MTBob
Well-Known Member
I recently purchased a Paragon KM18t 3 element Pro. This furnace has a Bartlett Sentinel Controller that is very easy to use. It incorporates a WiFi connection that allows access to the stored heating cycle data. As an example, here's the data output from this morning's heat treatment of some AEB-L blades. All it takes to make this graph is to login to a Bartlett IP address for the specific heating event, download the data to an Excel spreadsheet and create a graph.
After years of heat treating on a propane forge and always questioning the HT accuracy, I'm now able to control the HT cycle and create a record of what actually has happened in the process.
Data is recorded every 30 seconds. I've done some detail evaluations of what the deviations are from a given set point and it's really accurate - plus/minus a few degrees. The furnace uses 3 heating elements that minimizes the temperature deviations from front to rear when inserting blades. Data is also collected showing the power levels in amps for each element (not shown here for clarity). You can see a small example of the front to rear heating deviation at the first hold point when I inserted the blades.
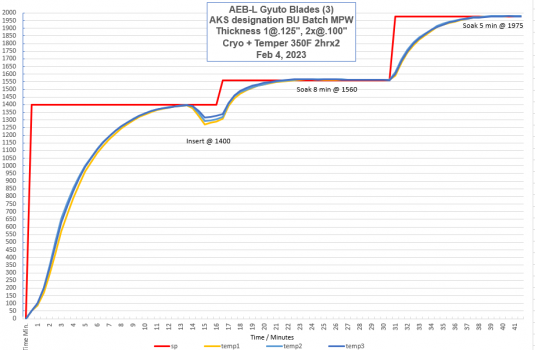
After years of heat treating on a propane forge and always questioning the HT accuracy, I'm now able to control the HT cycle and create a record of what actually has happened in the process.
Data is recorded every 30 seconds. I've done some detail evaluations of what the deviations are from a given set point and it's really accurate - plus/minus a few degrees. The furnace uses 3 heating elements that minimizes the temperature deviations from front to rear when inserting blades. Data is also collected showing the power levels in amps for each element (not shown here for clarity). You can see a small example of the front to rear heating deviation at the first hold point when I inserted the blades.
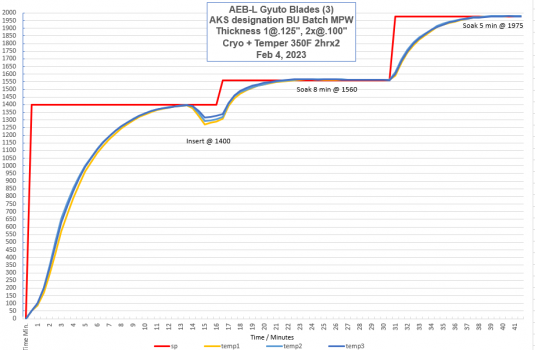