It's been a while since I've melted metal, so tonight I decided to melt up some for a bolster on a knife I'm working on. I had been reading on shibuichi, which is an alloy of copper and silver, and I wanted to give it a try. I've got some silver and copper squirreled away for the real stuff, but just for messing around tonight I used some silver brazing rod. It's 15% silver, with the rest being copper and a bit of phosphorous. My normal casting rig is more set up for casting alot bigger amounts of metal than what I wanted to cast, so I improvised. Now using steel for a crucible isn't the best option especially for copper alloys as the temp is high enough to make the crucible possibily fail, and some of the iron will dissolve into the melt affecting the alloy. But for something this small a really thick walled steel crucible will be fine, I'm not concerned with having a "proper" alloy as I'm just tinkering around here, so I used an old 1 1/4 shallow well impact socket that I welded up the bottom on. It makes a nice heavy walled crucible with a thick floor, once it's up to heat it stays there for a while. Here it is charged with all the brazing rod cut up and some hardwood for a cover.
Lots of folks use charcoal for a cover, but I've had good luck using just plain old hardwood, in this case it's black walnut. It turns into charcoal in the forge pretty dang quick anyways
So into my little forge the crucible goes, this small of a melt doesn't take too long to get liquid. For a mold I used just an openfaced mold made from walnut, yup just a pocket carved in walnut. I've played around with wooden molds before and to my supprise it works pretty well. You're not going to get a really accurate reproduction of what you carved, but you'd be supprised. I wouldn't do big stuff in wood as sometimes it can get a bit hairy, and only shallow openfaced molds, but for small stuff I've never had a problem. Another plus of using wood, is the metal doesn't oxidize as all the excess oxygen is burnt up by the wood. I've even used plain old carved up 2x4's. Here it is after pouring in the wood
Pardon the last two pics as they were taken on my phone. I like alloying my own bronzes compared to buying a piece of bronze and machining it to shape, I think it adds character. I personally HATE brass, and I hate casting it. Beware that brass contains zinc, and at casting temp it smokes, which isn't really smoke but the zinc boiling off of the brass, DON'T BREATHE THE VAPOR, zinc fume fever is no fun, I've had it and I wouldn't wish it on anyone. If you do taste a metalic taste in your mouth, drink LOTS of milk.
Lots of different alloys can be made with copper, scrap copper can be used, and I've used tin solder to make a traditional bronze, different ammounts of tin will make different shades. I've even used plain old 60/40 solder and copper to make bronze. You can alloy copper with aluminum to make an aluminum bronze, usually anything over 10% aluminum will get pretty brittle. It's a very pretty bronze and tough as nails, but a pain to cast. There will be shrink voids, inclusions, and it forms an oxidation "skin" when the liquid is in the air between the crucible and mold. But for all it's difficulties, when you get it right, it's an awesome metal.
This is the first time I've done a copper-silver alloy, and I'm gonna use it for the bolster on the knife I'm slowly working on, it turned out pretty good, here is the little chunk that I casted tonight, I ground and polished a bit of it and used birchwood casey cold blue to blacken it up a bit, here it is next to the blade that I'm working on.
Now to make a bolster out of it. Thanks for watching folks
Zeb
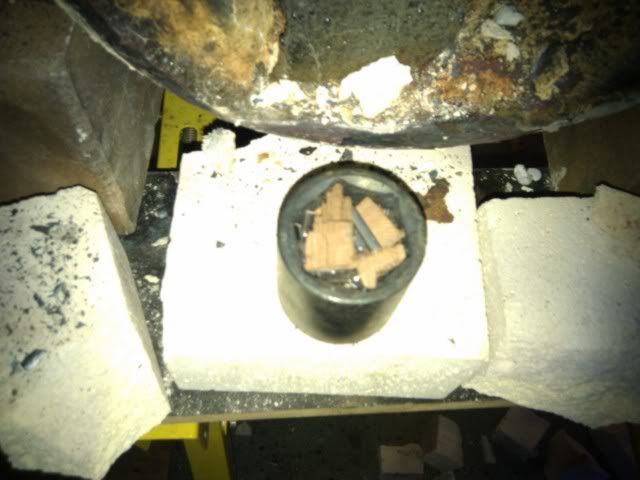
Lots of folks use charcoal for a cover, but I've had good luck using just plain old hardwood, in this case it's black walnut. It turns into charcoal in the forge pretty dang quick anyways
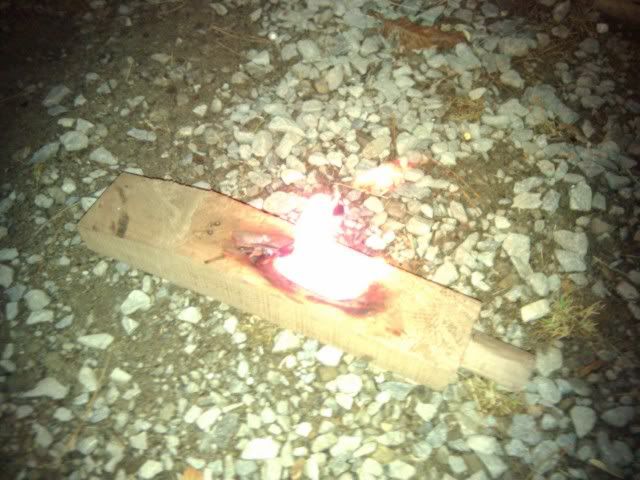
Pardon the last two pics as they were taken on my phone. I like alloying my own bronzes compared to buying a piece of bronze and machining it to shape, I think it adds character. I personally HATE brass, and I hate casting it. Beware that brass contains zinc, and at casting temp it smokes, which isn't really smoke but the zinc boiling off of the brass, DON'T BREATHE THE VAPOR, zinc fume fever is no fun, I've had it and I wouldn't wish it on anyone. If you do taste a metalic taste in your mouth, drink LOTS of milk.
Lots of different alloys can be made with copper, scrap copper can be used, and I've used tin solder to make a traditional bronze, different ammounts of tin will make different shades. I've even used plain old 60/40 solder and copper to make bronze. You can alloy copper with aluminum to make an aluminum bronze, usually anything over 10% aluminum will get pretty brittle. It's a very pretty bronze and tough as nails, but a pain to cast. There will be shrink voids, inclusions, and it forms an oxidation "skin" when the liquid is in the air between the crucible and mold. But for all it's difficulties, when you get it right, it's an awesome metal.
This is the first time I've done a copper-silver alloy, and I'm gonna use it for the bolster on the knife I'm slowly working on, it turned out pretty good, here is the little chunk that I casted tonight, I ground and polished a bit of it and used birchwood casey cold blue to blacken it up a bit, here it is next to the blade that I'm working on.
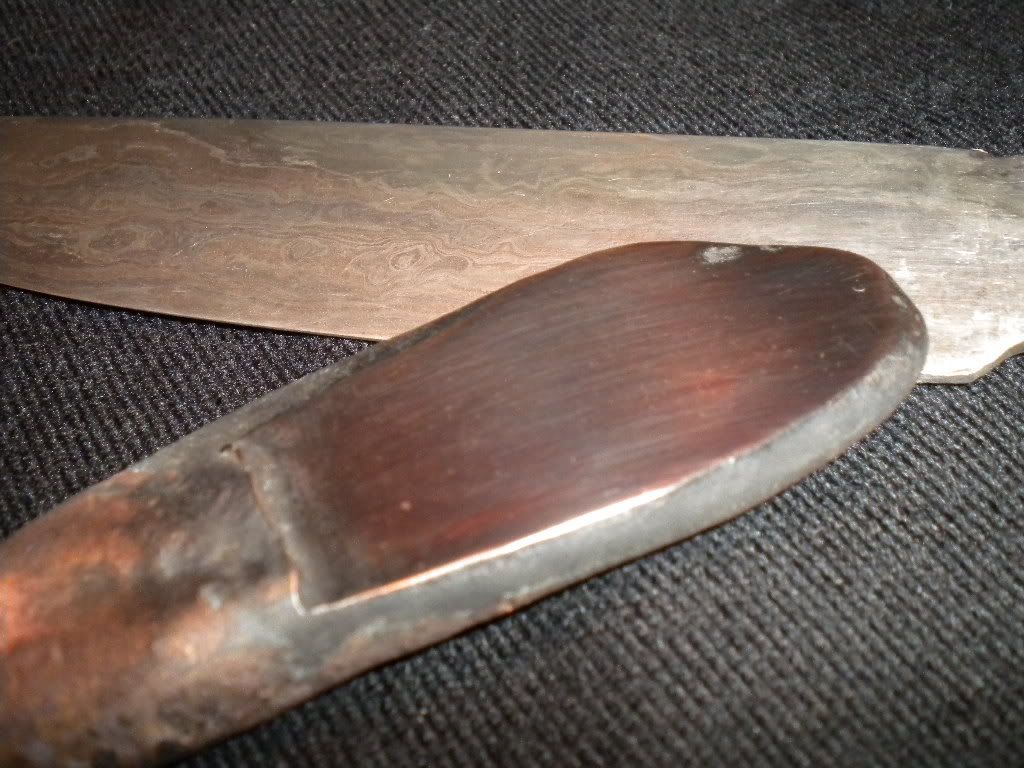
Now to make a bolster out of it. Thanks for watching folks
Zeb