N.N
Well-Known Member
I ordered a used benzomatic ts4000 on ebay, $15. Another member graciously donated 3 firebricks to the cause. Another $15 in brackets and such and my forge build is on it's way.
I used a 2" pvc pipe and sandpaper to create the hole and drilled out a hole. I drilled an angled hole for the torch head at the top of the inner brick tube to try and make the heat "Swirl" as I've seen on videos and such. What is not pictured below, and the next step to complete it is a metal frame that I'm constructing to hold the thing.
I got it fired up for a first test last night, wanted to do it at night so I could really see the colors. It seems to be a decent start, but it doesn't seem to be getting hot enough. I stuck a 1/4" thick piece of mild steel in this thing and after about 10 minutes of sitting in it, it never got to non magnetic. It was starting to turn red. So am I just not waiting long enough? Is 1/4" too thick? I've read where these things should be getting really hot, really fast, like a couple of minutes. I angled the hole and the torch head at the top of the inner brick tube to try and make the heat "Swirl" as I've seen on videos and such. But I've seen these things where the fire is roaring out of the holes. I never saw that roar. It was hot, but I could hold my hand 6 inches above the holes where the fire came out with no problem.
So what am I doing wrong? Is it the torch or something else? The pictures make the fire look a lot brighter that it really did look. And my old backyard forge gets way hotter, much faster.
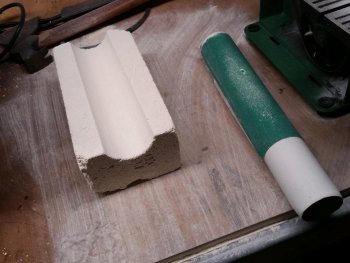
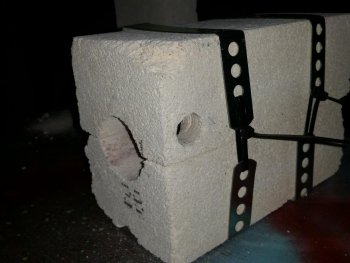
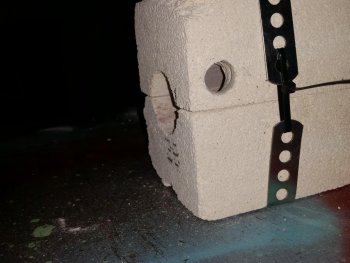
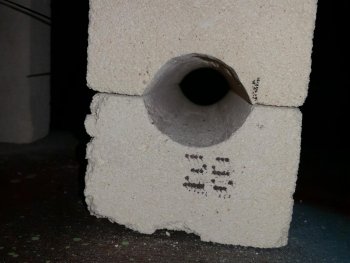
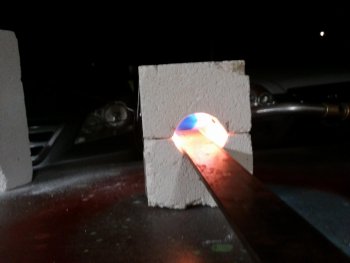
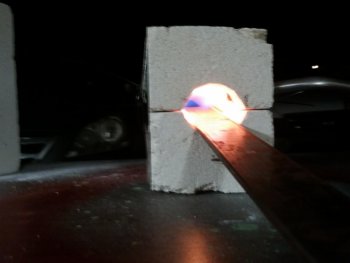
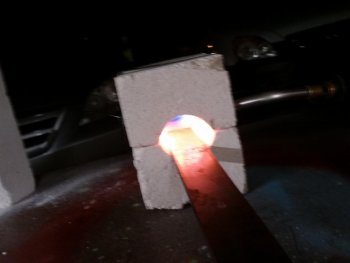
I used a 2" pvc pipe and sandpaper to create the hole and drilled out a hole. I drilled an angled hole for the torch head at the top of the inner brick tube to try and make the heat "Swirl" as I've seen on videos and such. What is not pictured below, and the next step to complete it is a metal frame that I'm constructing to hold the thing.
I got it fired up for a first test last night, wanted to do it at night so I could really see the colors. It seems to be a decent start, but it doesn't seem to be getting hot enough. I stuck a 1/4" thick piece of mild steel in this thing and after about 10 minutes of sitting in it, it never got to non magnetic. It was starting to turn red. So am I just not waiting long enough? Is 1/4" too thick? I've read where these things should be getting really hot, really fast, like a couple of minutes. I angled the hole and the torch head at the top of the inner brick tube to try and make the heat "Swirl" as I've seen on videos and such. But I've seen these things where the fire is roaring out of the holes. I never saw that roar. It was hot, but I could hold my hand 6 inches above the holes where the fire came out with no problem.
So what am I doing wrong? Is it the torch or something else? The pictures make the fire look a lot brighter that it really did look. And my old backyard forge gets way hotter, much faster.
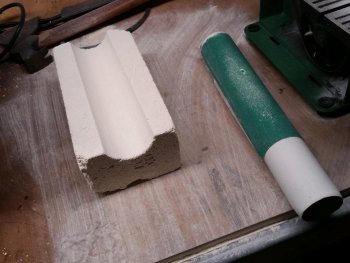
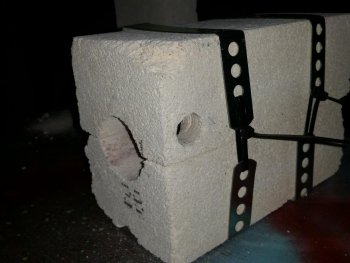
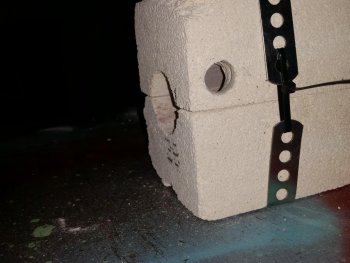
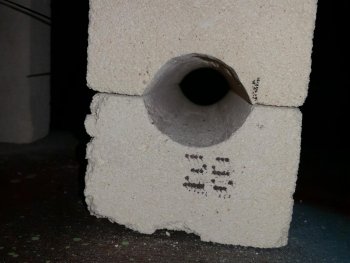
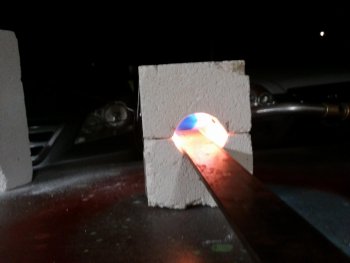
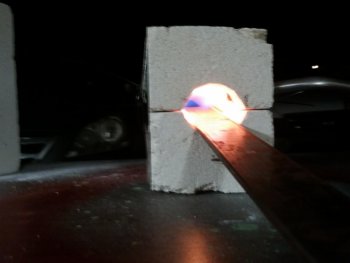
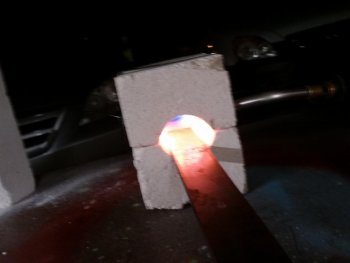
Last edited: