisingly little about wrought iron San-Mai forge welding. Maybe this will help somebody. Or ruin them. Who knows.
There will be minimal forging from here on out apart from drawing out the tang, which I'll quickly abort as well if it goes sideways. I should manage 7" for the blade/ricasso, and plenty for the tang. I'll cut/grind the blade to shape from there.
Gratuitous pics.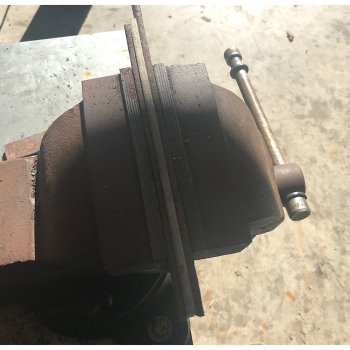
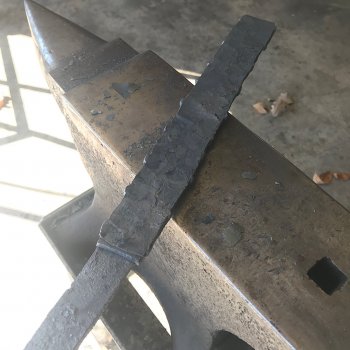
With much uncertainty, I started with 3/16" x 1" x 8" blade steel and 1/8" x 1" wrought.
I MIG welded each side about 1" apart after slicking it all up real good.
I also welded welded fluxless, as that's all I've ever done. Wasn't sure if wrought needed flux or not, but I did put the time into prep and my forge (NC whisper low boy) seems to create a reducing atmosphere all on its own, so I went for it.
I did 3 "welding" heats, the first taking about 20 seconds out of the forge. On the second heat, it had that real satisfying welded feel under the hammer, and one more to make sure.
It took surprisingly few heats to get it drawn out considering how easy I went at it. I did about 10 heats or so before a used the rounding hammer, and I was done a few after that. Looks like the billet will clean up at about 1 1/4" x 10" x 1/4", with just about a 1/16" of wrought on each side, which should work out great.
I took the trouble to write all this part out because I found surprisingly little about wrought iron San-Mai forge welding. Maybe this will help somebody. Or ruin them. Who knows.
There will be minimal forging from here on out apart from drawing out the tang, which I'll quickly abort as well if it goes sideways. I should manage 7" for the blade/ricasso, and plenty for the tang. I'll cut/grind the blade to shape from there.
Gratuitous pics.
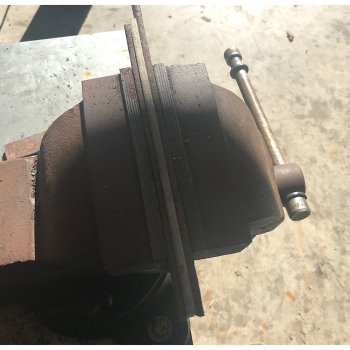
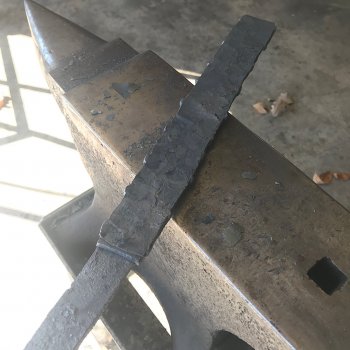