McClellan Made Blades
Well-Known Member
Update from re-HT and using DT-48 quench oil....take a look at what I got!
Hey Guys,
With everyone's input and a lot of tenacity, meaning an abnormal amount of hand sanding, polishing, some cussing, whining and a little moaning AND cracking open a 5 gallon bucket of Maxim's DT-48, I was able to get a much better hamon, that is well off the edge, with some interesting activity that is really nice.
A couple of things I did differently,
1. When I applied the clay, I didn't do my normal 1/3rd's, it was more like 1/4th's, I basically kept the clay much higher, closer to the spine, and then added my little details by using a little more water mixed with clay than normal and drug the extra lines down toward the edge at an angle, or rather a curve...hard to explain, next time I think I will do a straight line at an angle to see what happens.
2. My target temp this time was 1450, I did a 5 minute soak time, I'm thinking from what I've learned from Don Hanson's many posts, is the a 7 to 8 minute soak time would be better and may help in keeping the hamon higher up on the blade.
3. And probably one of the most important changes, I quenched it in Maxim's
DT-48. I believe I got the best results from using it than I have with anything I've used to date. It came out harder than any blade I have quenched and no warping on a fairly thin blade (knock on wood!).
Now it's time to see some PICS!!
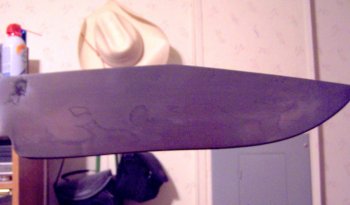
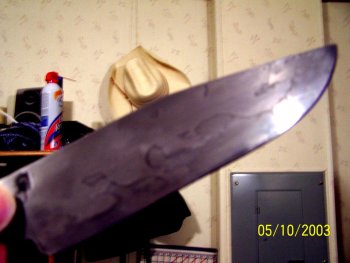
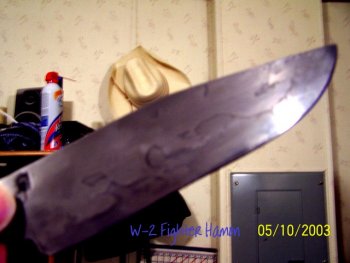
I did my best to make them a good size to be able to see the details, it may be pretty big, sorry the pics aren't the best but it's late!
Let me know what y'all think, both pro's and con's! If these pics aren't good enough, let me know and I'll set up my light tent tomorrow night and get some better shots!
Thanks for EVERYTHING!!! I couldn't have done it without everyone's help! Rex
Hey Guys,
With everyone's input and a lot of tenacity, meaning an abnormal amount of hand sanding, polishing, some cussing, whining and a little moaning AND cracking open a 5 gallon bucket of Maxim's DT-48, I was able to get a much better hamon, that is well off the edge, with some interesting activity that is really nice.
A couple of things I did differently,
1. When I applied the clay, I didn't do my normal 1/3rd's, it was more like 1/4th's, I basically kept the clay much higher, closer to the spine, and then added my little details by using a little more water mixed with clay than normal and drug the extra lines down toward the edge at an angle, or rather a curve...hard to explain, next time I think I will do a straight line at an angle to see what happens.
2. My target temp this time was 1450, I did a 5 minute soak time, I'm thinking from what I've learned from Don Hanson's many posts, is the a 7 to 8 minute soak time would be better and may help in keeping the hamon higher up on the blade.
3. And probably one of the most important changes, I quenched it in Maxim's
DT-48. I believe I got the best results from using it than I have with anything I've used to date. It came out harder than any blade I have quenched and no warping on a fairly thin blade (knock on wood!).
Now it's time to see some PICS!!
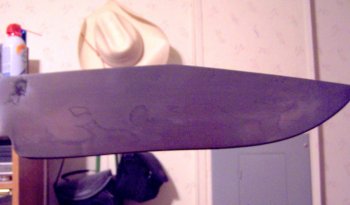
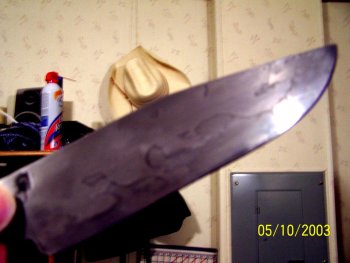
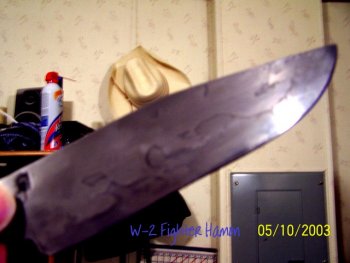
I did my best to make them a good size to be able to see the details, it may be pretty big, sorry the pics aren't the best but it's late!
Let me know what y'all think, both pro's and con's! If these pics aren't good enough, let me know and I'll set up my light tent tomorrow night and get some better shots!
Thanks for EVERYTHING!!! I couldn't have done it without everyone's help! Rex