Time for handles. I'll be using corby bolts for the handles, so I will show my process for installing handles on a regular tang and a tapered tang.
After I have split the block and flattened the scales, I position the blade on the scales where I want it, paying attention to any defects and the grain I want in the handle, and drill one of the pin holes. Then I'll insert a pin in that hole and drill the next.
Next, I tape both scales together and use the holes in the one scale to drill the other.
On a tapered tang, I need to find 1/2 the difference in the thickness of the ricasso end of the handle and the butt end. On this blade, the math was easy. The ricasso is .200" thicker than the butt end of the tang, so I need to shim the butt end of the scale up .100" when I drill the holes.
Three pieces of G-10 liner material will work for the shims.
After the pin holes are drilled, I pin the blade to each scale and draw around the tang. On one of each set of scales, I draw the shape I want for the front of the scales, then rough cut each scale on the band saw, and sand the front of the scale on the disc sander.
I then pin the scale with the profiled front to the other one and cut and sand it to the profiled scale.
Next, I trace the scale profile on to the liner material, cut them out and drill the holes. After ruining a band saw blade cutting the G-10 liners, I found that a pair of tin snips work pretty good to cut the liners out.
After pinning the scales and liners together, I sand the liners flush with the scales.
For the tapered tang, I tape .200" of shims between the front of the scales and liners and .100" of shims under the bottom scale. This squares everything up so the front of the scales will be square with the blade when I sand the fronts.
Now I set up the step drill to drill for the corby bolts. I leave .160" under the shoulder of the corby bolt. This let's me use the same set up on any blade from 1/16" to 3/16" without having to change my set up. I use a shim that I drilled a hole in to set up the stop for drilling with the step drill.
For the tapered tang, I need to shim the front of the scale up .100" to drill for the corby bolts. Since each pin will have to be drilled to a different depth, I set the stop so that the shoulder on the step drill flush with the table. Then I will use different size drill bits set on the stop for each hole.
For the front hole I use a 1/4" drill bit on the stop since the scale is raised up .100" and I want .160" under the shoulder of the corby bolt. I used a .210" bit for the middle pin hole and a .163" for the back hole.
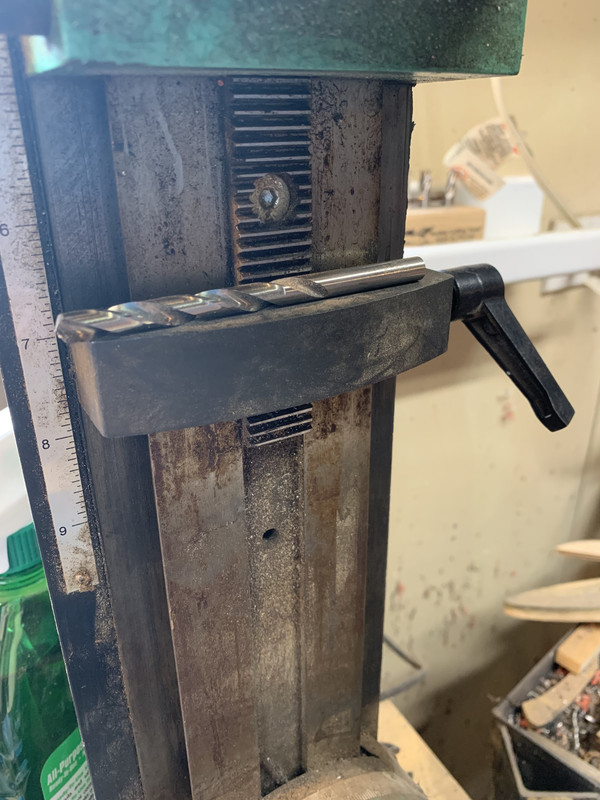