opaul
Well-Known Member
Saw this on another forum. Seems like a good deal and I like the idea. I think there have been threads on this.
www.bladeforums.com
Carbide Straightening hammers
Hello Everyone, I’ve gotten some requests recently from friends for carbide hammers like what I use to straighten my blades so I’ve decided to make a few small batches. These start off as a small 7oz hammer that I modify and then pressure fit and glue a 3/8” carbide ball into. The 3/8” carbide...
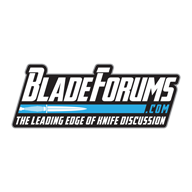