opaul
Well-Known Member
I saw an add where Fiddleback Forge is offering a one day 8 hour knife making class. The students (limit of 2) will take home a finished knife. I did a quick tally on knife making steps and I came up with about 15 total hours using 2- 1 hour tempering cycles.
My question is how will the blades be heat treated and tempered. Also a finished handle - so it must be fast setting epoxy.
Here is the link. It’s worth a read if you have 5 minutes to see the description.
fiddlebackforge.com
My question is how will the blades be heat treated and tempered. Also a finished handle - so it must be fast setting epoxy.
Here is the link. It’s worth a read if you have 5 minutes to see the description.
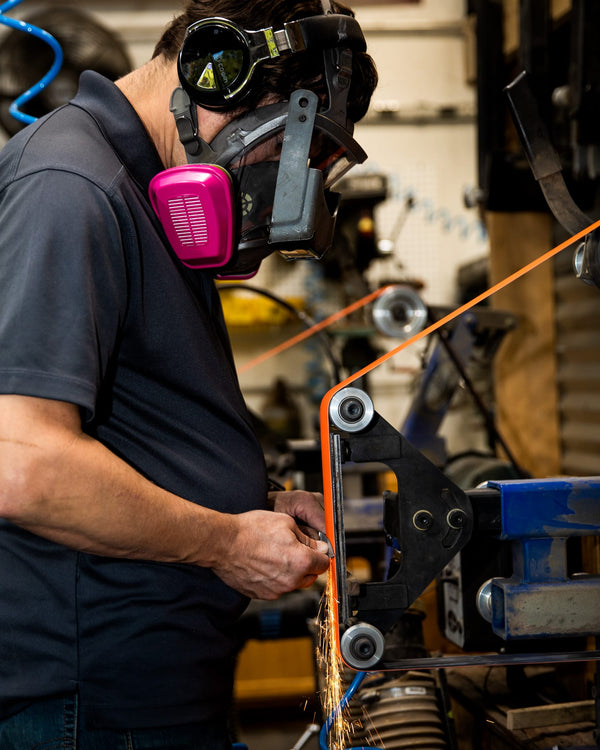
Fiddleback University - Knife Making Class - One Day In Person Training
Whether you are learning how to make your first knife, or looking to improve your current knife production as a professional knife maker, Fiddleback University will give you the skills necessary to meet your next goal in your knife making journey. In person classes are taught by Andy Roy of...
