Graham Fredeen
Well-Known Member
Hello Bruce and Friends, I hope you don't mind me posting this here. I've always felt more at home in Bruce's forums here than the other sections:
Some of you may remember me from a while ago (about 5 years), and many more may not. I am sure that there are quite a few new faces that have come and gone in that time. For those that I recognize, hello again, and for those who I don't pleasure to meet you.
My lengthy absence is the result of starting a new career and moving across the country. Back in 2011 I moved from Colorado to Michigan to work as an engineer at a steel mill. I went with hopes of having success with my career, getting a decent house and a nice shop setup to make knives, buy a bunch of much desired equipment to fill said shop, etc. Well, that pretty much came true, but there was one element lacking in all of this, time outside of work to do much of anything. It didn't start out that bad, for the first 6 months I was able to get my new shop (36'x48' pole barn) wired, insulated, heated, and on its way to being filled up with new tools/equipment. However, after this time, I was involved with a series of major capital projects at the mill that basically consumed any work life balance I once had. I was involved in the construction, cold and hot commissioning of about $155M worth of new equipment, namely a new continuous caster, followed by a twin tank vacuum degas system, then was responsible for maintenance of these areas, having to fight through all of the new equipment teething problems along the way. I did this for a couple of years until I eventually was placed in charge of all maintenance in the Mill's Melt Shop (Electric Arc Furnace, Ladle Metallurgy Furnace, Vacuum Degasser, Caster, and all support systems, with a team of 44 reporting to me). This may sound all good and fine to those who haven't ever worked in a steel mill, and don't get me wrong, it wasn't all bad, lots of great experience, very interesting work, processes, equipment, etc. never boring, but running maintenance in a steel mill is very demanding work. I have seen more things destroyed, damaged, broken down, caught fire, blown up (literally), ripped out, and mangled, than many will see in their lives, and I've had to be the one to put it all back together, more often than not at 3 am on a Sunday... I am very good at troubleshooting systems, devising plans of repair, directing manpower, etc. and for all of that, I got the reward of having to shoulder most of the catastrophes that happened in my particular steel mill. This would have been all good and fine, and worth the sacrifice of my time (in exchange for career advancement), but throw in a heaping pile of politics, a revolving door of poor upper management, economic and business struggles and the resulting changes, and my career quickly became one that was not very desirable and the rewards were no longer worth the sacrifices. I watched a large number of my peers leave the company (retire if they could, the good ones quit and moved on, and there were some "strategic head count reductions" as well), none of which made my work load lighter or easier. Late 2015 I decided it was time to see what else was out there for a career and I found a new position with another Steel Producer in the area, which promises to be better financially, and also in the work-life balance aspect as well. Having just concluded my time with my previous employer, I am set to start with my new one next week. So, that short novel is a very condensed account of where I have been for the past 5 years, and as you can guess, why I haven't been on the bladesmithing scene.
With all my time spent working and what little time off spent mainly trying to keep up with life's other responsibilities, I didn't do much shop work in the past 5 years, although, I did try at times. My feeble attempts resulted in only 2 knives, and a couple other blacksmithing projects (steel roses, and the sort) over my 5 year span. Not impressive by any means, and it is something that I have missed a lot in my life (a good creative outlet, stress relief, source of a lot of pride and satisfaction, etc).
I thought I would take the time now however to share the result of one of the knives I actually finished, and this one is pretty special. Bare with the back story if you will, I worked with a gentleman, another Maintenance Supervisor in the mill who retired back in 2014 (Dave Nadeau). We went back to when I was first starting out with the company, we were assigned to the New Caster project together. We spent the better part of a year and a half on the project together working side by side to fight all of the problems, make things right, fighting with management to spend money on things that needed to be done, troubleshooting issues, running utility piping, building platforms and grating for maintenance access, buying a few million dollars worth of spare parts, developing the maintenance systems for the new machine, etc. It was an uphill battle all the way, but it was a very valuable and rewarding experience working with Dave. Dave worked for many years as skilled trades as a hydraulic technician and his understanding of industrial hydraulics was immense (I learned a great deal from him) and he had a manner of being extremely organized, following through with pretty much everything, and being able to direct manpower and get jobs done, definitely the best maintenance supervisor that plant ever had. We found that we were very like minded and similar in many ways and through our struggles together, formed a strong bond. For political reasons the maintenance superintendent at the time eventually moved Dave over to the Electric Arc Furnace to clean up after another supervisor had made a mess of the area and I was left to deal with the caster. Being near the end of his career, with 34 years in the industry, and with lack of support, and stress affecting his health, he decided to retire. Because of our close bond and all of the things that we had been through together I wanted to do something special for his retirement. Back in 2012, when we started up the New Caster, I was able to save some of the steel from the very fist successfully produced heat. I took some of this and decided to make a knife out of it.
So without any further writing (hope this will be worth all the reading) here is the result:
I started the knife back in July of 2014 over a vacation I took the week of 4th of July. I did most of the pattern welding then and then, forged, ground, and heat treated the blade over various weekends in between, and finished the knife over Thanksgiving of 2014. From there it took me quite awhile to get around to making the sheath, and then up until now to finally get proper pictures of it taken. So it's been a bit of a work in progress for a good long while. I wanted to do everything on this knife myself, 100% sole authorship, due to it's personal significance, down to the pictures. While they aren't on the level of Jim Cooper (for example), I think I did ok.
As for the knife itself, here are the stats:
OAL: 10.875"
Blade Length: 6.25"
Handle: Desert Ironwood Burl
Mosaic Pattern Welded Blade composed of 15N20, 1095, and roughly 30% 1040 from the first heat from the New Caster.
Guard: 1040 from New Caster, Nitre Blued, 410 Stainless Spacers, coin edged
Sheath: Crafted by me, with Diamond Back Rattle Snake Insert.
Custom display stand with engraved plaque
Overall, not too shabby for someone as rusty with his knife making as I have been.
Thanks for tolerating the length of this one. Hope you folks like it and let me know what you think. I'm hoping that with the new job 2016 will see me in the shop more than I have been in a long time and back in the bladesmithing scene.
Some of you may remember me from a while ago (about 5 years), and many more may not. I am sure that there are quite a few new faces that have come and gone in that time. For those that I recognize, hello again, and for those who I don't pleasure to meet you.
My lengthy absence is the result of starting a new career and moving across the country. Back in 2011 I moved from Colorado to Michigan to work as an engineer at a steel mill. I went with hopes of having success with my career, getting a decent house and a nice shop setup to make knives, buy a bunch of much desired equipment to fill said shop, etc. Well, that pretty much came true, but there was one element lacking in all of this, time outside of work to do much of anything. It didn't start out that bad, for the first 6 months I was able to get my new shop (36'x48' pole barn) wired, insulated, heated, and on its way to being filled up with new tools/equipment. However, after this time, I was involved with a series of major capital projects at the mill that basically consumed any work life balance I once had. I was involved in the construction, cold and hot commissioning of about $155M worth of new equipment, namely a new continuous caster, followed by a twin tank vacuum degas system, then was responsible for maintenance of these areas, having to fight through all of the new equipment teething problems along the way. I did this for a couple of years until I eventually was placed in charge of all maintenance in the Mill's Melt Shop (Electric Arc Furnace, Ladle Metallurgy Furnace, Vacuum Degasser, Caster, and all support systems, with a team of 44 reporting to me). This may sound all good and fine to those who haven't ever worked in a steel mill, and don't get me wrong, it wasn't all bad, lots of great experience, very interesting work, processes, equipment, etc. never boring, but running maintenance in a steel mill is very demanding work. I have seen more things destroyed, damaged, broken down, caught fire, blown up (literally), ripped out, and mangled, than many will see in their lives, and I've had to be the one to put it all back together, more often than not at 3 am on a Sunday... I am very good at troubleshooting systems, devising plans of repair, directing manpower, etc. and for all of that, I got the reward of having to shoulder most of the catastrophes that happened in my particular steel mill. This would have been all good and fine, and worth the sacrifice of my time (in exchange for career advancement), but throw in a heaping pile of politics, a revolving door of poor upper management, economic and business struggles and the resulting changes, and my career quickly became one that was not very desirable and the rewards were no longer worth the sacrifices. I watched a large number of my peers leave the company (retire if they could, the good ones quit and moved on, and there were some "strategic head count reductions" as well), none of which made my work load lighter or easier. Late 2015 I decided it was time to see what else was out there for a career and I found a new position with another Steel Producer in the area, which promises to be better financially, and also in the work-life balance aspect as well. Having just concluded my time with my previous employer, I am set to start with my new one next week. So, that short novel is a very condensed account of where I have been for the past 5 years, and as you can guess, why I haven't been on the bladesmithing scene.
With all my time spent working and what little time off spent mainly trying to keep up with life's other responsibilities, I didn't do much shop work in the past 5 years, although, I did try at times. My feeble attempts resulted in only 2 knives, and a couple other blacksmithing projects (steel roses, and the sort) over my 5 year span. Not impressive by any means, and it is something that I have missed a lot in my life (a good creative outlet, stress relief, source of a lot of pride and satisfaction, etc).
I thought I would take the time now however to share the result of one of the knives I actually finished, and this one is pretty special. Bare with the back story if you will, I worked with a gentleman, another Maintenance Supervisor in the mill who retired back in 2014 (Dave Nadeau). We went back to when I was first starting out with the company, we were assigned to the New Caster project together. We spent the better part of a year and a half on the project together working side by side to fight all of the problems, make things right, fighting with management to spend money on things that needed to be done, troubleshooting issues, running utility piping, building platforms and grating for maintenance access, buying a few million dollars worth of spare parts, developing the maintenance systems for the new machine, etc. It was an uphill battle all the way, but it was a very valuable and rewarding experience working with Dave. Dave worked for many years as skilled trades as a hydraulic technician and his understanding of industrial hydraulics was immense (I learned a great deal from him) and he had a manner of being extremely organized, following through with pretty much everything, and being able to direct manpower and get jobs done, definitely the best maintenance supervisor that plant ever had. We found that we were very like minded and similar in many ways and through our struggles together, formed a strong bond. For political reasons the maintenance superintendent at the time eventually moved Dave over to the Electric Arc Furnace to clean up after another supervisor had made a mess of the area and I was left to deal with the caster. Being near the end of his career, with 34 years in the industry, and with lack of support, and stress affecting his health, he decided to retire. Because of our close bond and all of the things that we had been through together I wanted to do something special for his retirement. Back in 2012, when we started up the New Caster, I was able to save some of the steel from the very fist successfully produced heat. I took some of this and decided to make a knife out of it.
So without any further writing (hope this will be worth all the reading) here is the result:
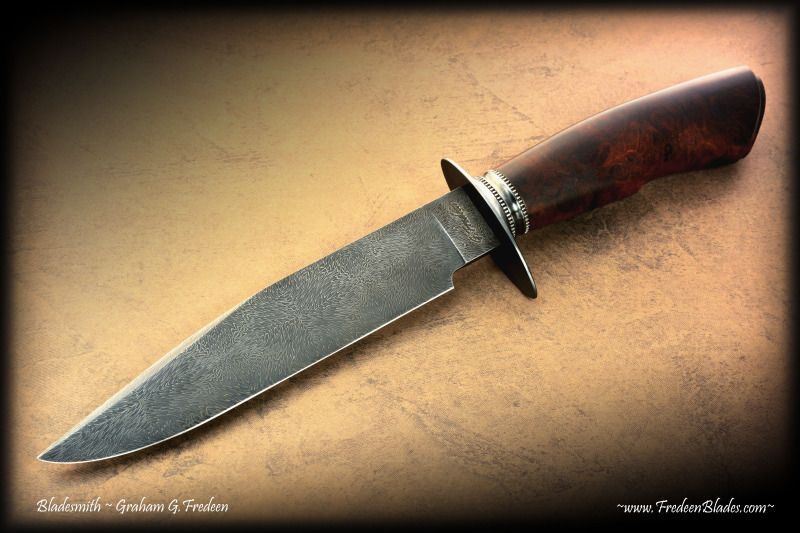
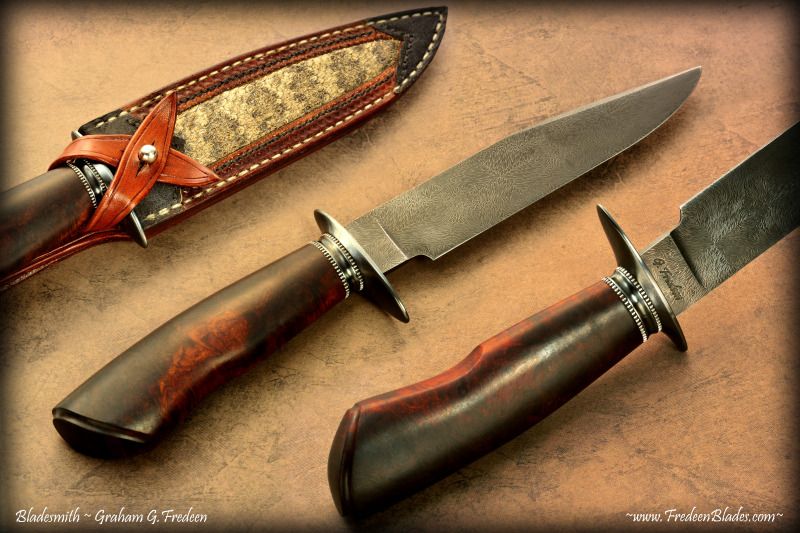
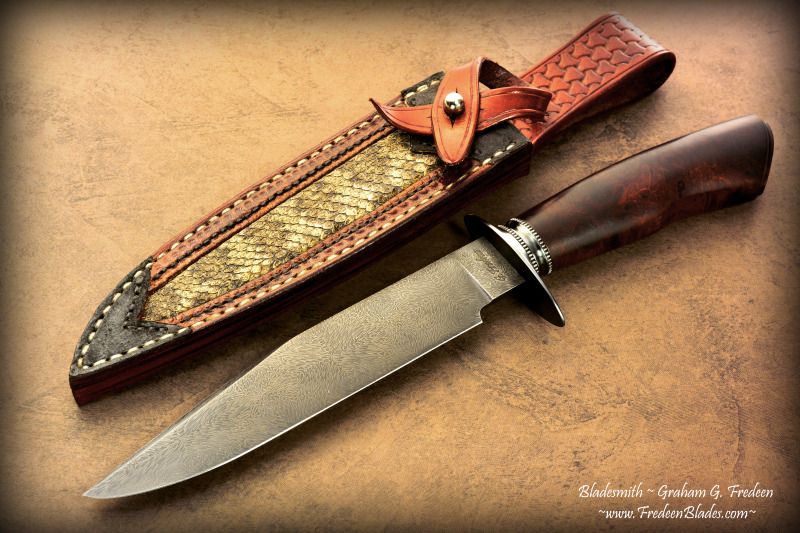

I started the knife back in July of 2014 over a vacation I took the week of 4th of July. I did most of the pattern welding then and then, forged, ground, and heat treated the blade over various weekends in between, and finished the knife over Thanksgiving of 2014. From there it took me quite awhile to get around to making the sheath, and then up until now to finally get proper pictures of it taken. So it's been a bit of a work in progress for a good long while. I wanted to do everything on this knife myself, 100% sole authorship, due to it's personal significance, down to the pictures. While they aren't on the level of Jim Cooper (for example), I think I did ok.
As for the knife itself, here are the stats:
OAL: 10.875"
Blade Length: 6.25"
Handle: Desert Ironwood Burl
Mosaic Pattern Welded Blade composed of 15N20, 1095, and roughly 30% 1040 from the first heat from the New Caster.
Guard: 1040 from New Caster, Nitre Blued, 410 Stainless Spacers, coin edged
Sheath: Crafted by me, with Diamond Back Rattle Snake Insert.
Custom display stand with engraved plaque
Overall, not too shabby for someone as rusty with his knife making as I have been.
Thanks for tolerating the length of this one. Hope you folks like it and let me know what you think. I'm hoping that with the new job 2016 will see me in the shop more than I have been in a long time and back in the bladesmithing scene.