Karl B. Andersen
Well-Known Member
I'm in the process of getting three sheaths done so I can get some knives shipped out, but I was able to get the "Alaskan" hardened and tempered yesterday.
This is a shot of the post-tempering clean-up without any etching.
I will wait until the knife is completely built before I etch the blade.
I can see now that I achieved my intentions during the hardening process to produce this hamon.
This is a shot of the post-tempering clean-up without any etching.
I will wait until the knife is completely built before I etch the blade.
I can see now that I achieved my intentions during the hardening process to produce this hamon.
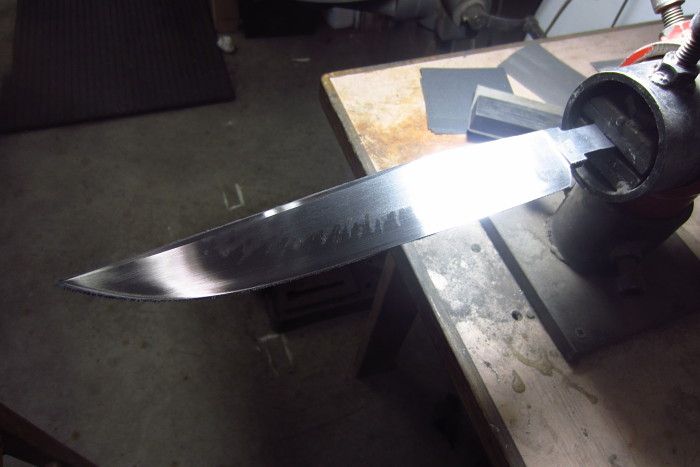