MTBob
Well-Known Member
One thing I dislike is hand sanding - on anything. So to preserve my aging hands I'm always looking for a way for a machine to do the work. I've begun making more kitchen knives and I've fiddled around with some grinder attachments that seem to offer a way to get a hand sanded look in rather short order.
Here's what I've done:
For a while I tried using rubber contact wheels, 2",4",10", but I found it resulted in a belt bump irregularity that wasn't good and it didn't provide enough flatness for a smooth look. Some time ago I added a horizontal platen to my grinder (red angle iron piece) that's used with a T bar setup to sharpen knives.
I tried using it with Gator belts to finish kitchen knives. The flat metal horizontal platen worked OK, but didn't offer any softness to the blade shape, particularly if there is a convex curve.
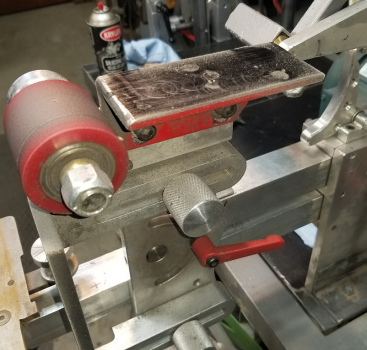
So I thought well why not added the leather softener I use on the vertical platen. It's held on with some magnets.
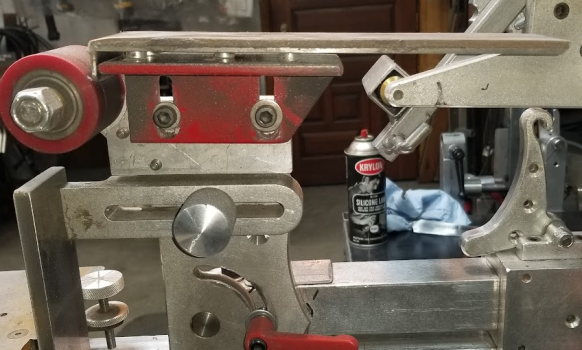
This platen attachment is set higher than the front contact wheel so that the only contact is on the flat surface. Spraying a little silicone on the leather surface minimizes friction.
The belt is run slowly in reverse direction, about 40% on the VFD. This effectively turns the process into a hand operated surface grinder / sander. It also assists transitioning from the primary grind flat onto the ricasso area without a noticeable plunge line. This same arrangement could also be performed on the vertical platen, but the position is not as easy to use as with the horizontal setup.
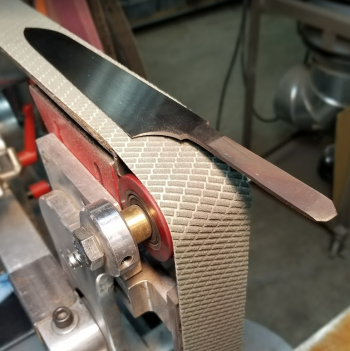
Here's the result with A100 / 180 grit gator belt. For sure, I'm not a hand sanding expert. But, this method seems to offer a good enough finish. Of course finer grits offer a shinier surface, but I'm not fond of that look. The long flat leather platen smooths out any irregularities created from previously grinding the primary angle, perhaps even better than what's achieved by hand sanding.
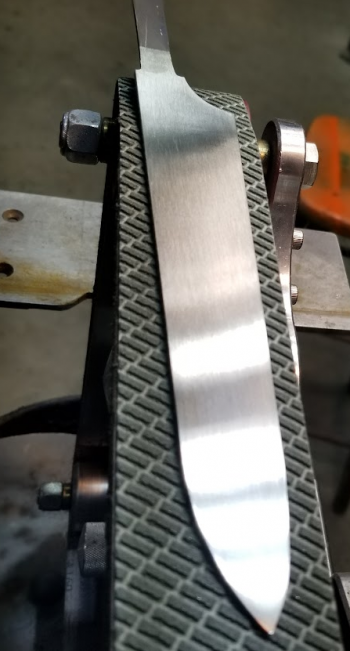
(Comments & critiques are welcome)
Here's what I've done:
For a while I tried using rubber contact wheels, 2",4",10", but I found it resulted in a belt bump irregularity that wasn't good and it didn't provide enough flatness for a smooth look. Some time ago I added a horizontal platen to my grinder (red angle iron piece) that's used with a T bar setup to sharpen knives.
I tried using it with Gator belts to finish kitchen knives. The flat metal horizontal platen worked OK, but didn't offer any softness to the blade shape, particularly if there is a convex curve.
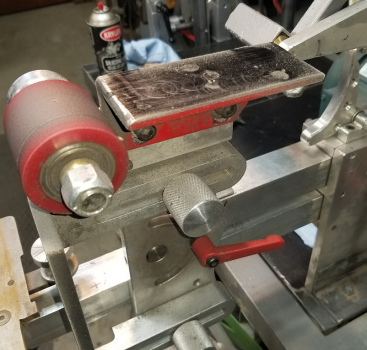
So I thought well why not added the leather softener I use on the vertical platen. It's held on with some magnets.
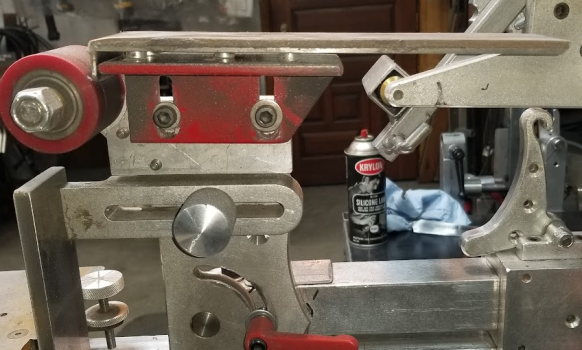
This platen attachment is set higher than the front contact wheel so that the only contact is on the flat surface. Spraying a little silicone on the leather surface minimizes friction.
The belt is run slowly in reverse direction, about 40% on the VFD. This effectively turns the process into a hand operated surface grinder / sander. It also assists transitioning from the primary grind flat onto the ricasso area without a noticeable plunge line. This same arrangement could also be performed on the vertical platen, but the position is not as easy to use as with the horizontal setup.
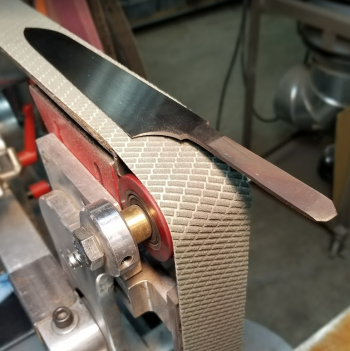
Here's the result with A100 / 180 grit gator belt. For sure, I'm not a hand sanding expert. But, this method seems to offer a good enough finish. Of course finer grits offer a shinier surface, but I'm not fond of that look. The long flat leather platen smooths out any irregularities created from previously grinding the primary angle, perhaps even better than what's achieved by hand sanding.
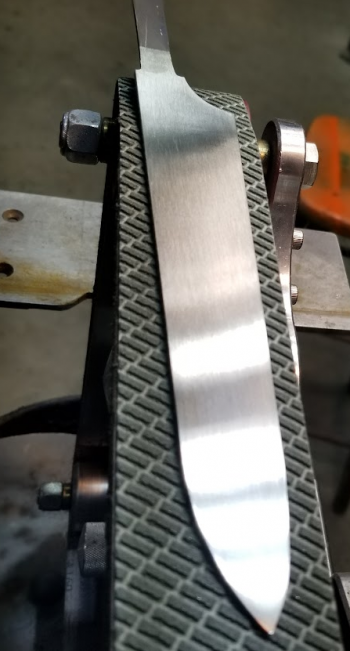
(Comments & critiques are welcome)