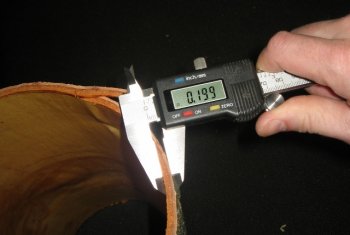
I just collected some birch bark from live trees that were about to be logged.
Guess it was the right time of the year because both the inner and outer bark easily popped right off.
Most of the stuff I read only mentions to use the outer bark...no mention of the inner bark.
Because of the thickness, I'm really tempted to use them both.
Anyone here have any experience with this?