MTBob
Well-Known Member
With great apprehension I'm taking the plunge and getting started on the KITH for Fred Kingery.
And just to keep my blood pressure off the chart, I've decided to try something that I've screwed up several times - making a multipart handle. What a better way to truly embarrass myself than trying something that I've not been able to figure out how to do - - in front of a couple hundred expert knife makers OMG.
Based on advice from a wise knife maker who lives in Florida (Fred), I've opted to not use wood in the handles due to the high humidity differences between Montana and Florida. So, I'm planning on using Ivory and Black G-10 for handle scales, . I'm currently thinking of using vintage micarta for the liner and spacer., though that may change.
Typically, I've never planned out a knife like this. But, I thought it would give you'all a chance to give me some serious critique before I got too far along.
Before I even begin cutting steel, I'm going to figure out a method to make the multi-part handle scales.
I'm an old geezer with thick skin.... so let the comments roll!
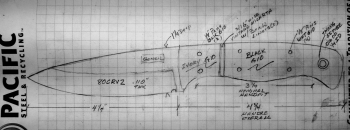
And just to keep my blood pressure off the chart, I've decided to try something that I've screwed up several times - making a multipart handle. What a better way to truly embarrass myself than trying something that I've not been able to figure out how to do - - in front of a couple hundred expert knife makers OMG.
Based on advice from a wise knife maker who lives in Florida (Fred), I've opted to not use wood in the handles due to the high humidity differences between Montana and Florida. So, I'm planning on using Ivory and Black G-10 for handle scales, . I'm currently thinking of using vintage micarta for the liner and spacer., though that may change.
Typically, I've never planned out a knife like this. But, I thought it would give you'all a chance to give me some serious critique before I got too far along.
Before I even begin cutting steel, I'm going to figure out a method to make the multi-part handle scales.
I'm an old geezer with thick skin.... so let the comments roll!
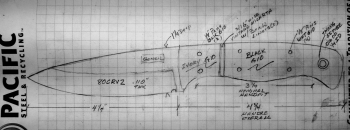