MTBob
Well-Known Member
If you're like me, too many times I've gotten lazy using my drill press and find my work piece Helicoptering. For those who haven't experienced the Helicopter, it can occur when drilling a long thin work piece (say ... a knife blank). If too much pressure is applied as the drill leaves the bottom of the hole, the bit digs in and wham-o, you've got an unbalanced rotating finger slicer ripping into your bones. This problem arises usually when the drill RPM is too high, feed rate (downward pressure) is too high, or drill bit is dull. Here are several ways to stop the Helicoptering.
Use a clamp as a blocking device. Position the clamp within the spin radius of the work piece so it will keep it from spinning if the drill binds up. I usually don't use this kind of clamp to hold work pieces onto the table, it's just serves as a block to stop Helicoptering. The clamp can be limited in use since it often can't be positioned where you want it due to webs under the table. The clamp shown here is a quick release Hanson adjustable clamp. C clamps will work, but much to fiddly for me.
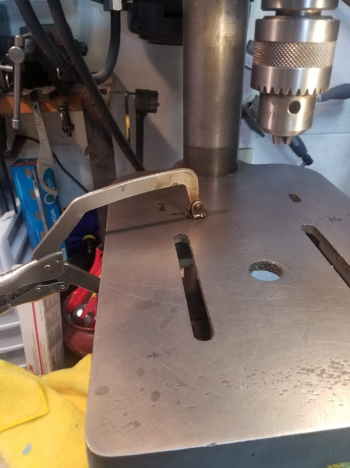
Here's a little fixture I made the other day that takes the place of a clamp and works really well. Simple to make and does the job. I cut off a chunk of aluminum stock and drilled / threaded a hole for a bolt located in a table slot. This fixture also could easily be made with a bolt and stack of washers, nothing fancy, just something that keeps the work piece from spinning.
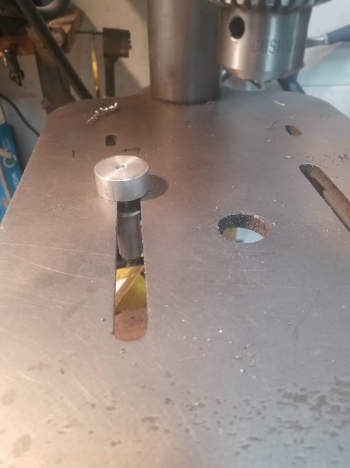
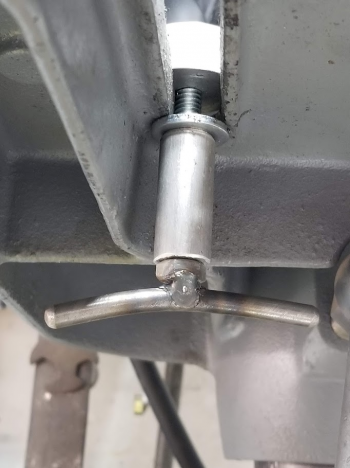
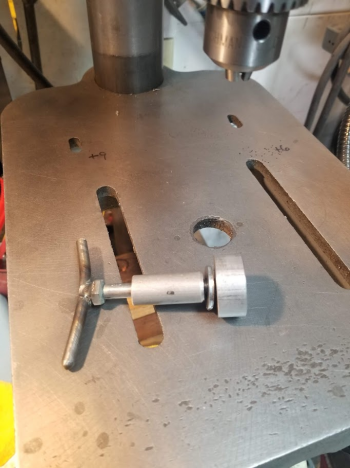
One disadvantage of this simple block (or above clamp) is that they won't do much to keep the work piece from cork screwing up the drill bit flute, a nasty variation of the classic "Helicopter". If that happens the work piece can ride up over the block and still helicopter, that's when it gets real exciting. The best method, of course, is to clamp the piece to the table solidly for each hole being drilled. I'm often too lazy to do that, so I've learned to be mindful of how much pressure I apply when the drill begins to exit the work piece and push down on the work piece with my hand. I am also careful to adjust my drill press RPM to match the size of drill - small drill higher RPM / larger drill slower RPM. It's also worth mentioning that I always place my hands in a position to move them quickly out of the potential spin radius. A dab of cutting oil also reduces binding.
I also use a seriously solid offset clamp for those times when the drill sizes get too big (say >3/8"). Using an offset clamp is a fast way of readjusting work pieces on the drill press table and achieving solid hold down pressure. I modified the clamp shown here so it bolts to the table and has a heavy flexible hold down foot. It works well for larger pieces, but it's somewhat bulky and not too convenient.
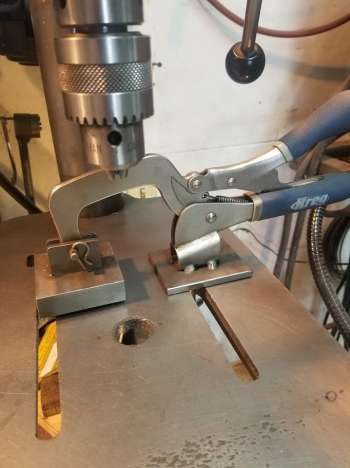
I NEVER drill any long flat work piece without one of these methods in place. "Chunks" of stuff can be held in a vice.
Use a clamp as a blocking device. Position the clamp within the spin radius of the work piece so it will keep it from spinning if the drill binds up. I usually don't use this kind of clamp to hold work pieces onto the table, it's just serves as a block to stop Helicoptering. The clamp can be limited in use since it often can't be positioned where you want it due to webs under the table. The clamp shown here is a quick release Hanson adjustable clamp. C clamps will work, but much to fiddly for me.
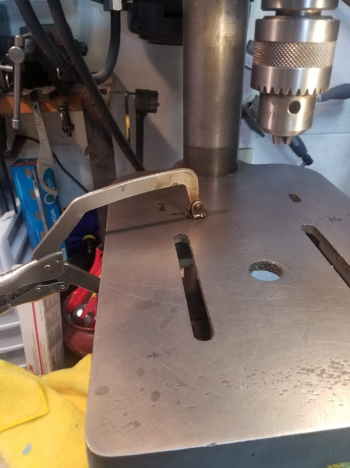
Here's a little fixture I made the other day that takes the place of a clamp and works really well. Simple to make and does the job. I cut off a chunk of aluminum stock and drilled / threaded a hole for a bolt located in a table slot. This fixture also could easily be made with a bolt and stack of washers, nothing fancy, just something that keeps the work piece from spinning.
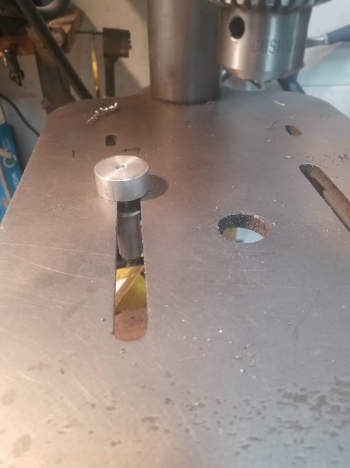
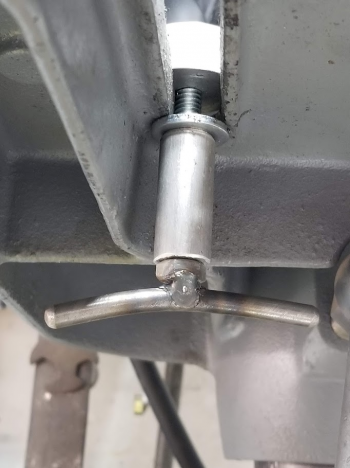
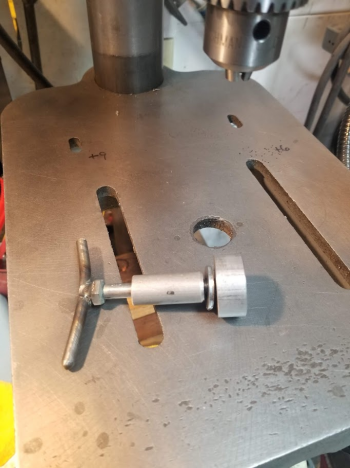
One disadvantage of this simple block (or above clamp) is that they won't do much to keep the work piece from cork screwing up the drill bit flute, a nasty variation of the classic "Helicopter". If that happens the work piece can ride up over the block and still helicopter, that's when it gets real exciting. The best method, of course, is to clamp the piece to the table solidly for each hole being drilled. I'm often too lazy to do that, so I've learned to be mindful of how much pressure I apply when the drill begins to exit the work piece and push down on the work piece with my hand. I am also careful to adjust my drill press RPM to match the size of drill - small drill higher RPM / larger drill slower RPM. It's also worth mentioning that I always place my hands in a position to move them quickly out of the potential spin radius. A dab of cutting oil also reduces binding.
I also use a seriously solid offset clamp for those times when the drill sizes get too big (say >3/8"). Using an offset clamp is a fast way of readjusting work pieces on the drill press table and achieving solid hold down pressure. I modified the clamp shown here so it bolts to the table and has a heavy flexible hold down foot. It works well for larger pieces, but it's somewhat bulky and not too convenient.
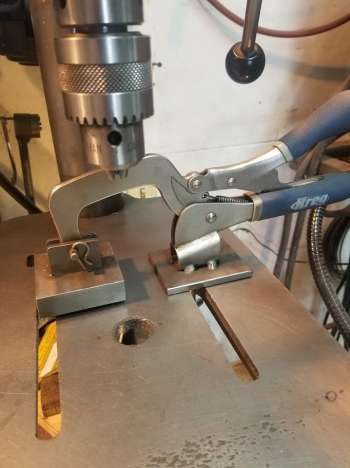
I NEVER drill any long flat work piece without one of these methods in place. "Chunks" of stuff can be held in a vice.