Stang Bladeworks
KNIFE MAKER
Hi Guys,
I just got a mill and I have been looking for any excuse to use it. I decided to use a 1/16 end mill to mill long pulls in my slipjoints. Due to my process I need to mill this after hardening. I run my cpm154 at 62HRC so it is a bit of a challenge. I bought a carbide end mill on amazon for this task. I got one done but my endmill snapped. I am wondering if anyone has any tips or tricks for an operation like this. I am hoping to get more than one knife per endmill. For this time I ran about 2500rpm with .005" depth of cut. Is there a specific type of end mill that would excel at this? can I reasonably get multiple knives out of one endmill? should I adjust my parameters? For this one I used rapid tap but I imagine I should use some coolant or at least air to help. The chips started to pile up badly. These small endmills snap like toothpicks and they are not cheap. I am open to any suggestions, I have no machining experience so I have a lot to learn / spend...
Thanks.
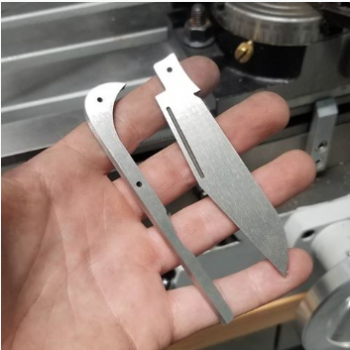
I just got a mill and I have been looking for any excuse to use it. I decided to use a 1/16 end mill to mill long pulls in my slipjoints. Due to my process I need to mill this after hardening. I run my cpm154 at 62HRC so it is a bit of a challenge. I bought a carbide end mill on amazon for this task. I got one done but my endmill snapped. I am wondering if anyone has any tips or tricks for an operation like this. I am hoping to get more than one knife per endmill. For this time I ran about 2500rpm with .005" depth of cut. Is there a specific type of end mill that would excel at this? can I reasonably get multiple knives out of one endmill? should I adjust my parameters? For this one I used rapid tap but I imagine I should use some coolant or at least air to help. The chips started to pile up badly. These small endmills snap like toothpicks and they are not cheap. I am open to any suggestions, I have no machining experience so I have a lot to learn / spend...
Thanks.
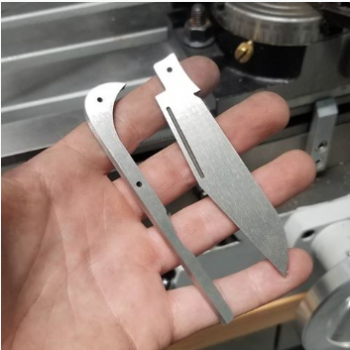