I'll second and third comments about blade speed being critical for metal cutting. Too fast and your blade is toast. How fast is too fast? Depends on a number of things, metal type ie steel vs aluminum vs brass, thickness, feed rate, metal alloy content, tooth rake, etc. I typically run my saw at about 175 SFM, but I vary it a lot depending on the material.
I first began using a bandsaw in the late 50's in my Dad's shop, I now have that same saw in my shop - it's a Delta/Milwaukee 14" with a variable speed drive. In differing years these machines were widely manufactured under various combination of names depending on Delta / Milwaukee / Rockwell ownerships. The old machines like this one are still available at auctions & surplus sales, and are workhorses. This one has had a number of upgrades to improve its performance, including tires, tension spring & guides. The speed control was made by BF Goodrich, it is a constant torque drive using a number of belts driven by a variable pitch pulley. I think any bandsaw can be used for either metal or wood, it's just a matter of matching the blade speed to the material being cut. But, like all machinery, cheaply made equipment can lead to all kinds of problems.
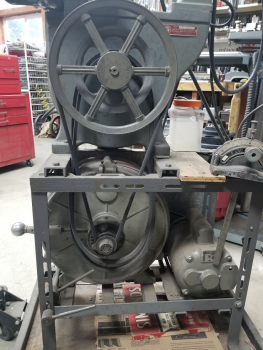
I use this bandsaw a LOT for cutting all kinds of materials, metals, G-10, plastics, wood, nearly anything. To answer one of the questions in this thread, I routinely cut wood with my metal blades. Using a metal blade for wood is not optimal, but I do it all the time. I crank up the speed - but, even then a rip cut it can be slow., crosscutting is easy. Oily woods can tend to burn using a metal blade.
When cutting thick steel, say over 1/4", I'll use a spray mister for coolant & lubricant. My "standard" every day blade is 14 tooth, 3/8", carbon steel. It's a good compromise for getting a fairly tight radius and yet tough enough for most metals and works fine on knife blade stock down to 1/8" or slightly less. I was trying to cut some annealed 80CRV2 .070" stock the other day and found it was going to wreck the blade. Thin material requires higher number of teeth per inch.
Until last year I've been exclusively welding my own blades from 100ft carbon steel coil stock. However, I decided to try some bi-metal blades (Lennox and Starrett) and they are truly a better choice, more expensive but much much tougher than carbon steel. However, I'm cheap, and I get some satisfaction by making my own carbon steel blades from 100 ft coil stock using this antique bandsaw blade welder. I've been told that bi-metal stock cannot be welded easily with this machine.
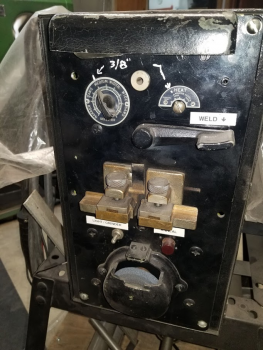
_______________
Bob