The wheels have been bolted on using 1/2" bolts and washers and machinery bushings.
Machinery bushings are just washers with a special shape. These go next to the wheel bearings. The ID fits the 1/2" bolt and the OD is not larger than the bearings pressed into the pockets on the wheels. This means the bushing will not rub on the wheel but the pressure is on the outer rim of the bearing.
Stack 2 of these on either side of the wheel bearing and then add enough washers to line the wheels up
The swivel block side with 2 machinery bushings stacked up.
The motor side with 2 machinery bushings and a fender washer.
When you are lining up the wheels, start with the 4 wheel set up first.
Stack washers on the contact wheels first, then the tracking wheel and finally move the drive wheel in and out on the motor drive shaft to get them lined up. After that, pop in your single contact wheel and stack washers accordingly.
Careful how tight this is. You want the bolt just tight enough to not wobble but any tighter and bind things up. The wheel should spin freely by hand or you have it too tight. We will ship these with locking nuts. I just used regular nuts shown here during prototyping.
Your platen will absolutely require some tweaks to get perfectly lined up. We bend these by hand in a 20 air over hydraulic press brake and they will each be slightly different. Use a hammer to tap these to the shape and bend you need.
Here the tracking wheel shows it needs some additional washers. Keep in mind that occasionally, you will track your belt off the wheels slightly and this might be just right.
The tracking wheel swivels on a 1/4"x3" bolt. Use a washer between the brackets and block.
This is the tracking adjustment block. You can see the 1/4" through hole that is the pivot. You can also see the threaded 1/2"-13 (coarse) hole to hold the tracking wheel. The sharpie circle mark shows where the adjustment screw pushes against the block to swivel the assembly in or out.
Note the top and bottom of the swivel bloc is slightly rounded. We do that to give some additional swivel room. If you still need more swivel room, grind away on the XXX's to allow the block to swivel just a bit further.
While this looks mickey mouse, it works well and it's cheap. Keep that in mind. This is a budget grinder.
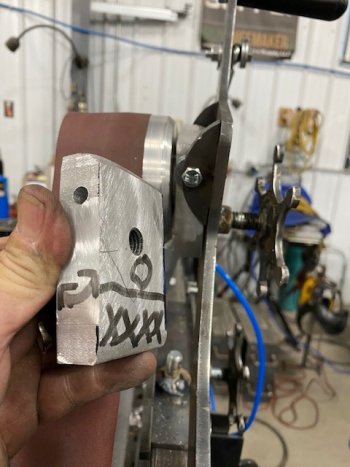