Gliden07
Well-Known Member
Well I've collected most of the parts for the gas part for the burners, got the Kiln shelf cut and fitted. Need to cut the rear door out and figure out what I want for front and rear shelves to support the fire brick to help keep heat in forge. Then it will be time to get messy with the Satinite and ITC.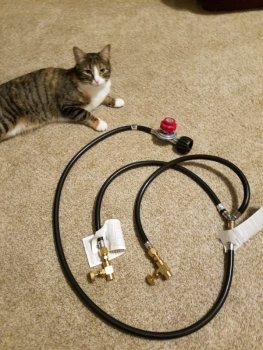
These are all the hoses and most of the valves (still need a ball valve for shut off) 30PSI regulator, 2 needle valves to adjust pressure at the burners so I can balance them. And that is my model Zoe!!
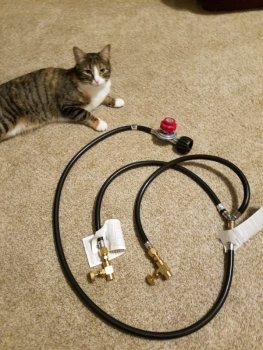
These are all the hoses and most of the valves (still need a ball valve for shut off) 30PSI regulator, 2 needle valves to adjust pressure at the burners so I can balance them. And that is my model Zoe!!
Last edited: