Ryan Minchew
Well-Known Member
Thanks for the thoughts on the spring guys, beats tapping it in with hammer.
Wanted to post a few more pictures mainly shaping. I screwed up the first set during shaping. I took too much off the front to where the lock showed in the half stop position.
Here's some with the new liners shaped and the blade is rough ground here. I ground it on a 14" wheel.
I'm using the parallel clamps to clamp to see what it looks like when closed. So far it's all lining up centered, fingers crossed it stays that way
I've got a little more on the other two to catch them up to this point so it maybe a couple days before I post some. In the closed position on this knife the spring sticks up a hair so I'll be showing how I'm going about correcting that problem. I worked on it some last night, hopefully I'll work on it a little more after work tonight.
Wanted to post a few more pictures mainly shaping. I screwed up the first set during shaping. I took too much off the front to where the lock showed in the half stop position.
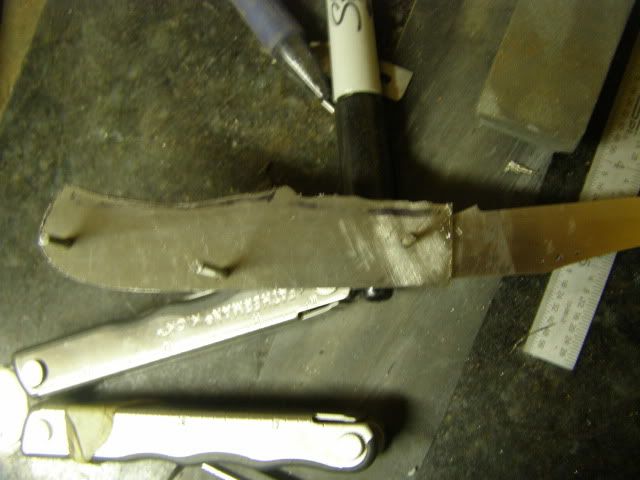
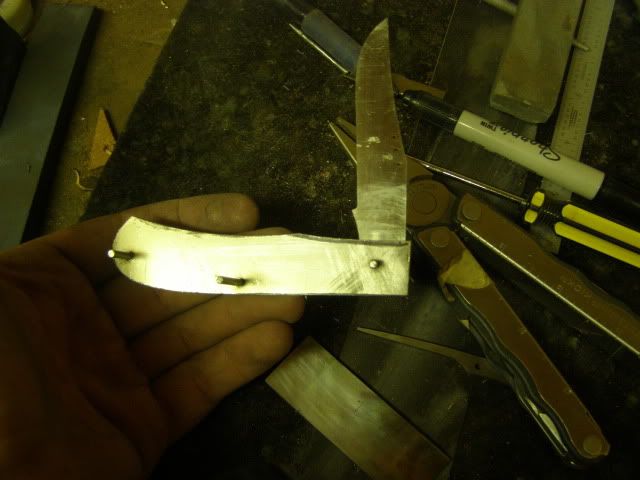
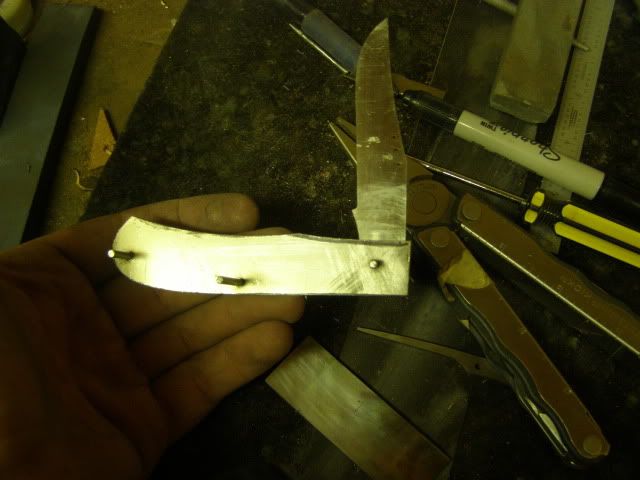
Here's some with the new liners shaped and the blade is rough ground here. I ground it on a 14" wheel.
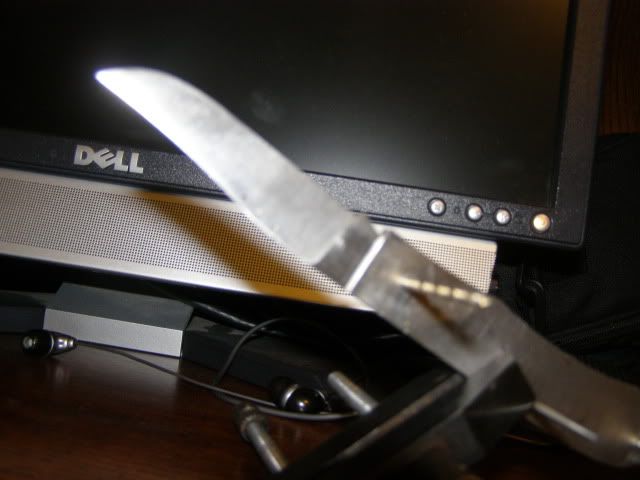
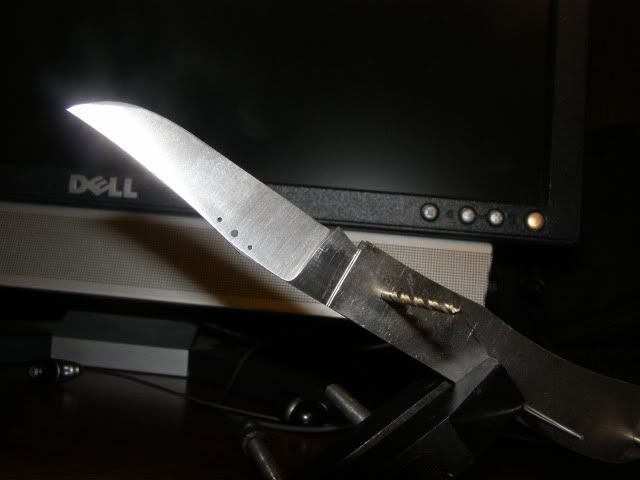
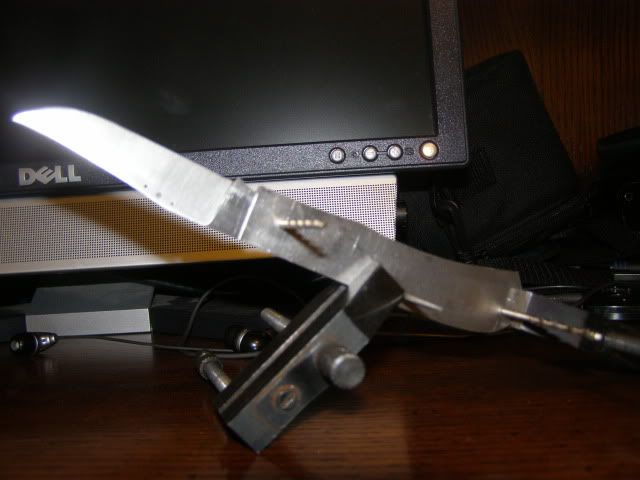
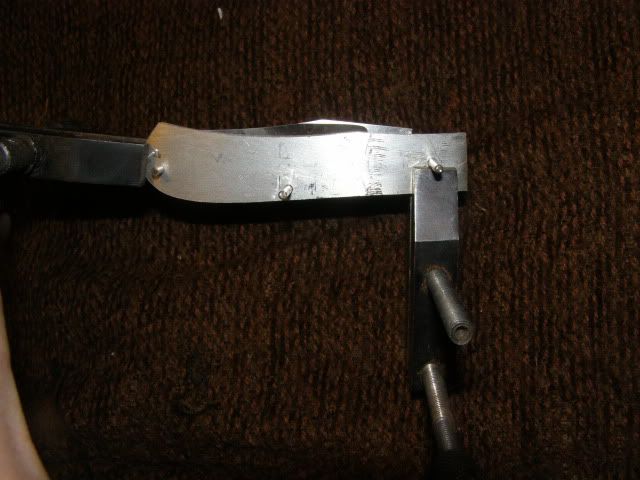
I'm using the parallel clamps to clamp to see what it looks like when closed. So far it's all lining up centered, fingers crossed it stays that way
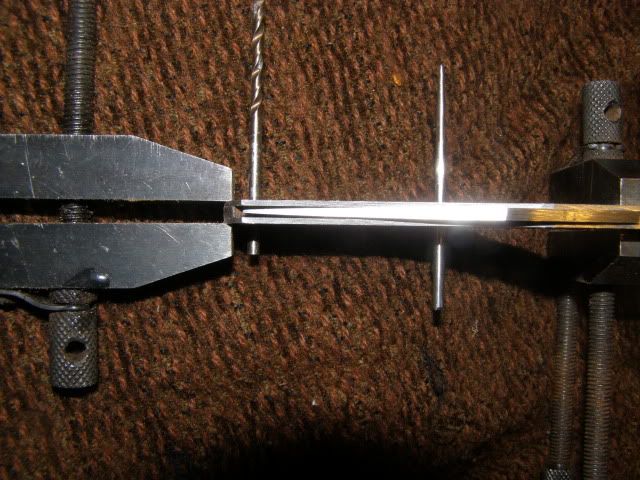
I've got a little more on the other two to catch them up to this point so it maybe a couple days before I post some. In the closed position on this knife the spring sticks up a hair so I'll be showing how I'm going about correcting that problem. I worked on it some last night, hopefully I'll work on it a little more after work tonight.