Ryan Minchew
Well-Known Member
Well after taking a haitus from everything but work I'm back. I hope everyone had a Merry Christmas and a Happy New Year.
I got the bolsters flat sanded. I wanted to get them just a hair thinner than the mop so that they could be sanded flat together and the mop would be more soft than the metal.
here you can see the bolster is still higher than the mop
closer
and it doesn't show it well here but the mop is actually taller than the bolster
Next I'll be taking the bolster from the 220 grit it's at to a 600 grit hand polish, then rough cutting the mop, glueing the mop up to the liners, drilling holes, then shaping the mop to the liners better. That's the plan for the weekend anyway. Take care
I got the bolsters flat sanded. I wanted to get them just a hair thinner than the mop so that they could be sanded flat together and the mop would be more soft than the metal.
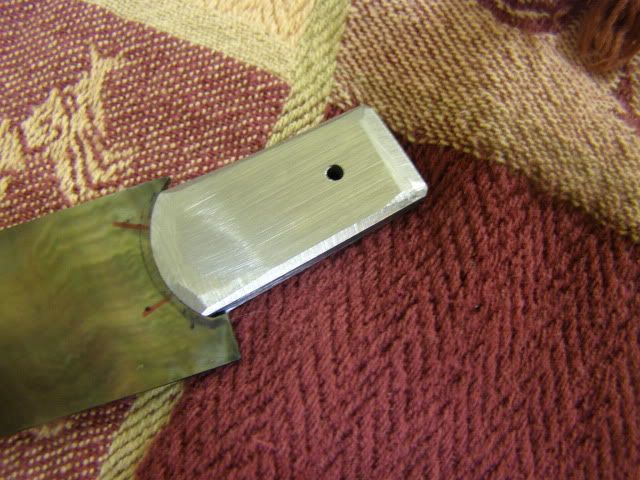
here you can see the bolster is still higher than the mop
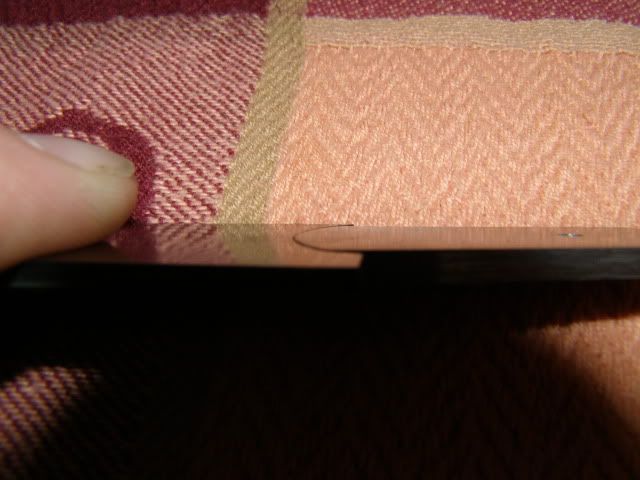
closer
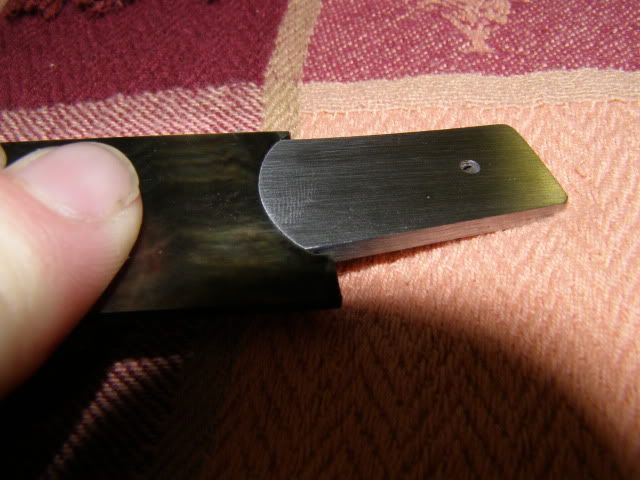
and it doesn't show it well here but the mop is actually taller than the bolster
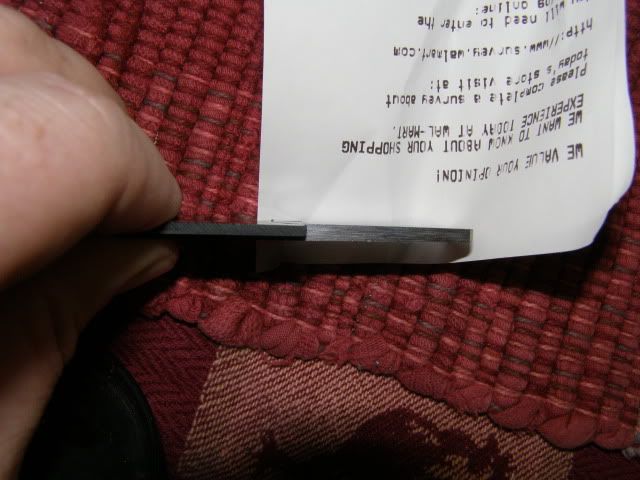
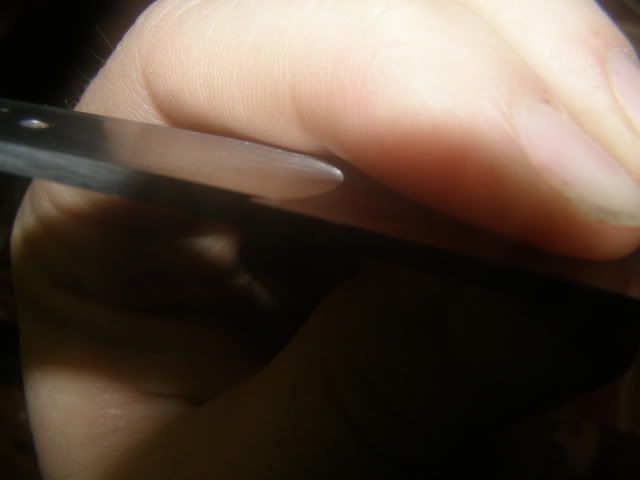
Next I'll be taking the bolster from the 220 grit it's at to a 600 grit hand polish, then rough cutting the mop, glueing the mop up to the liners, drilling holes, then shaping the mop to the liners better. That's the plan for the weekend anyway. Take care