JPSWorks
Well-Known Member
(UPDATE SUCCESS!)..Unable to solder stainless steel bolsters
Hello everyone. I was hoping to get some soldering guidance from those with more knowledge and experience than I do.
I am working on a slipjoint and was attempting to solder on the bolsters because I don't currently have a spot welder. A while back I was able to successfully solder brass bolsters to brass liners. I had read and watched many tutorials that made it go much easier than I thought it would. Today was the complete opposite. The difference is that this is the first time I have tried to join stainless to stainless.
I used 410 ss for both the liner and bolster.
Sanded them completely flat by hand on sandpaper over thick glass.
Roughed the areas to be soldered together.
Used nitrile gloves and cleaned everything thoroughly with acetone.
Wiped it down and clean it again letting it air dry.
Applied the paste flux to all the each piece the laid a coil of solder on.
I attempted to tin each piece by heating it over the torch, moving it in and out of the flame. When it began to melt I tried to spread it around with a steel rod but it just wanted to pool in the center. Even using the rod I couldn't spread it out over the whole are. When I was tinning the brass each bit of solder would melt and flow evenly out to all sides. I could then use the rod to spread it around if I missed spot then knock the rest off. It left and nice thin shiny tinned layer on each piece. This just looked like a round blob in the middle, and a brownish barrier around the solder.
I am obviously burning the flux before the solder has time to melt even though I tried to heat it slowly. No matter what I tried it kept burning. For those that have done this many times, can you tell me what I am doing wrong? Am I applying too much flux, or am I even using the correct type of solder and flux for the job? The flux is this weird white cream that came with a brush to paste it on. Not liquid like I have seen in some how-tos.
Hopefully the pics below with show more what I am referring to. I appreciate any and all help with this.
Thanks again,
John
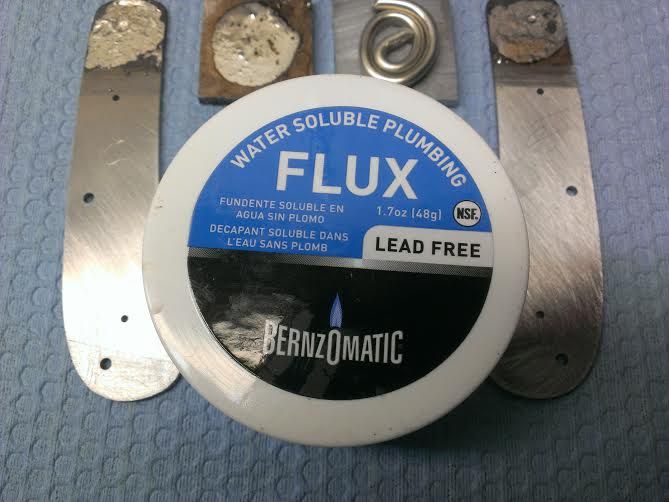
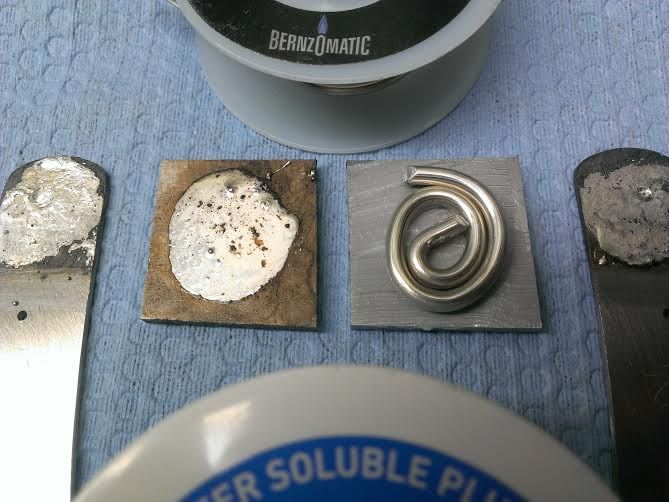
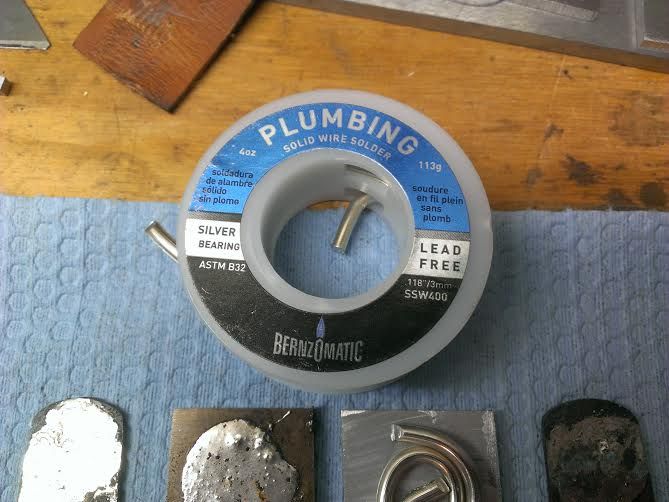
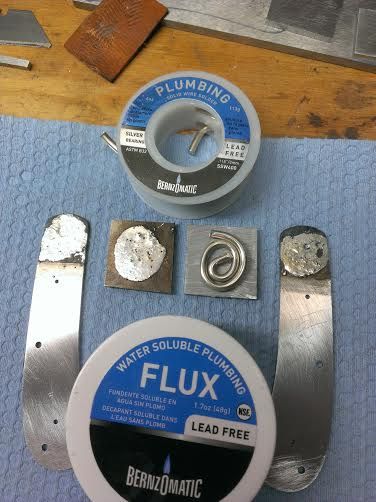
Hello everyone. I was hoping to get some soldering guidance from those with more knowledge and experience than I do.
I am working on a slipjoint and was attempting to solder on the bolsters because I don't currently have a spot welder. A while back I was able to successfully solder brass bolsters to brass liners. I had read and watched many tutorials that made it go much easier than I thought it would. Today was the complete opposite. The difference is that this is the first time I have tried to join stainless to stainless.
I used 410 ss for both the liner and bolster.
Sanded them completely flat by hand on sandpaper over thick glass.
Roughed the areas to be soldered together.
Used nitrile gloves and cleaned everything thoroughly with acetone.
Wiped it down and clean it again letting it air dry.
Applied the paste flux to all the each piece the laid a coil of solder on.
I attempted to tin each piece by heating it over the torch, moving it in and out of the flame. When it began to melt I tried to spread it around with a steel rod but it just wanted to pool in the center. Even using the rod I couldn't spread it out over the whole are. When I was tinning the brass each bit of solder would melt and flow evenly out to all sides. I could then use the rod to spread it around if I missed spot then knock the rest off. It left and nice thin shiny tinned layer on each piece. This just looked like a round blob in the middle, and a brownish barrier around the solder.
I am obviously burning the flux before the solder has time to melt even though I tried to heat it slowly. No matter what I tried it kept burning. For those that have done this many times, can you tell me what I am doing wrong? Am I applying too much flux, or am I even using the correct type of solder and flux for the job? The flux is this weird white cream that came with a brush to paste it on. Not liquid like I have seen in some how-tos.
Hopefully the pics below with show more what I am referring to. I appreciate any and all help with this.
Thanks again,
John
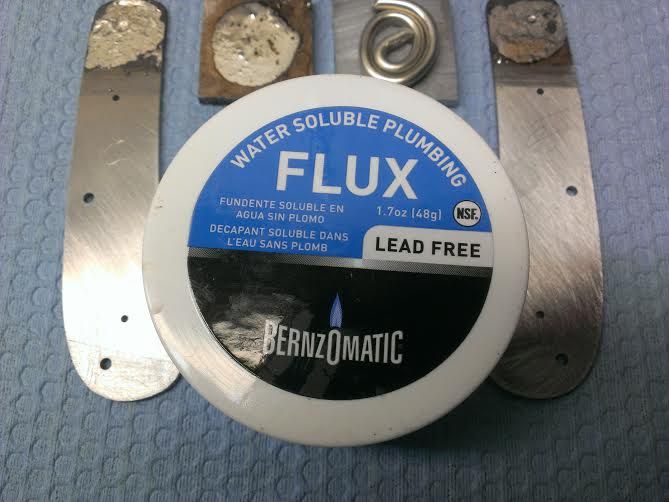
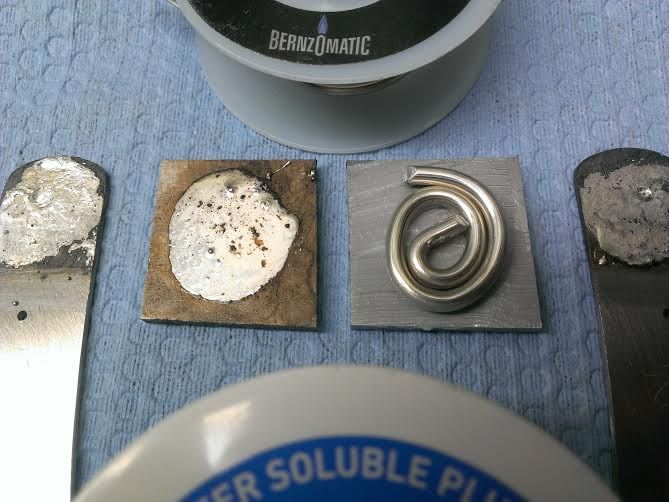
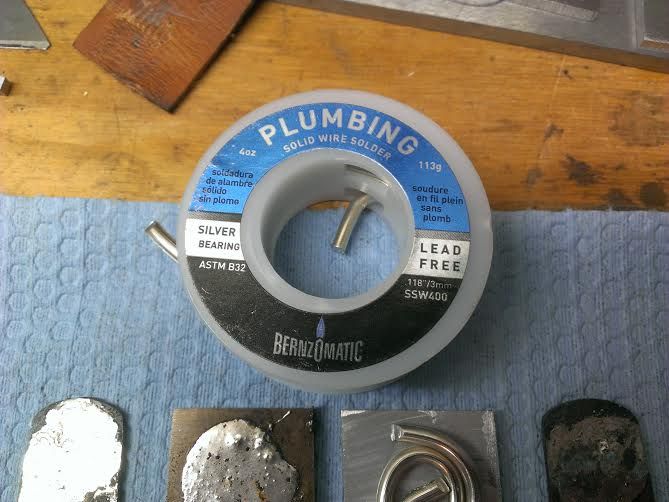
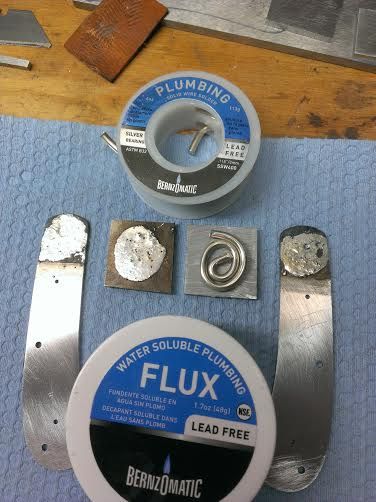
Last edited: