J S Machine
Well-Known Member
I have been nonstop building a completely new shop since around May of last year. Since my family and I moved to our new home, I finally got the chance to build a dedicated knife shop. I was able to section of an area of the shop and make it a grinding room, and then utilize the rest of the floor space for other things. I have been slowly trying to make the transition from doing things at work to being completely self sufficient at home. I am a tool maker for a living, so I have heat treat ovens and surface grinders at work - those two things being the last of the machines I need to make the 100% transition to making at home.
Anyway, the tormach I acquired last year is in place and up and moving at last. I have been slowly working the bugs out of a new design. The goal with this machine is to make at least a couple of different designs of knives, where just about everything but the blade grinding and final finishing can be done. That would be approximately 85% of each knife I guess.
I'm really trying to work towards being able to actually take orders and sell knives, and that is something I have never done. Since I have been doing this - around 2007 - I have only sold two knives. I'm past the point of doing it for fun and I really enjoy doing them for charity (around ten of those so far), but I've got to start getting some return on my efforts. I'm hoping the tormach will enable this.
This is the first design I have actively worked on in the machine. It is called the "Maelstrom". I am working on the third prototype now, and I hope to have it ironed out within a month or so. I have made two sets of handle frames so far, this being the second set. The current blade in it in these pictures is just some cold rolled sheet stock where I am trying to perfect the blade shape. The handle shape is pretty much final, but I'm still working on redesigning the pocket clip. It needs to be further towards the handle end, and it will most likely utilize one of the standoff screws to hold it, which will eliminate the third screw it is being held by at the moment. I'm also going to try to make it universal, where it can be mounted tip up or tip down.
Materials are Ti for the handle frames and clip, and whatever blade steel is popular for the blade. The current stuff I have on hand is CTS XHP. Blade thickness is not correct at the moment. It will be around 5/32". When the design is perfected, then I can work on variations such as inlays and whatever else to make each one unique. I can't wait to get to that part.
A goal that I had set was to be up running and producing in the next few months, where I could at last be a vendor at Blade show in Atlanta. I've never been a vendor before or had any type of table at any show, so I am not sure I will get there, but that's the goal.
Please let me know your thoughts on the design. since it is still in the design phase, any changes are easy to make right now. I'd really like to have input.
:5:
Anyway, the tormach I acquired last year is in place and up and moving at last. I have been slowly working the bugs out of a new design. The goal with this machine is to make at least a couple of different designs of knives, where just about everything but the blade grinding and final finishing can be done. That would be approximately 85% of each knife I guess.
I'm really trying to work towards being able to actually take orders and sell knives, and that is something I have never done. Since I have been doing this - around 2007 - I have only sold two knives. I'm past the point of doing it for fun and I really enjoy doing them for charity (around ten of those so far), but I've got to start getting some return on my efforts. I'm hoping the tormach will enable this.
This is the first design I have actively worked on in the machine. It is called the "Maelstrom". I am working on the third prototype now, and I hope to have it ironed out within a month or so. I have made two sets of handle frames so far, this being the second set. The current blade in it in these pictures is just some cold rolled sheet stock where I am trying to perfect the blade shape. The handle shape is pretty much final, but I'm still working on redesigning the pocket clip. It needs to be further towards the handle end, and it will most likely utilize one of the standoff screws to hold it, which will eliminate the third screw it is being held by at the moment. I'm also going to try to make it universal, where it can be mounted tip up or tip down.
Materials are Ti for the handle frames and clip, and whatever blade steel is popular for the blade. The current stuff I have on hand is CTS XHP. Blade thickness is not correct at the moment. It will be around 5/32". When the design is perfected, then I can work on variations such as inlays and whatever else to make each one unique. I can't wait to get to that part.
A goal that I had set was to be up running and producing in the next few months, where I could at last be a vendor at Blade show in Atlanta. I've never been a vendor before or had any type of table at any show, so I am not sure I will get there, but that's the goal.
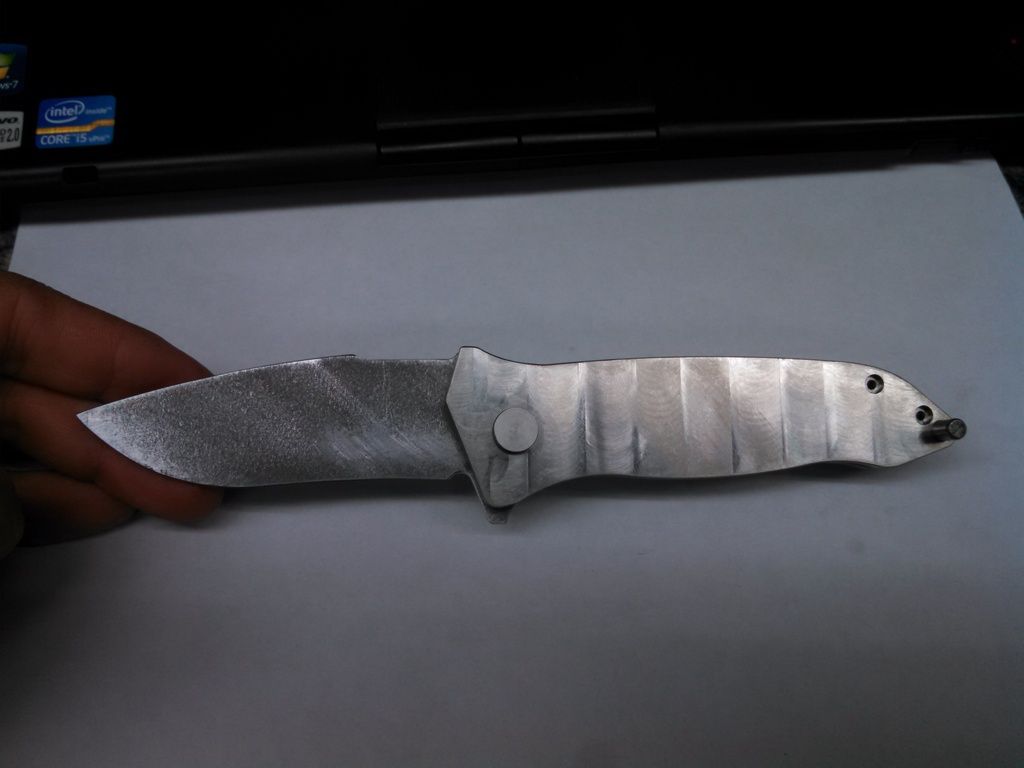
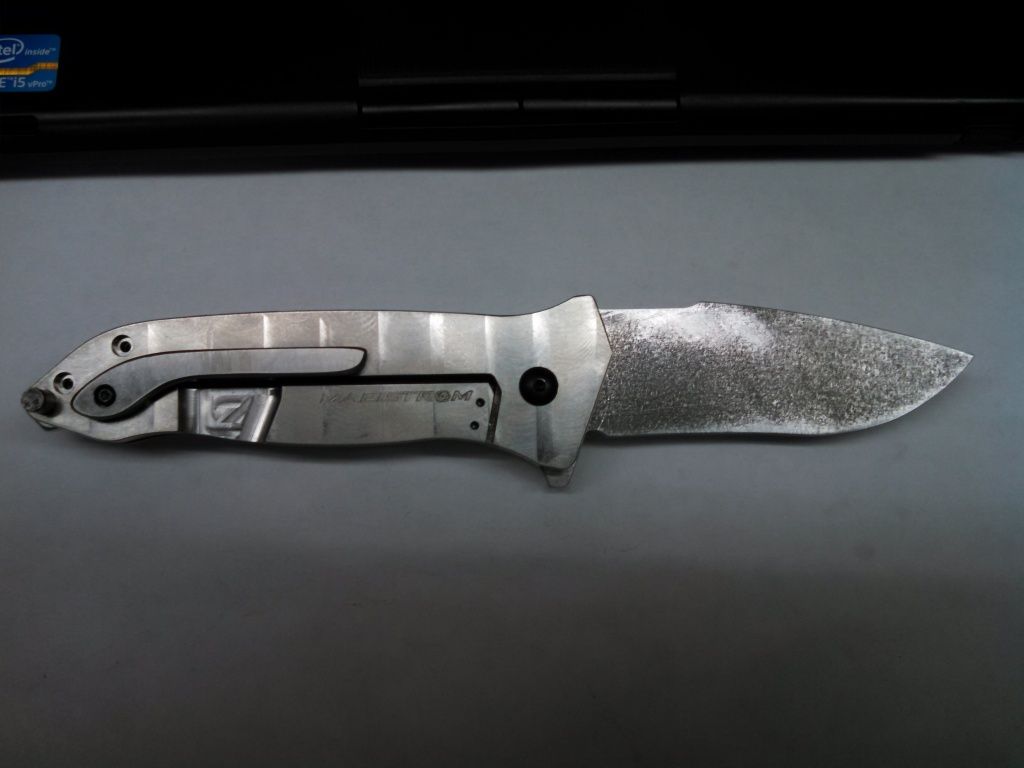
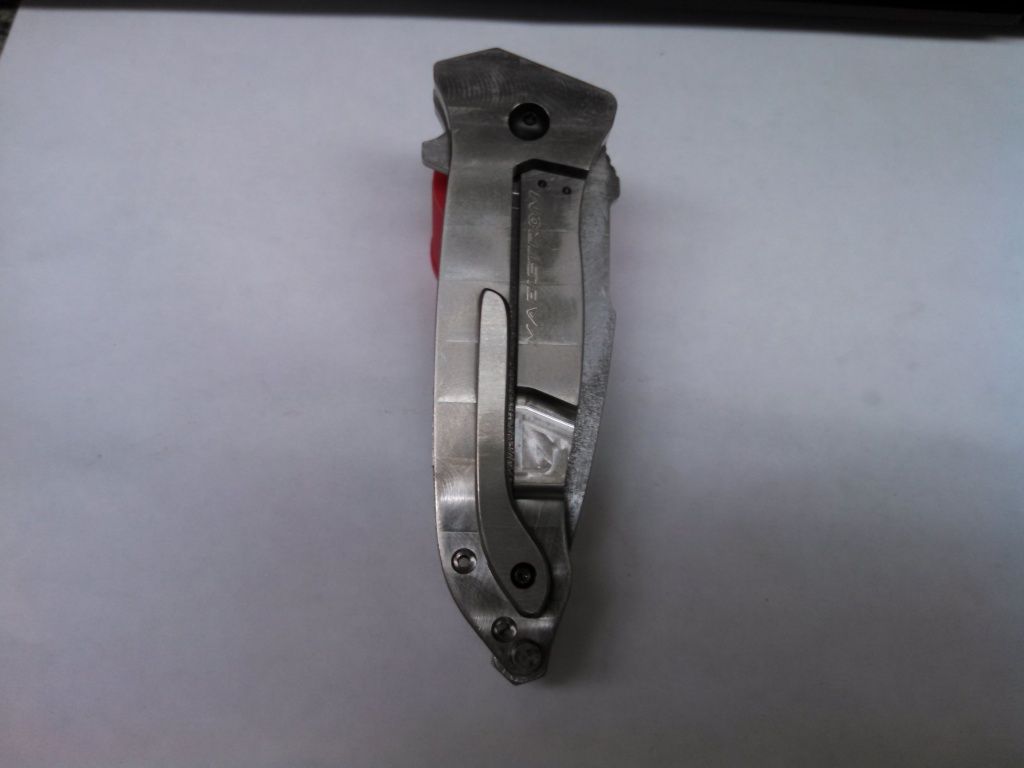
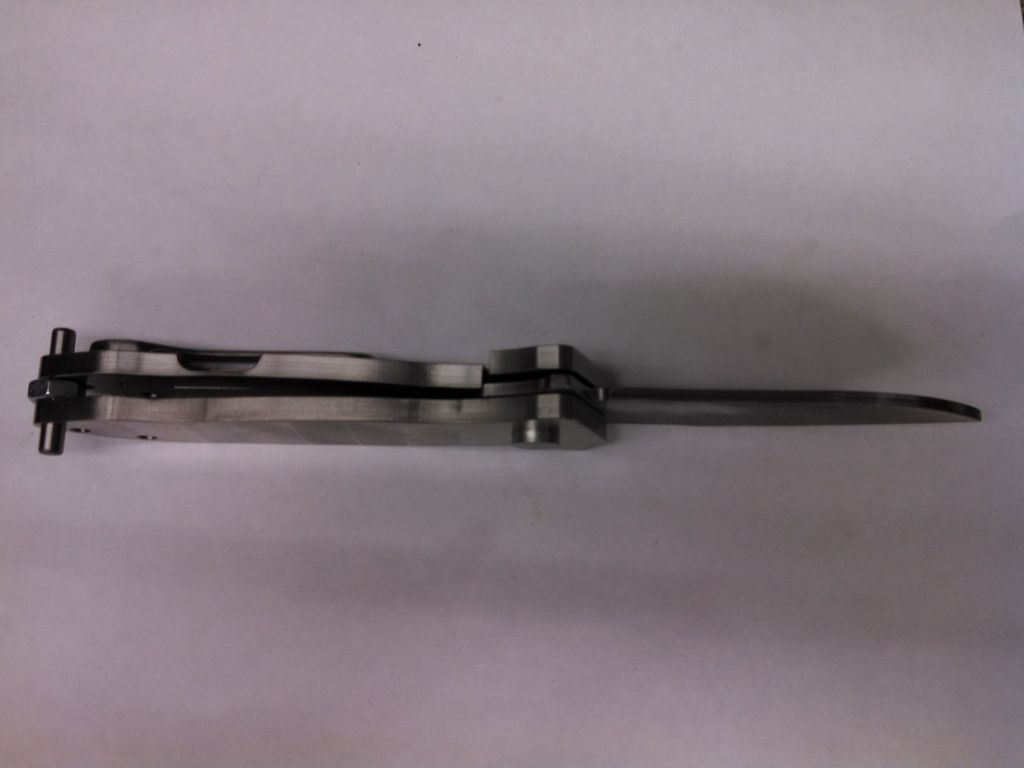
Please let me know your thoughts on the design. since it is still in the design phase, any changes are easy to make right now. I'd really like to have input.
:5: