J S Machine
Well-Known Member
I am by no means a maker who can say that I have walked the talk when it comes to slipjoints, as I have only made a handful. However, during that time I have learned a great deal about them. I have also piled up a bucket full of concerns that I need to address. I would like to get some input on what the other makers here think about some of these problems.
Most of the time, we see the finished photos of knives in the member's albums. Rarely do we see or hear about the trials and tribulations, or the fixes to common problems that we all run in to. I often look at some of my pictures and think "wow, it sure looks nice but it was a long road and alot of headache to get it this way" lol.
Here is one of the things I struggle most with when it comes to slippies.
In this illustration, there are three seperate pictures. What we are looking at here is the cross section of a slipjoint half. this would be the liner, the bolster, and the handle material (scales). Let's just assume the end with the bolster is the pivot end. The bolster will be soldered to the liner. It could even be a milled liner - where the bolster and liner are all one piece.. Either way..
So in Figure 1, we see the holes. We have the pivot hole and the smaller hole which is used to hold either side of the scale down. It is my understanding that all these pins are peened, so the holes need to be tapered.
For those who don't understand this concept, the pin actually spreads when peened, and thus fills the tapered space. When this happens, it creats a kind of fastener -so to speak- that will hold everything together. If everything works the way it is supposed to, the pins "head" or upper portion spreads and fills the tapered hole opening correctly. when ground smooth, the pin is not visible, provided that we used the same materials for pin and bolster..
Figure 2 shows the pins (in red) correctly peened and spread out to fill the tapered space, and then ground smooth.
Figure 3 shows one of the most common problems I have. I don't know if it is that the pin material I'm using is too hard, or that I am not doing it correctly. I will install my pins in my holes, which are reamed, so the fit is tight or close to a slip fit. Most of the time I have to tap them in. Then, I will be sure the pin is only slightly longer than the half or two pieces I am working with. As I hammer the pin, the extra length mushrooms down and becomes a "head".
Often times, the pin will develop a kink below the surface of the hole, and it will try to bend at an angle. This will of course render any further blows with the hammer useless, because it is only going to bend further. Usually at this point, I drill the pin out or nock it out from the opposite side. I then try it again with a new pin. I know that hitting the pin dead on center of the hammer face and trying to strike it straight down is a big part of it..but sometimes it is very hard to tell if you are actually doing this or not. The results are usually bad..if a bent pin imposes enough pressure on the surrounding hole, it can not only elongate the hole, but even move the scale material in an undesired direction or even worse, bust it - if it is a fragile material like ivory or fossil materials.
The second issue I have is this: When peening my pivot pin, I am looking for several things at once. The first thing is to actually bring the two handle half assemblies together against the blade. The second thing is to be sure my pin is spreading equally on both sides and giving me enough fill to fill the tapered holes. The third thing is my blade action. Usually I will check my blade action after every blow, especially after I get close. I know that the fool proof way to do this is to put a piece of shim material inside the assembly between blade and liner. Then you can hammer as much as you need to in order to spread the pins effectively. Okay, but wait..
What if the pin actually increases in diameter right in the center?? I have had this happen on several knives. I have the correct spread on each side to fill the holes; the liners pull in together as they should and take up all the space except for a small gap of maybe .001 or .002", but then the blade gets hard to move. So how do I avoid the pin swelling in the very center, where the blade pivot hole is??
Most of the time, we see the finished photos of knives in the member's albums. Rarely do we see or hear about the trials and tribulations, or the fixes to common problems that we all run in to. I often look at some of my pictures and think "wow, it sure looks nice but it was a long road and alot of headache to get it this way" lol.
Here is one of the things I struggle most with when it comes to slippies.
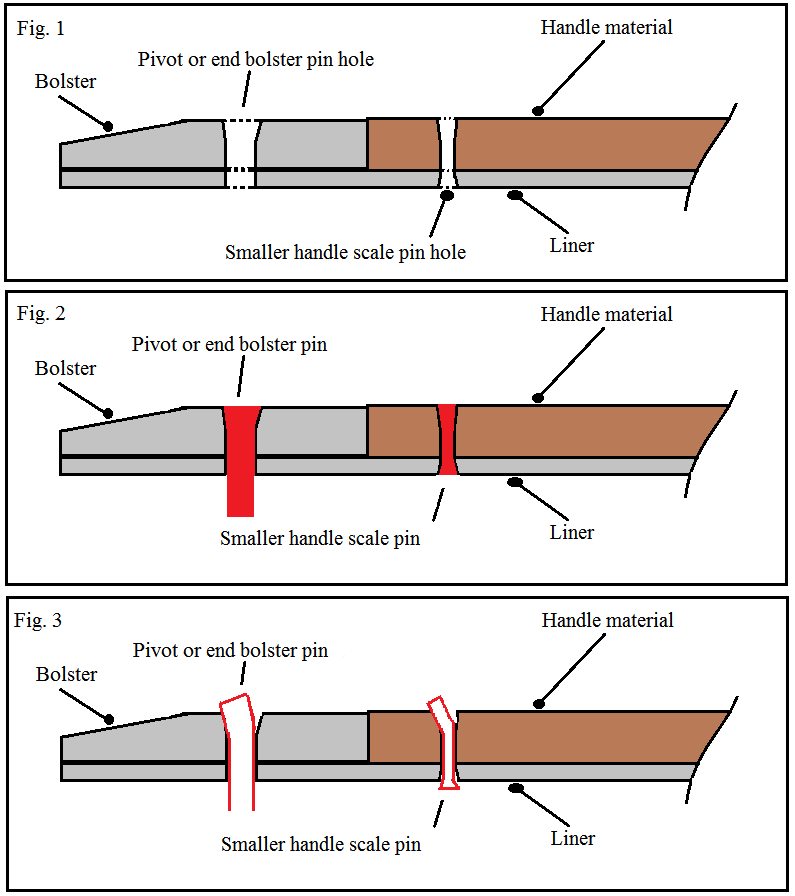
In this illustration, there are three seperate pictures. What we are looking at here is the cross section of a slipjoint half. this would be the liner, the bolster, and the handle material (scales). Let's just assume the end with the bolster is the pivot end. The bolster will be soldered to the liner. It could even be a milled liner - where the bolster and liner are all one piece.. Either way..
So in Figure 1, we see the holes. We have the pivot hole and the smaller hole which is used to hold either side of the scale down. It is my understanding that all these pins are peened, so the holes need to be tapered.
For those who don't understand this concept, the pin actually spreads when peened, and thus fills the tapered space. When this happens, it creats a kind of fastener -so to speak- that will hold everything together. If everything works the way it is supposed to, the pins "head" or upper portion spreads and fills the tapered hole opening correctly. when ground smooth, the pin is not visible, provided that we used the same materials for pin and bolster..
Figure 2 shows the pins (in red) correctly peened and spread out to fill the tapered space, and then ground smooth.
Figure 3 shows one of the most common problems I have. I don't know if it is that the pin material I'm using is too hard, or that I am not doing it correctly. I will install my pins in my holes, which are reamed, so the fit is tight or close to a slip fit. Most of the time I have to tap them in. Then, I will be sure the pin is only slightly longer than the half or two pieces I am working with. As I hammer the pin, the extra length mushrooms down and becomes a "head".
Often times, the pin will develop a kink below the surface of the hole, and it will try to bend at an angle. This will of course render any further blows with the hammer useless, because it is only going to bend further. Usually at this point, I drill the pin out or nock it out from the opposite side. I then try it again with a new pin. I know that hitting the pin dead on center of the hammer face and trying to strike it straight down is a big part of it..but sometimes it is very hard to tell if you are actually doing this or not. The results are usually bad..if a bent pin imposes enough pressure on the surrounding hole, it can not only elongate the hole, but even move the scale material in an undesired direction or even worse, bust it - if it is a fragile material like ivory or fossil materials.
The second issue I have is this: When peening my pivot pin, I am looking for several things at once. The first thing is to actually bring the two handle half assemblies together against the blade. The second thing is to be sure my pin is spreading equally on both sides and giving me enough fill to fill the tapered holes. The third thing is my blade action. Usually I will check my blade action after every blow, especially after I get close. I know that the fool proof way to do this is to put a piece of shim material inside the assembly between blade and liner. Then you can hammer as much as you need to in order to spread the pins effectively. Okay, but wait..
What if the pin actually increases in diameter right in the center?? I have had this happen on several knives. I have the correct spread on each side to fill the holes; the liners pull in together as they should and take up all the space except for a small gap of maybe .001 or .002", but then the blade gets hard to move. So how do I avoid the pin swelling in the very center, where the blade pivot hole is??