Rev 1
Used a 1x1/8 strap, tack welded on 3/16 rod & 1" square tube. Just did tack welds so I can break the positions and move, if necessary.
Decided to try a 1" square tube, thinking that the tube shape might give better control. The bend in the lower part of the support seems important, that gives the lower fingers a control surface while grinding. That bend angle may need some refinement, it was just a wild guess.
Ground the rod down to just wider than the .060 blade I tested this on. Ground a thumb relief on the top, thinking it would allow a better touch/feel for control and temperature sensing.
Added a piece of nylon sticky back tape to the surface allowing blade to slide across support easier.
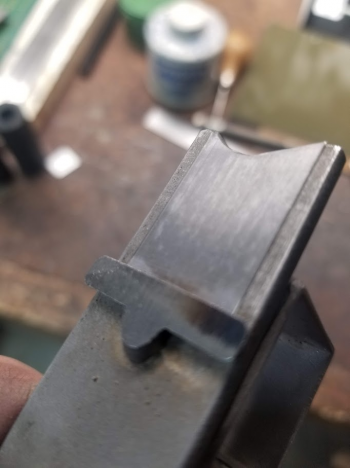
There's definitely a learning curve using this thing - keeping in mind that I'm a novice free hand grinder. I did a couple of quick grinds and it passed the "bozo" test, and seems worth spending more time seeing how it works out. Depending on primary grind angle, the support rod may grind down to the same thickness as the blade. So, after grinding this .060" in blade, will this work on a .125" blade? Gotta try that out, though 1/8 blades or thicker are not that big a problem. Perhaps I need a set of these depending on blade thickness.
I can see that the fit & feel of this thing is somewhat dependent on hand size. But, so far it seems to work pretty good... I think.
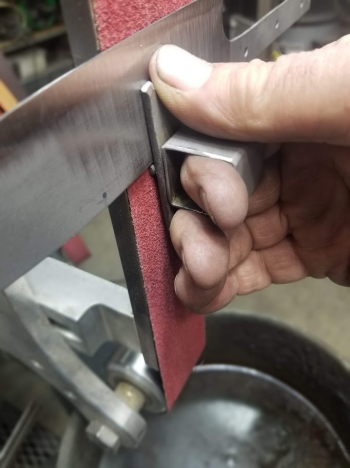
Easy to make. If you don't have a welder, the pieces could simply be attached with epoxy/JB Weld.
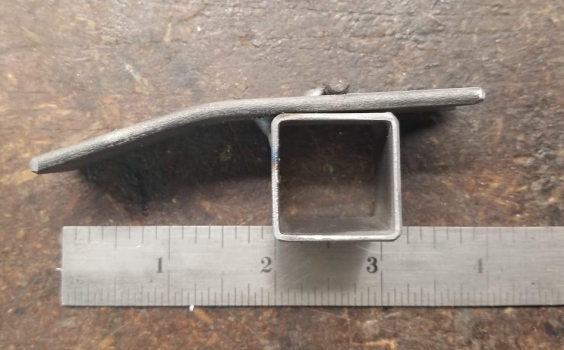