Cameron Wilcox
Well-Known Member
I sent off a batch of knives for HT but forgot that the drill bit I had been using gave up the ghost with 2 of 3 holes drilled on one knife. So I bought a carbide bit from Tracy but when I try to drill it (high speed w/ lots of cutting lube) my old drill press just begins to vibrate and the work table just slides down. The drill press is an old one that was given to me by my grandfather and he had gotten it from his father-in-law so I'm sure that is the issue but now I am faced with another problem, is two front pins enough? The handle is 4" and the holes are are 5/8" and 2 1/4" from the Ricasso.
This is how it looks
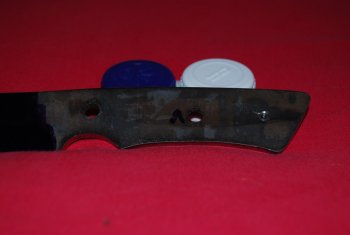
It is dykem on the blade just pulled it from grinding to take this
This is how it looks
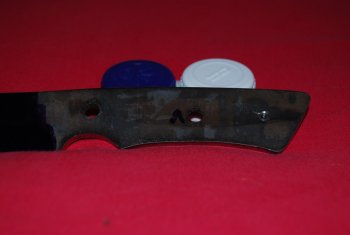
It is dykem on the blade just pulled it from grinding to take this
Last edited: