I have finally finished up the small batch run. Overall I am happy with how these turned out. This was the first time I have made a small batch like this, can't say I'll do it again anytime soon! Also the first time working with a stainless steel, probably will do more in the future, once I have the ability to heat treat them myself (need LN). There are 3 things I am not 100% thrilled with though.
1) 3 of the 7 blades were so badly warped that they couldn't be salvaged (by me). I set them aside and may try again in the future, but for now I just remade the blades using O1 tool steel. So I only ended up with 4 MagnaCut blades.
2) I should have waited to finish the blades until after the logo was laser etched. They needed to be sanded after the logo and then finished in the acid and stonewashing. However, I had already used Loc-Tite on the hardware when I assembled the knives prior to logo etching. Plus, most of these are zero grind or close to it before I put the 18 degree bevels on. I was afraid that if I stonewashed these again in my tumbler with the ceramic media, the edges may chip out, I didn't want to risk that. Plus I like the worn in, well used look, and the logos def have that look! So I'm not too upset.
3) There is some centering issue with a couple of the blades. Nothing horrible, but my OCD is def going crazy! The blades are flat (checked on granite surface plate) as well as the scales (check with granite surface plate). There aren't any burrs around the pivot (as far as I could tell), so the only thing I can think is my counterbore that I use for the bearing pocket must be nearing the end of it's life or something like that. I'll scrap it and get a new one. Been thinking of different ways to do this anyway, maybe using a smaller end mill and my rotary table to mill the bearing pocket instead.
But, again, I like how they look. I am a big fan of worn in/well used looking things. They will make excellent EDC blades. They def aren't show pieces, they are made to be used. As such, they will be priced accordingly if anyone is interested in purchasing one.
Thanks for following along and the nice comments as well. Hopefully it helped someone with some aspect of making a framelock!!
Take care and grind on!!
Here are the first 4 (only #2 is MagnaCut out of this group)
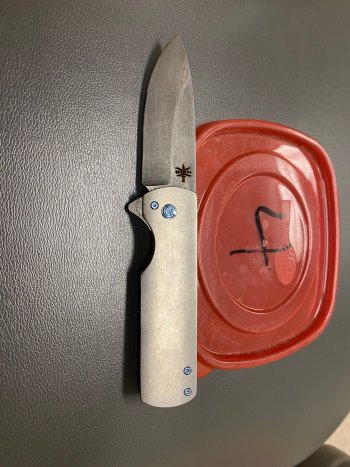