Bruce Bump
Forum Owner-Moderator
The excess bolster material can be cleaned up on the belt grinder now or after its pinned permanately
Pop the bolsters off the frame and clean the glue off with a razor blade. If they dont just "pop off" use a propane torch and warm them up, they,ll come off for sure. Stack and pin them together and face them off on the flat disc as a pair. Be sure the disc table is set at 90 degrees.
Mark each one "out" so you cant reverse them and using a 2 degree tapered ream by hand remove metal from the "out" side of each. Taper them all the way to the other side not just a little around the top of the hole as the bolsters will be contoured later and the pin wouldnt be tapered enough to hold tight.
Cut a couple of 1/8" pins and sharpen on end to slip through the assembly. Grind off the pins on both ends so they stand proud about 3/16" and peen them down enough to close up the gaps.
From here I like to press them down with my forging press but a bigger hammer would work too.

Pop the bolsters off the frame and clean the glue off with a razor blade. If they dont just "pop off" use a propane torch and warm them up, they,ll come off for sure. Stack and pin them together and face them off on the flat disc as a pair. Be sure the disc table is set at 90 degrees.
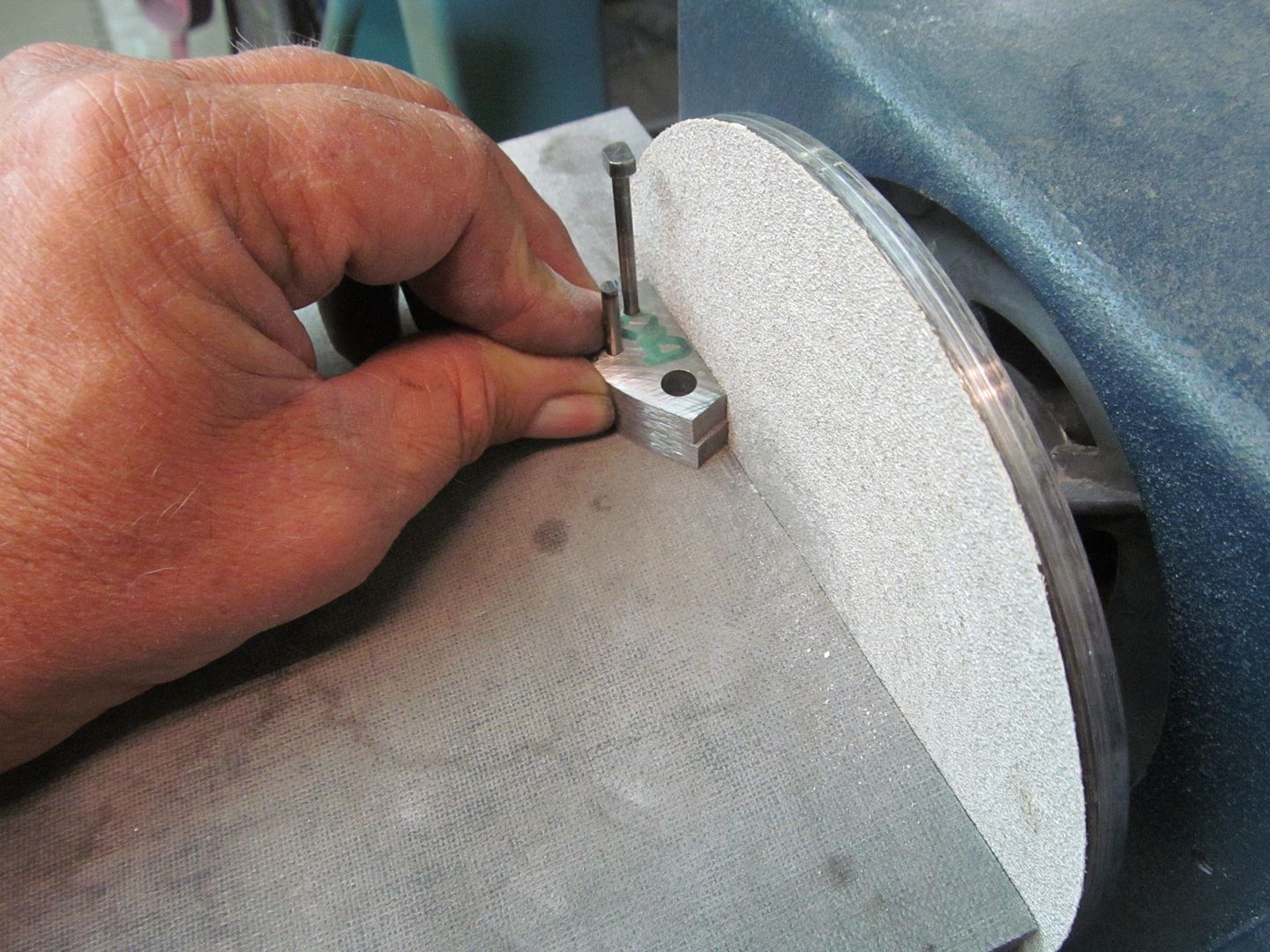
Mark each one "out" so you cant reverse them and using a 2 degree tapered ream by hand remove metal from the "out" side of each. Taper them all the way to the other side not just a little around the top of the hole as the bolsters will be contoured later and the pin wouldnt be tapered enough to hold tight.
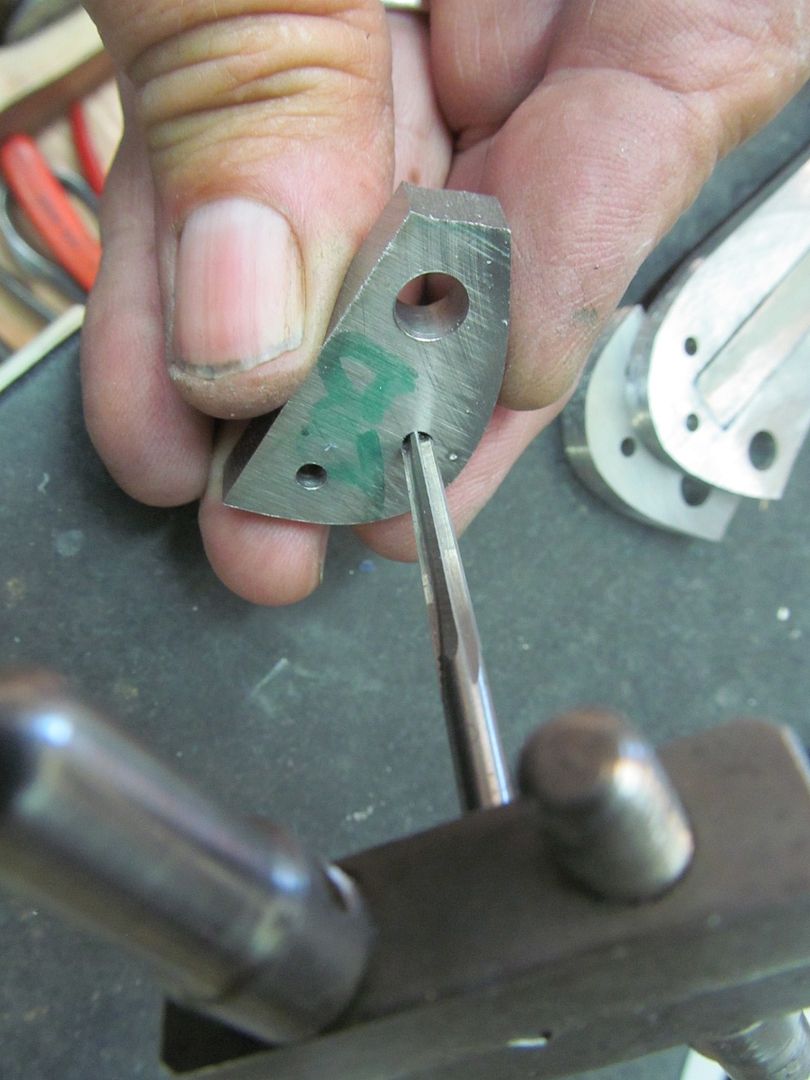
Cut a couple of 1/8" pins and sharpen on end to slip through the assembly. Grind off the pins on both ends so they stand proud about 3/16" and peen them down enough to close up the gaps.
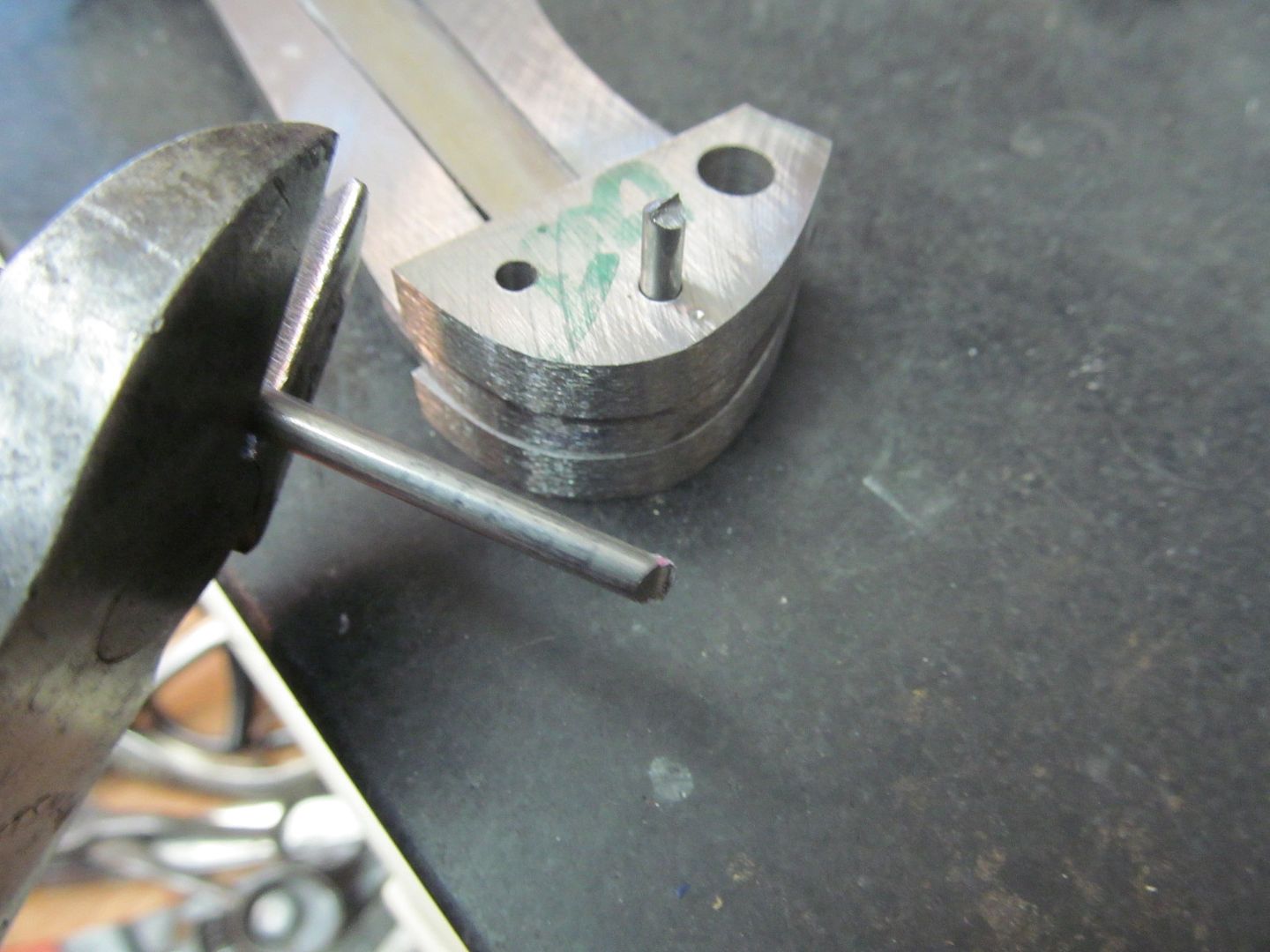
From here I like to press them down with my forging press but a bigger hammer would work too.
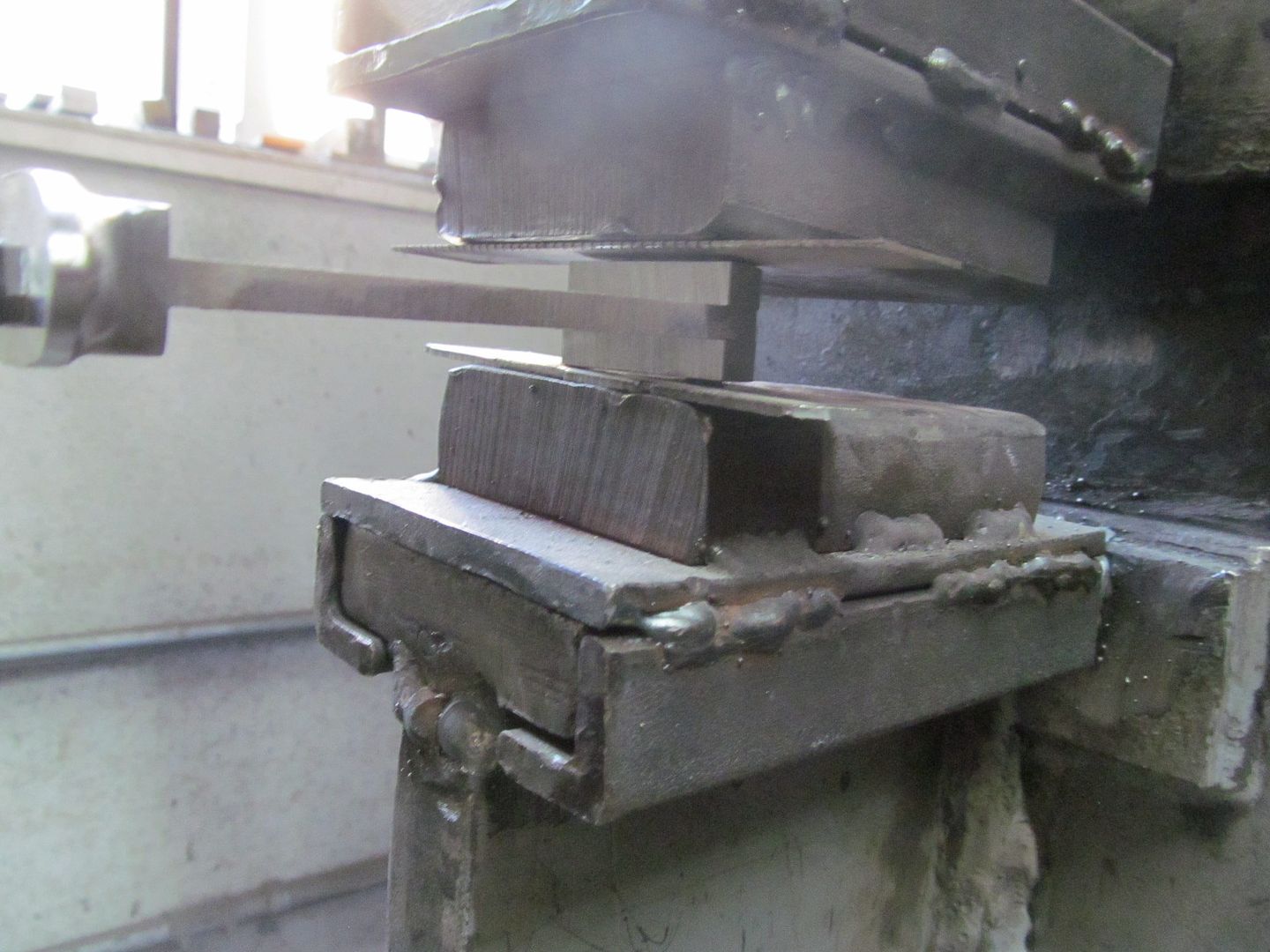
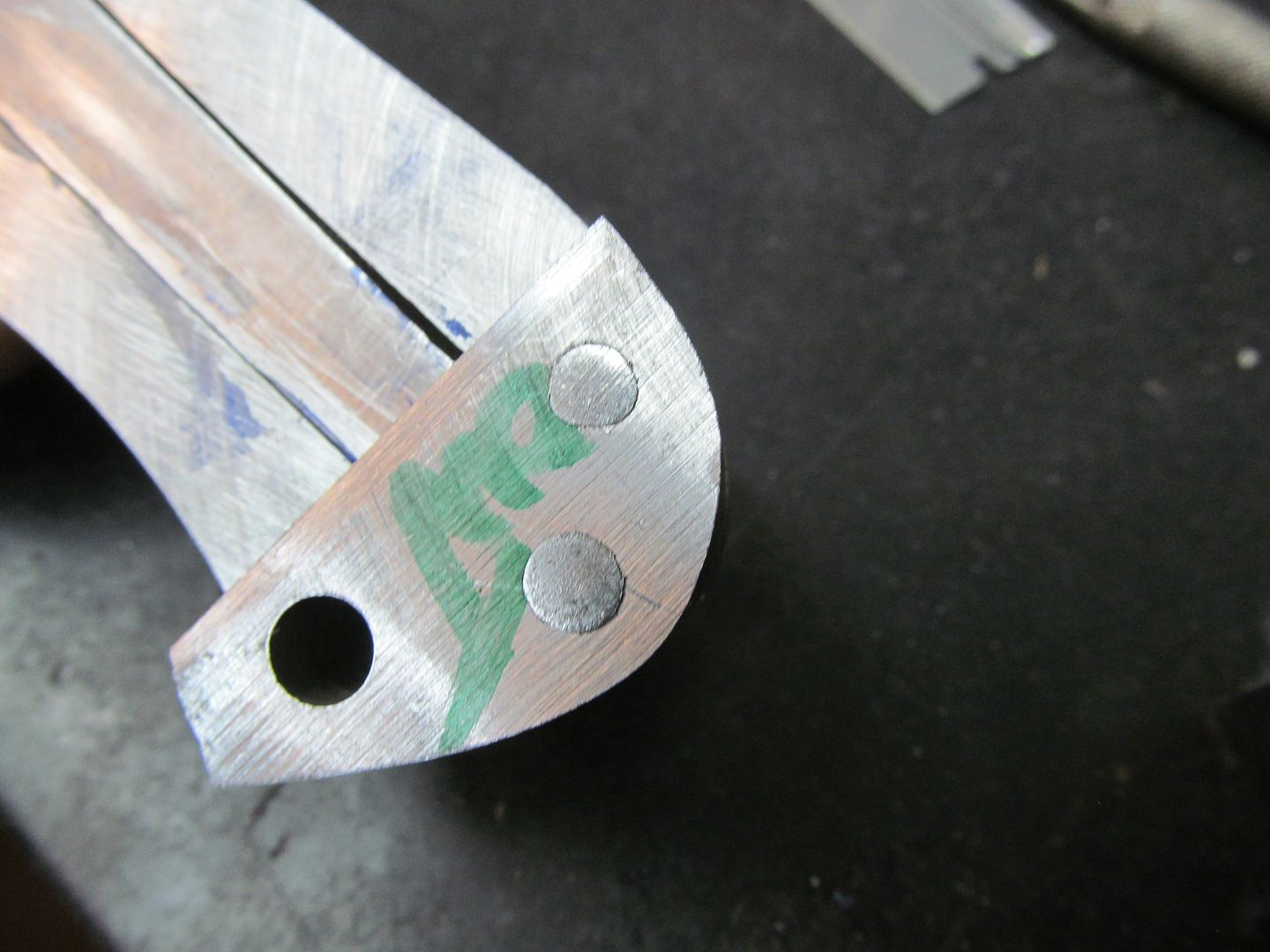
Last edited: