Smallshop
KNIFE MAKER
So I did eventually manage to hard mill a blade. Was not fun. Ruined the blade due to the bow it introduced....$60 in endmills....no more hard milling...lol.
I did what I call "pattern machined". I did this to lessen the finish grinding.By leaving "valleys" there is much less material that need to be removed to get to sharp. The real solution to my problem (back pain limiting my grinding) is just to leave less stock. I left the blades .100 thick at the edge....way too much stock. I am going to change my roughing before heat treat...leave less...hate life less. Lol.
Here's what I came up with. Cuts nice...kinda interesting. Machine time is ridiculous long but grind time is amazingly short....what do I want to wear out first...a Ted or a CNC mill....
I want to try a few of these in the future...with the nice gray air cooled flat finish in the valleys and a fine grind on the high spots for contrast. I liked the result. My business partner hated it...but after 26 yrs of marriage this is not a first for her to not like one of my experiments....(let me know what you think please.)
those are Claro walnut blanks the prototypes are sitting on....!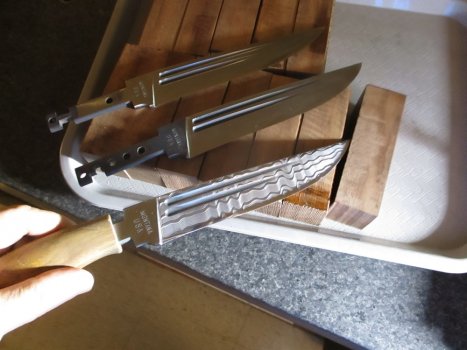
I did what I call "pattern machined". I did this to lessen the finish grinding.By leaving "valleys" there is much less material that need to be removed to get to sharp. The real solution to my problem (back pain limiting my grinding) is just to leave less stock. I left the blades .100 thick at the edge....way too much stock. I am going to change my roughing before heat treat...leave less...hate life less. Lol.
Here's what I came up with. Cuts nice...kinda interesting. Machine time is ridiculous long but grind time is amazingly short....what do I want to wear out first...a Ted or a CNC mill....
I want to try a few of these in the future...with the nice gray air cooled flat finish in the valleys and a fine grind on the high spots for contrast. I liked the result. My business partner hated it...but after 26 yrs of marriage this is not a first for her to not like one of my experiments....(let me know what you think please.)
those are Claro walnut blanks the prototypes are sitting on....!
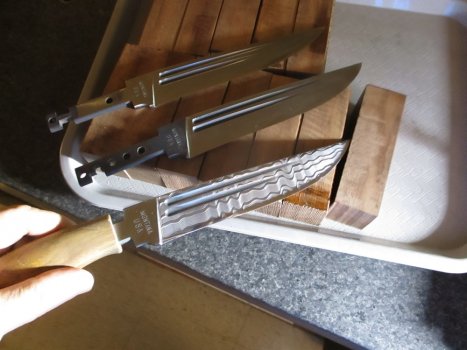