Nylund knives
Well-Known Member
Hi again,
I have now made a forge to do my forge welding but I have som trouble with the fine tuning of my burners. I have made a lot of changes cutting and welding to my forge thats why it is so ugly.
This is my current setup:
The inside is about 17 inch long with 3 layers 1" wool, inside dia is 6" and I have two burners, the hole for the gas inlet is 1/16.
I've also tried a single burner and only 2 layers of wool.
What should the flame look like inside the forge?
What I'm trying to get is some blue at the burners, about 2inches long blue flames, and some yellow flames out of the burner opening, "dragon breath" like in the picture. Is this right?
My main problem is probably that my blower is to large.
When I'm running at 7 psi and the bladevalve for the blower is 95% closed then everything is looking good, and I get welding heat but my burners have backfired a few times and starts burning inside the pipe. The nozzle on the burners look like this:
The bigger pipe is 1,5 inch dia. Can the door be to small?
If I open the gatevalve to about 80% I get long blue flames and no dragon breath. If I then turn up the gas to about 10 psi everything is looking good except that the wool starts melting inside my forge.
I run the forge for 20min today and in that time I hade melted away 1 inch of the 3 inches of wool.
Do you have any ideas?
Regards
Jakob
I have now made a forge to do my forge welding but I have som trouble with the fine tuning of my burners. I have made a lot of changes cutting and welding to my forge thats why it is so ugly.
This is my current setup:
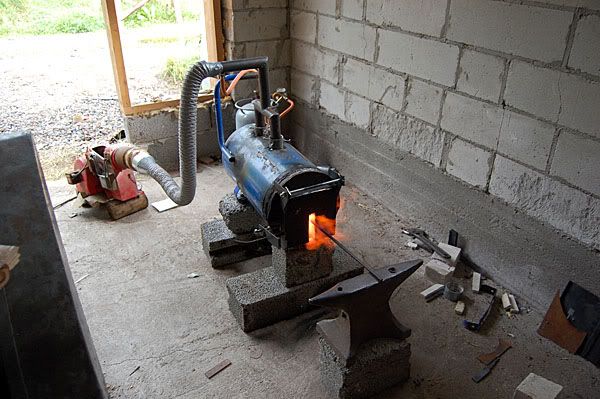
The inside is about 17 inch long with 3 layers 1" wool, inside dia is 6" and I have two burners, the hole for the gas inlet is 1/16.
I've also tried a single burner and only 2 layers of wool.
What should the flame look like inside the forge?
What I'm trying to get is some blue at the burners, about 2inches long blue flames, and some yellow flames out of the burner opening, "dragon breath" like in the picture. Is this right?
My main problem is probably that my blower is to large.
When I'm running at 7 psi and the bladevalve for the blower is 95% closed then everything is looking good, and I get welding heat but my burners have backfired a few times and starts burning inside the pipe. The nozzle on the burners look like this:
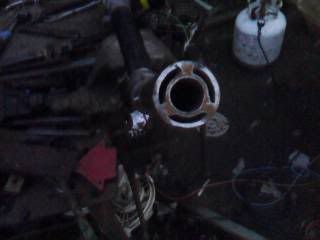
The bigger pipe is 1,5 inch dia. Can the door be to small?
If I open the gatevalve to about 80% I get long blue flames and no dragon breath. If I then turn up the gas to about 10 psi everything is looking good except that the wool starts melting inside my forge.
I run the forge for 20min today and in that time I hade melted away 1 inch of the 3 inches of wool.
Do you have any ideas?
Regards
Jakob