Edwardshandmadeknives
Well-Known Member
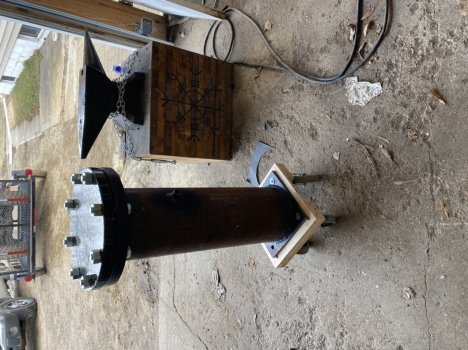
I don’t know why the picture insists on loading sideways, but here is what I built. I started trying to stabilize with a stainless vessel with a 1/2” Lexan lid, and first my vacuum pump crushed the chamber, so I built a stronger one, then it broke the lid. I decided to go a little heavier this time, and built this. It’s 28” of 8” diameter steel pipe, with a weld-on steel flange. I got the steel pipe scrap from a local plumbing shop, and had them order me the flanges and gasket. If anyone is thinking of going this route, it’s not terribly expensive. The scrap of pipe was free, and the flanges, bolts, and gasket set me back about $300. I paid a certified high pressure steam welder $100 to weld it all up, with a 1/2” threaded port to connect the piping to. It will handle all the vacuum I can throw at it (29.98”), plus I was told it should handle 500 psi. It’s going to be outfitted with a digital micron gauge for the vacuum and an analog 0-1000 psi pressure gauge. Now I just have to pipe it!