Decided to build up a heat treat oven during my vacation! Chamber is 27" long, 7" wide and 6.5" tall and I used coil over quartz tubes across the top of the kiln like a few others have done. Auber Ramp/Soak/Wifi PID, dual SSR and heat sinks, 240v and a 3840 watt, 16amp element in 13 AWG Kanthal A1. I used RedBeard's wiring style/diagram for the electronics.
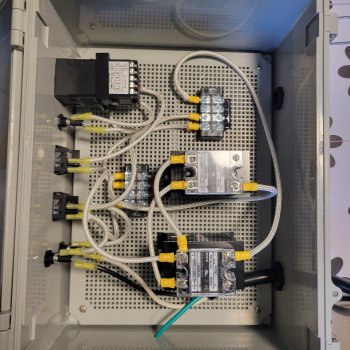
I suck at welding, but I welded up an angle iron frame for it. I used a self closing door hinge and rigged a spring mechanism to hold it tighter. I used a different limit switch as well than what others do.
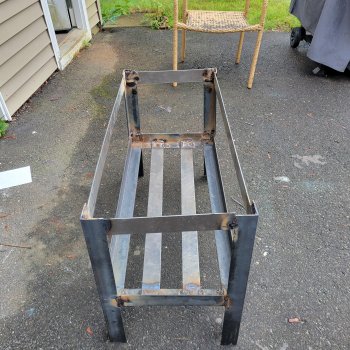
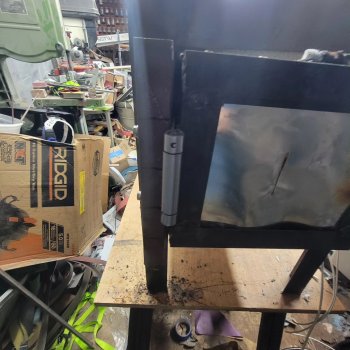

The rest was the generic K23 IFB build:
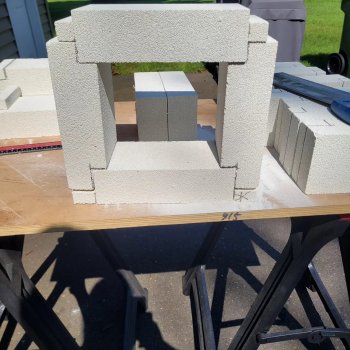
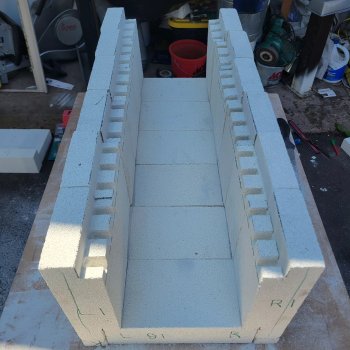
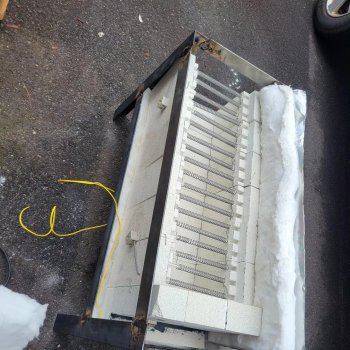
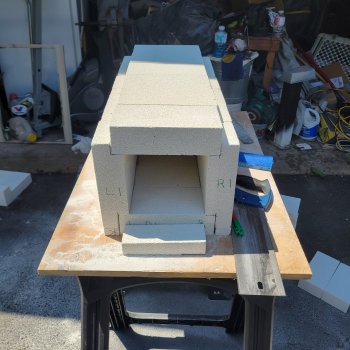
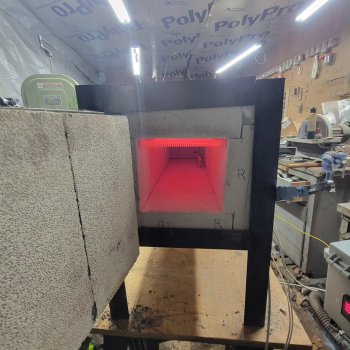
Gotta play with sealing the door better and 4 of the tubes broke when I was taking it up to 1900. The tubes were a very tight fit in the coils, and when I spaced out the coils, my jig was off, so there was a lot of tension between the elements. New element and tubes are ordered already.
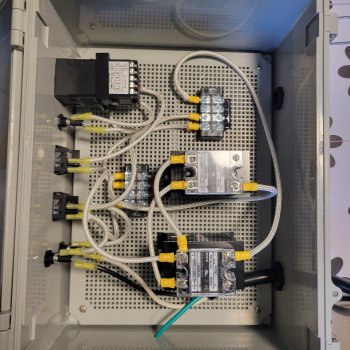
I suck at welding, but I welded up an angle iron frame for it. I used a self closing door hinge and rigged a spring mechanism to hold it tighter. I used a different limit switch as well than what others do.
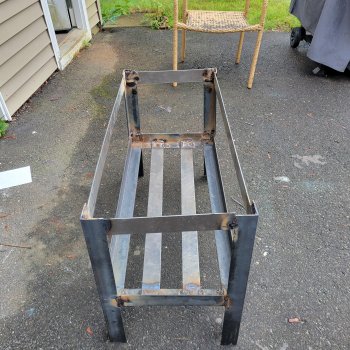
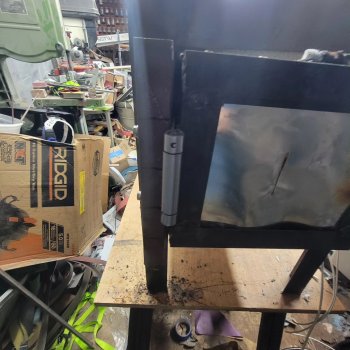

The rest was the generic K23 IFB build:
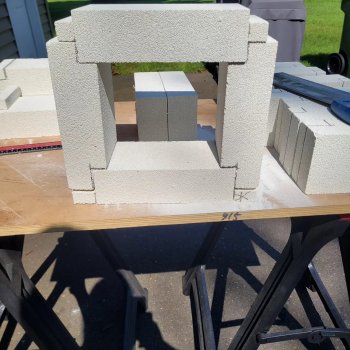
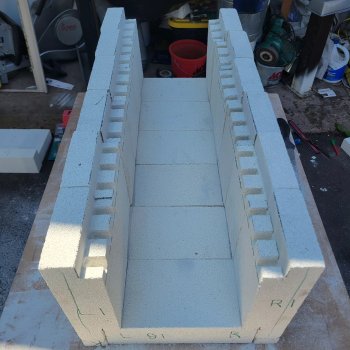
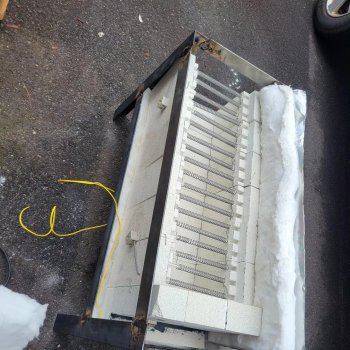
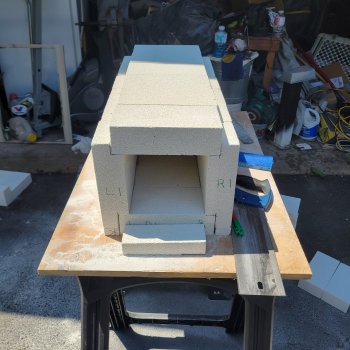
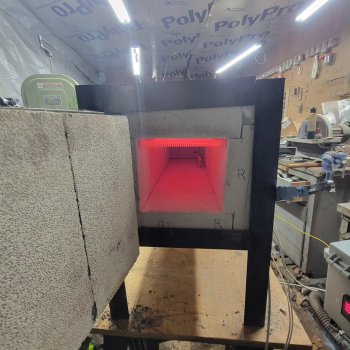
Gotta play with sealing the door better and 4 of the tubes broke when I was taking it up to 1900. The tubes were a very tight fit in the coils, and when I spaced out the coils, my jig was off, so there was a lot of tension between the elements. New element and tubes are ordered already.