How the "Unigrinder" concept was developed...
There is one old belt grinder in my woodworking shop, it uses 2.5” x 48” grinding belts and has a ½ hp motor which interferes with grinding on the left side of the contact wheel. Bought it about 20 years ago and have used it for many, many things in my woodworking shop besides knife making.
Got back into knife grinding, after about a 15 year sabbatical. Decided it was time to step up to full size belts, minimum of 1 ½ HP with speed and direction control, blade/tool rest that is solid and will actually work, real good belt alignment, low noise, smooth, etc. Looked seriously into my finances and realized it would have to be a low-budget affair using the equipment and materials that already have in my woodworking and turning shop.
Since I am really a beginner knife maker (meaning a small number of knives have been butchered over a long period of time), was not really sure what would work good or what was really needed in a grinder so the market was researched pretty well. Looked at the equipment and materials in my shop, took some measurements, thought about it a lot, and did some 3-D modeling. Based upon this, the following grinder evolved by trying to get back to the basics and keeping to simple solutions.
One of the tools available in my woodworking shop is a Powermatic 3520B wood turning lathe, a heavy duty wood turning lathe with a 1 ½ hp variable speed drive that can turn a 20 inch diameter disk over the ways. It would be a very easy to modify and a near perfect drive for the belt grinder.
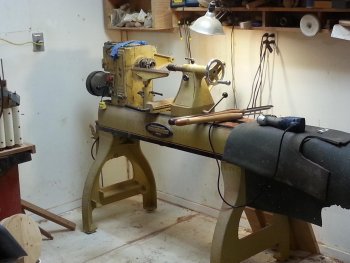
Picture 1 above showing the Powermatic 3520B lathe in the corner of my shop.
Existing belt grinders have a number of different wheels; drive wheels, alignment wheels, large radius contact wheels, small radius contact wheels, flat plenums, etc. Rethinking and simplifying the belt grinder’s purpose, it was decided to go with one wheel that would expand slightly to grip the grinding belt. What could be simpler – one wheel, and a big one at that? :les:
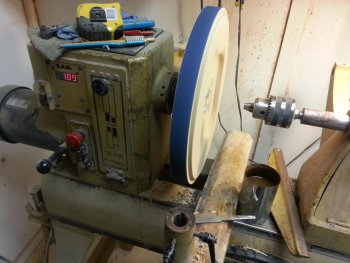
Picture 2 above showing, at a slow grinding speed, the “Unigrinder” prototype for half of a 2 ½” x 48” grinding belt.
The only grinding belts in my shop are 2.5” x 48”, and the same evening that I started designing this grinder, an article was read that stated one guy who like to rip his grinding belts in half so that he had 4 edges to work with on a belt instead of just 2. It made sense, :what!: so the prototype was built for a 1.25” wide x 48” long grinding belt with the 90° quadrants built out of ¾” MDF and sized to fit my largest wood turning scroll chuck. Had to buy ¾”MDF and metric bolts to match the chuck, total cost was less than $20.
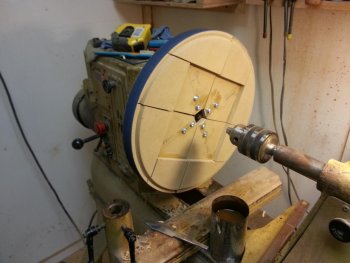
Picture 3 showing the semi-finished belt grinder prototype, without the tool/knife rest.
Above is a picture of the prototype in my shop, with the first test knife blade being ground with a 60 grit belts. The prototype has about a 15.24” diameter grinding wheel and will expand the 1/16” in diameter to grip the 48” long grinding belts used here. The quadrant segments were glued up ¾” MDF, trimmed slightly and drilled to fit the wood scroll chuck mounting holes. Once mounted, the lathe was turned on and the outside diameter turned true and the outside surface flattened with a 5” orbital sander. The quadrant width was turned to be slightly larger than the belt width. Belts used are the 60 and 120 grit blue Norton cloth backed belts. The rigidity of the backing made the slight wheel circumference gaps disappear.
Happy to say, the “Unigrinder” grinds good to me and hope some other people will try out the concept. Will post the updated concept for 2” x 72” belts over the next few days that can be easily made in a simple woodworking shop and total expected cost is about $300 for the 1.5 ho motor/driver combination and one sheet of ¾” MDF.
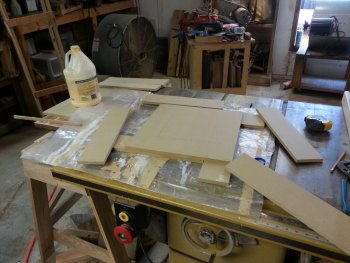
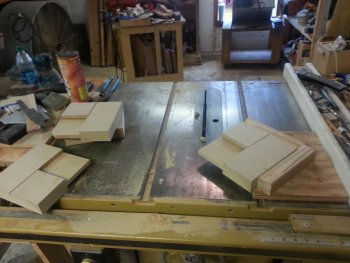

Pictures 4,5, & 6 show the wheel construction.
Next step is prototype for 2"x 72" belts that can be built in anybodys' woodworking shop for basically the cost of the motor and controller.
Hint, hint…if one has the motor and speed controller for it, then the woodworking lathe is not needed. The scroll chuck principles are simple…….you got it.
Will continue in several days when time permits.
Thank you guys and gals, here and in the other knife making forums and organizations. You have given me plenty of help and inspiration in the past, and this seems a simple way to try making up for some of it.
Rich S.
There is one old belt grinder in my woodworking shop, it uses 2.5” x 48” grinding belts and has a ½ hp motor which interferes with grinding on the left side of the contact wheel. Bought it about 20 years ago and have used it for many, many things in my woodworking shop besides knife making.
Got back into knife grinding, after about a 15 year sabbatical. Decided it was time to step up to full size belts, minimum of 1 ½ HP with speed and direction control, blade/tool rest that is solid and will actually work, real good belt alignment, low noise, smooth, etc. Looked seriously into my finances and realized it would have to be a low-budget affair using the equipment and materials that already have in my woodworking and turning shop.
Since I am really a beginner knife maker (meaning a small number of knives have been butchered over a long period of time), was not really sure what would work good or what was really needed in a grinder so the market was researched pretty well. Looked at the equipment and materials in my shop, took some measurements, thought about it a lot, and did some 3-D modeling. Based upon this, the following grinder evolved by trying to get back to the basics and keeping to simple solutions.
One of the tools available in my woodworking shop is a Powermatic 3520B wood turning lathe, a heavy duty wood turning lathe with a 1 ½ hp variable speed drive that can turn a 20 inch diameter disk over the ways. It would be a very easy to modify and a near perfect drive for the belt grinder.
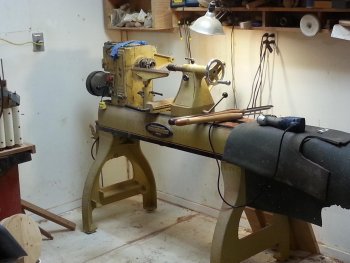
Picture 1 above showing the Powermatic 3520B lathe in the corner of my shop.
Existing belt grinders have a number of different wheels; drive wheels, alignment wheels, large radius contact wheels, small radius contact wheels, flat plenums, etc. Rethinking and simplifying the belt grinder’s purpose, it was decided to go with one wheel that would expand slightly to grip the grinding belt. What could be simpler – one wheel, and a big one at that? :les:
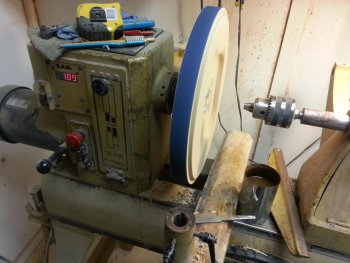
Picture 2 above showing, at a slow grinding speed, the “Unigrinder” prototype for half of a 2 ½” x 48” grinding belt.
The only grinding belts in my shop are 2.5” x 48”, and the same evening that I started designing this grinder, an article was read that stated one guy who like to rip his grinding belts in half so that he had 4 edges to work with on a belt instead of just 2. It made sense, :what!: so the prototype was built for a 1.25” wide x 48” long grinding belt with the 90° quadrants built out of ¾” MDF and sized to fit my largest wood turning scroll chuck. Had to buy ¾”MDF and metric bolts to match the chuck, total cost was less than $20.
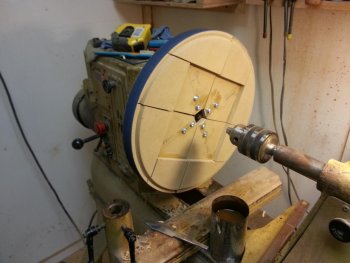
Picture 3 showing the semi-finished belt grinder prototype, without the tool/knife rest.
Above is a picture of the prototype in my shop, with the first test knife blade being ground with a 60 grit belts. The prototype has about a 15.24” diameter grinding wheel and will expand the 1/16” in diameter to grip the 48” long grinding belts used here. The quadrant segments were glued up ¾” MDF, trimmed slightly and drilled to fit the wood scroll chuck mounting holes. Once mounted, the lathe was turned on and the outside diameter turned true and the outside surface flattened with a 5” orbital sander. The quadrant width was turned to be slightly larger than the belt width. Belts used are the 60 and 120 grit blue Norton cloth backed belts. The rigidity of the backing made the slight wheel circumference gaps disappear.
Happy to say, the “Unigrinder” grinds good to me and hope some other people will try out the concept. Will post the updated concept for 2” x 72” belts over the next few days that can be easily made in a simple woodworking shop and total expected cost is about $300 for the 1.5 ho motor/driver combination and one sheet of ¾” MDF.
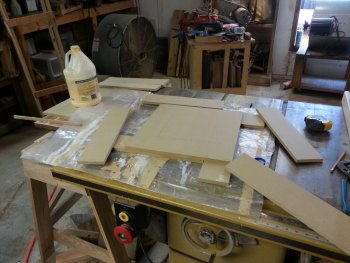
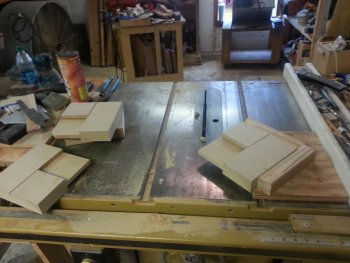

Pictures 4,5, & 6 show the wheel construction.
Next step is prototype for 2"x 72" belts that can be built in anybodys' woodworking shop for basically the cost of the motor and controller.
Hint, hint…if one has the motor and speed controller for it, then the woodworking lathe is not needed. The scroll chuck principles are simple…….you got it.
Will continue in several days when time permits.
Thank you guys and gals, here and in the other knife making forums and organizations. You have given me plenty of help and inspiration in the past, and this seems a simple way to try making up for some of it.
Rich S.