DanF
Well-Known Member
After many different recipes and etchant soak protocols, this is my best attempt. I still have a lot of work to do at the transition line where the two steels meet, but I think I'm getting there.
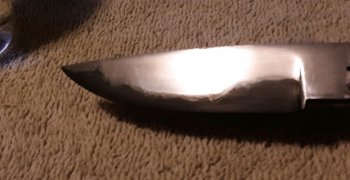
This is what I'm going for, but it still has a long way to go as every component will need much shaping and refining still.
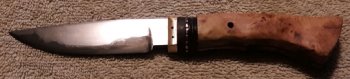
1084 sandwiched between 15n20. I think I will reverse them next time.
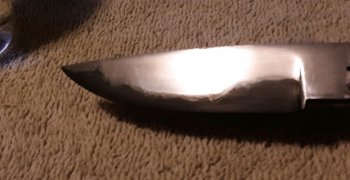
This is what I'm going for, but it still has a long way to go as every component will need much shaping and refining still.
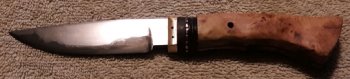
1084 sandwiched between 15n20. I think I will reverse them next time.
Last edited: