Gahagan
Well-Known Member
Ok I am perplexed. I am trying to get a hamon on some knives but it is not working very well. I have switched over to 1075 from normal w2 or 1095. I am applying the clay as usual but getting different results.
Here is how I am applying the clay
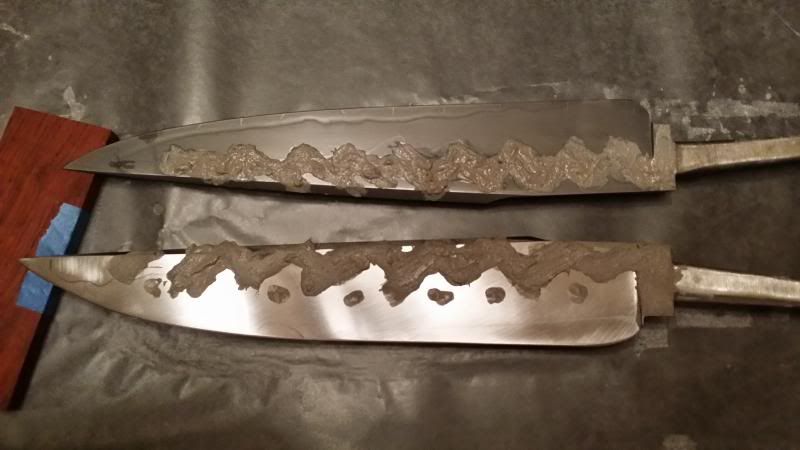
Normally I would get a hamon close to what I lay out slightly larger but now I am getting only the bottom 1/4 of the blade. I f you look at the top blade you can see the hamon from the first attempt with the same layout. Please provide me some insight into 1075. Do I need alot less area coverage and less alot less clay? How many times can I retry before I get major grain growth? I really am lost with this steel.
Here is how I am applying the clay
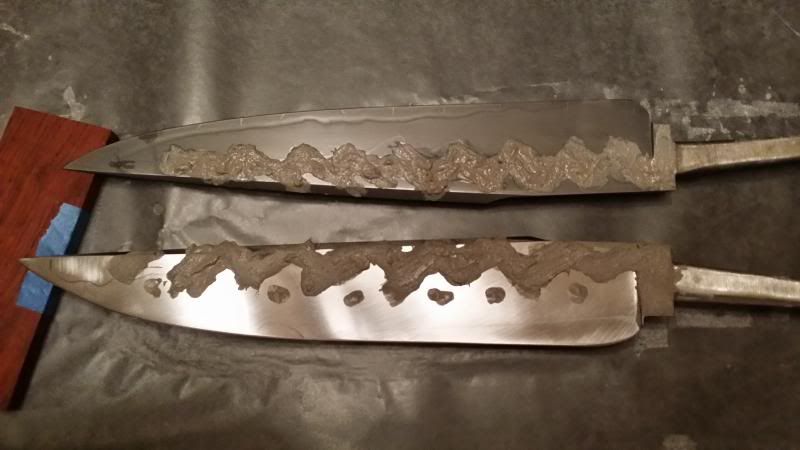
Normally I would get a hamon close to what I lay out slightly larger but now I am getting only the bottom 1/4 of the blade. I f you look at the top blade you can see the hamon from the first attempt with the same layout. Please provide me some insight into 1075. Do I need alot less area coverage and less alot less clay? How many times can I retry before I get major grain growth? I really am lost with this steel.