All right guys, picked up my laser cut blanks today! I took a bunch of pics and I'll try to describe them, but I want your feedback on how you think this compares to water jet parts. Overall, I am very happy with them, got 37 blanks cut for $145, or about $3.92 each. I had nested the parts myself and felt that 43 could've been cut, but laser guy said I had them too close and re-nested them. In fact, he told me in the future not to nest them, he just wants an individual part drawing.
So, here's how they came home. They were all rolled up in paper, in bundles of 5 and in a way that there was no metal to metal contact.
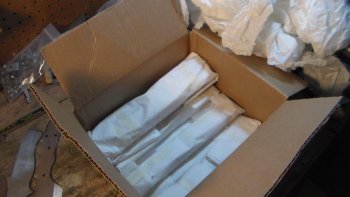
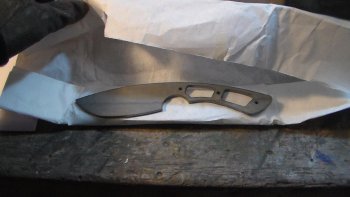
Draft and hole sizes were one of my first concerns, first pic shows a very tiny draft. We're talking 0.005" maybe. Checked holes with drill bits and you can see how tightly they fit. Actually, it almost looks like there is no draft to the holes, at least I couldn't figure out a way to check it.
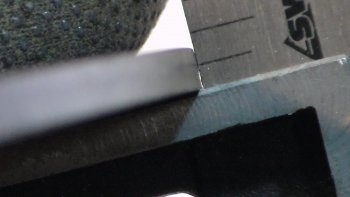
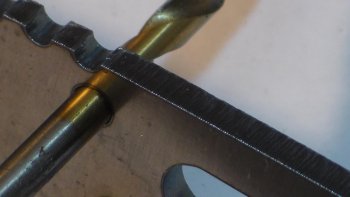
Here's some close ups of the jimping.
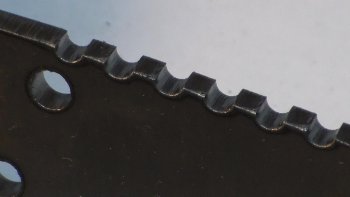
And finally, I tried to show a comparison of the milled blanks I've been making vs. the laser to show a cut quality comparison. The blank in front is laser, behind that is one I just roughed on the mill. Pretty close to the same.
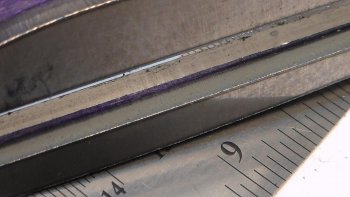
I have timed every step of profiling, milling, drilling, and filing jimping on my survival knife and I always average over an hour each. I think a conservative estimate on the time the laser is saving me for this batch is at least 40 hrs. of work. Not to mention drill bits, end mills, and my sore elbows. I think I can debur and clean these up in about 5 minutes each.