Drew Riley
Well-Known Member
When I first got started in knife making, I built a NWGS out of some steel, mostly procured from a local scrap yard, along with a few other used parts and pieces. The only thing I really splurged on was the wheels. Over the years, I've made a handful of necessary mods to it, and many fine knives with it, but it just wasn't cutting the mustard anymore.... Don't get me wrong, it's still a great grinder, and as good or better than anything I could get for the same money at the time (maybe even still), but I figured it was about time to upgrade.
Now the question became, should I buy a turn key grinder, open the box and go, buy a kit, and build, or design and build something from scratch? Well, after much deliberation, I opened up Fusion 360 and got to work designing something that would have exactly what I wanted in a grinder, or pretty darn close to it. After many hours, revisions, and deletions, I scraped enough of a basic design together to send some aluminum plate over to Mark Vanderwest at Leading Edge to have the basic parts cut.
Basic requirement: Multiple tool arm sockets, versatile/adjustable work rest system, rotates 90, direct drive/variable speed, primarily tool-less for adjustments, etc....
Oh, and for some reason, I was really hung up on using something similar to Mick Strider's over-center cam tensioning system (also seen on John Grimsmo's grinder, and another USN member... grumpy phil I think?)
So here are a few pictures, although it's still a little dirty from my dirty greasy hands running all over it...
Untitled by AR Custom Knives (Andrew Riley), on Flickr
Untitled by AR Custom Knives (Andrew Riley), on Flickr
Untitled by AR Custom Knives (Andrew Riley), on Flickr
Untitled by AR Custom Knives (Andrew Riley), on Flickr
Untitled by AR Custom Knives (Andrew Riley), on Flickr
Initial impressions are very good. I'm loving the "on/off" tension feature (hope Mick doesn't mind that I borrowed his idea), and it's so nice to finally have both a variable speed grinder AND a horizontal option. I still need to mount my 8" contact and small wheel attachment to some tool arms, and the work rest set up will have to be slightly modified for use with those as they stick out from the grinder body a few more inches, and the current work rest arm isn't quite long enough to get in front of them. I've got some ideas though... just gotta get some tool arm materials in.
There's still a small handful of minor tweaks to do, and final proof of concept will be grinding out a few knives on it, but I think I'm gonna really like this thing.
One last thing: It may or may not be obvious, but I drew inspiration from several grinders currently in existence, including, but not limited to: Chris Williams' Wilmont Grinder, Mick Strider's "Sofa King" grinder, Brian Fellhoelter's Ubergrinder, John Grimsmo's grinder, and even perhaps Rob Frink's KMG, to name just a few. Not that I tried to copy or clone anything exactly, but I think I'd be kidding myself and others if I didn't give at least some credit for the inspiration and ideas.
Thanks for looking. I'll eventually try to get some videos up of the grinder in action, and a better video (than what's on my channel) of the work rest system.
Now the question became, should I buy a turn key grinder, open the box and go, buy a kit, and build, or design and build something from scratch? Well, after much deliberation, I opened up Fusion 360 and got to work designing something that would have exactly what I wanted in a grinder, or pretty darn close to it. After many hours, revisions, and deletions, I scraped enough of a basic design together to send some aluminum plate over to Mark Vanderwest at Leading Edge to have the basic parts cut.
Basic requirement: Multiple tool arm sockets, versatile/adjustable work rest system, rotates 90, direct drive/variable speed, primarily tool-less for adjustments, etc....
Oh, and for some reason, I was really hung up on using something similar to Mick Strider's over-center cam tensioning system (also seen on John Grimsmo's grinder, and another USN member... grumpy phil I think?)
So here are a few pictures, although it's still a little dirty from my dirty greasy hands running all over it...
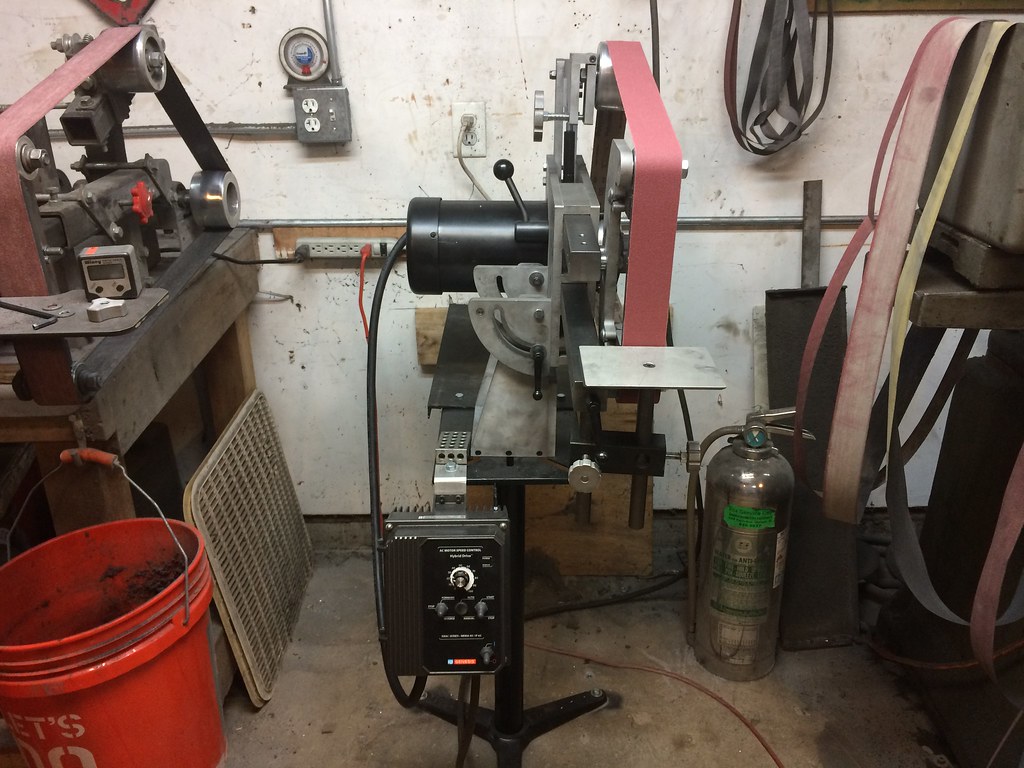
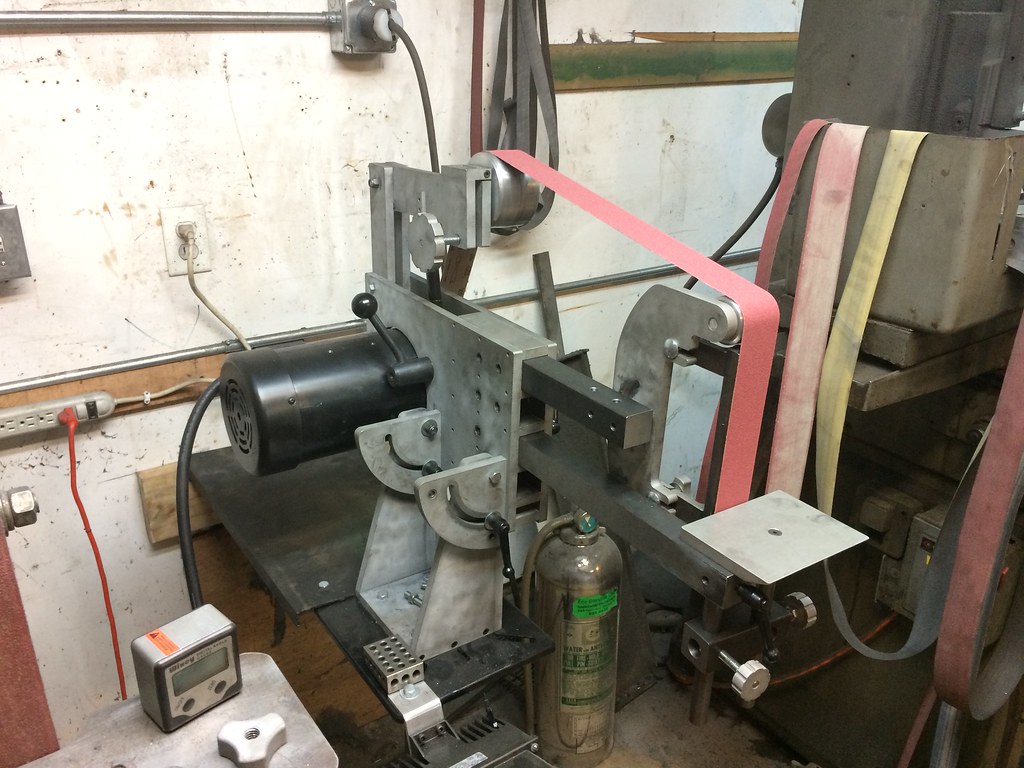
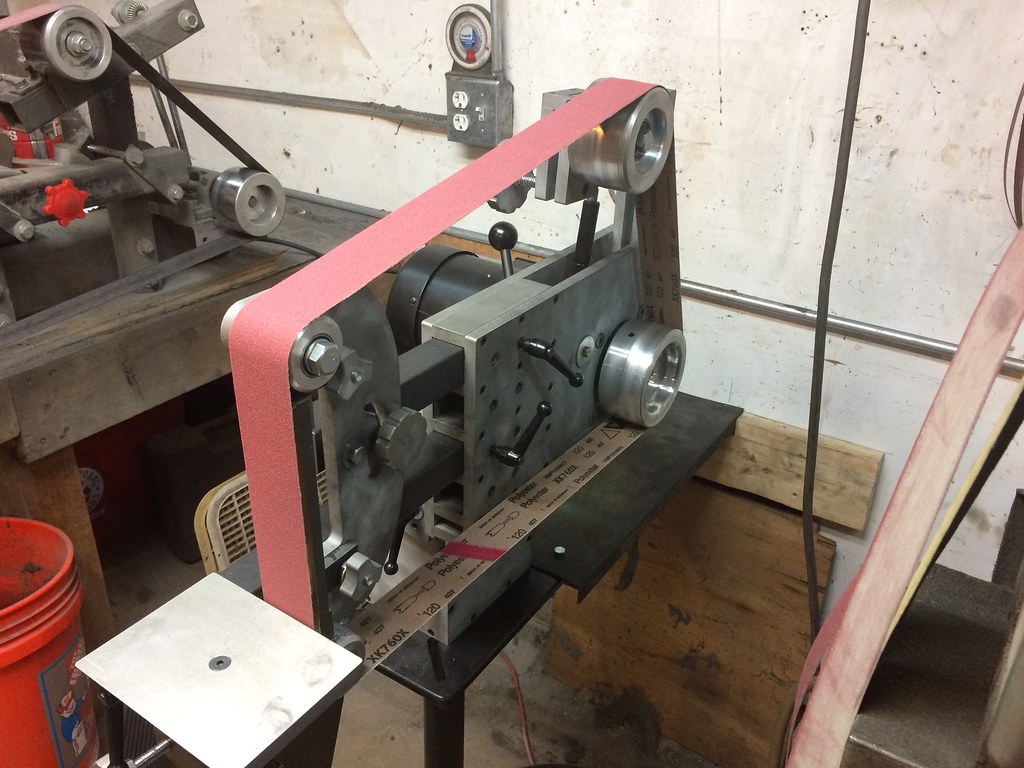
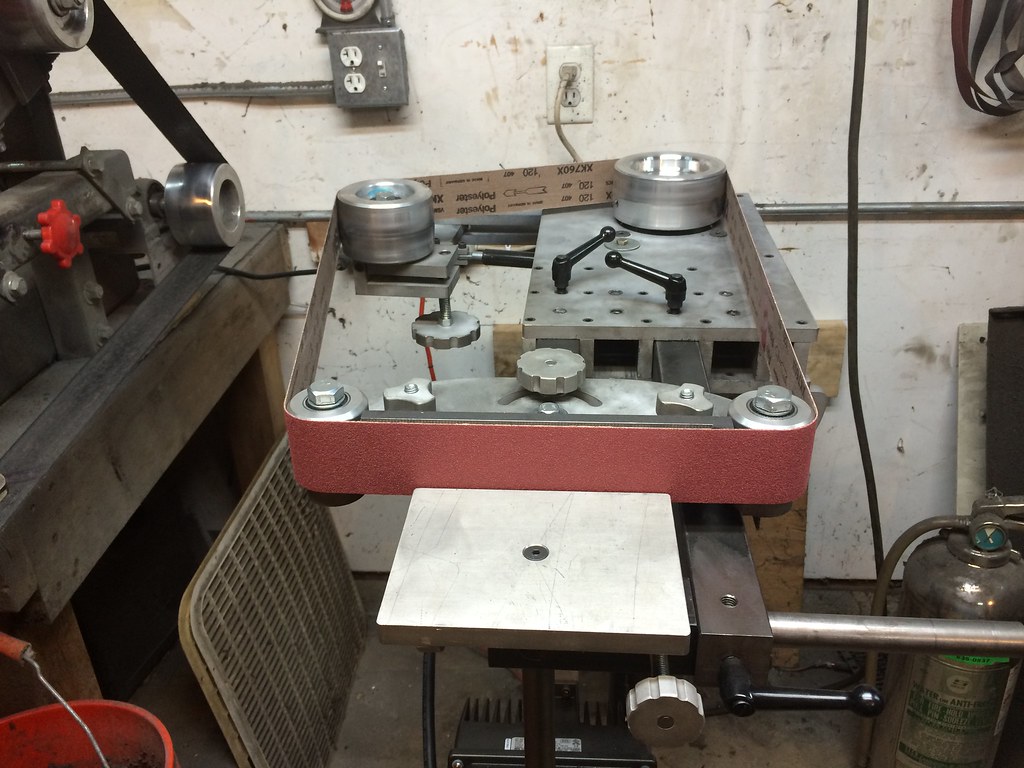
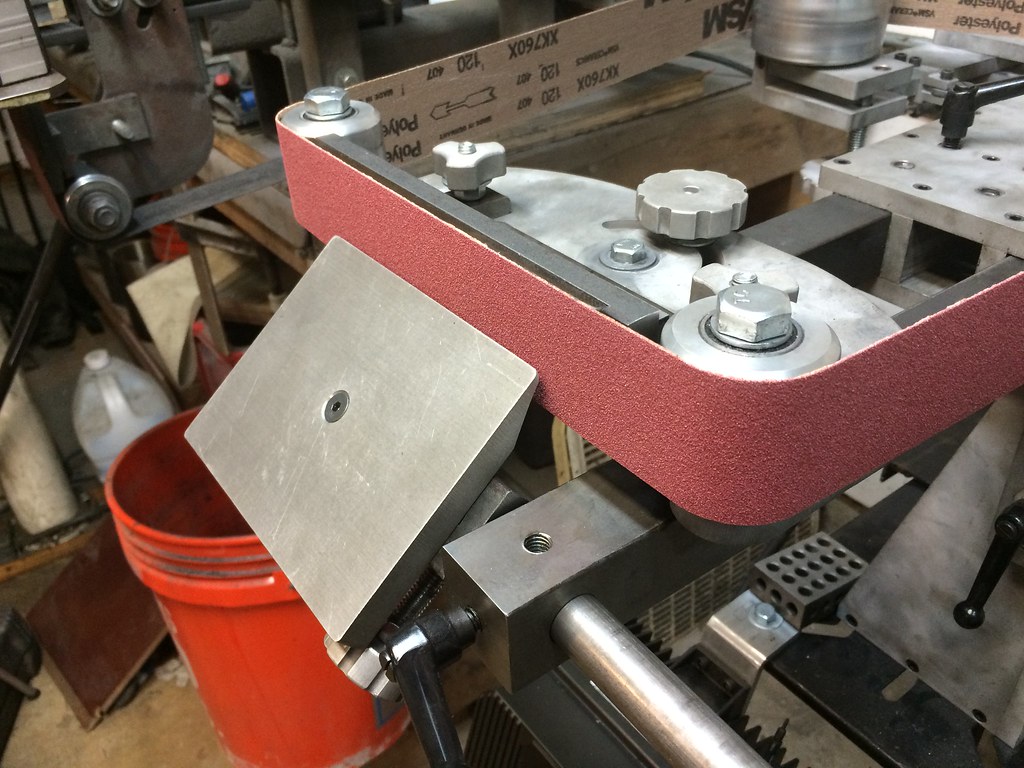
Initial impressions are very good. I'm loving the "on/off" tension feature (hope Mick doesn't mind that I borrowed his idea), and it's so nice to finally have both a variable speed grinder AND a horizontal option. I still need to mount my 8" contact and small wheel attachment to some tool arms, and the work rest set up will have to be slightly modified for use with those as they stick out from the grinder body a few more inches, and the current work rest arm isn't quite long enough to get in front of them. I've got some ideas though... just gotta get some tool arm materials in.
There's still a small handful of minor tweaks to do, and final proof of concept will be grinding out a few knives on it, but I think I'm gonna really like this thing.
One last thing: It may or may not be obvious, but I drew inspiration from several grinders currently in existence, including, but not limited to: Chris Williams' Wilmont Grinder, Mick Strider's "Sofa King" grinder, Brian Fellhoelter's Ubergrinder, John Grimsmo's grinder, and even perhaps Rob Frink's KMG, to name just a few. Not that I tried to copy or clone anything exactly, but I think I'd be kidding myself and others if I didn't give at least some credit for the inspiration and ideas.
Thanks for looking. I'll eventually try to get some videos up of the grinder in action, and a better video (than what's on my channel) of the work rest system.