farmrbrnboy
Active Member
When forging out the bevel/belly of bigger blades, WIP around 11", the distal end keeps bending up. I tried forging the blade with the opposite bend, but the distal end keeps bending up and I had to forge it back to straight after each heat with the belly/bevel and then address and twisting of the edge. Should I not have even worried about forging the blade with the opposite bend initially and just straighten as I go? My order of forging goes like this, hot cut bar to length, forge rough handle, forge down top of spine towards tip, draw both ends out, forge edge working from spine down to the edge, one side, flip and then the other side, work my way down to the tip, edge thicker than a nickle, dress up the edge to around dime-nickle thickness. BTW, I am using 1/4" x 1 1/2" 5160
Here is my first attempt at a zombie cutter, my 3rd blade forged, full convex grind. It's not cleaned up after HT, waiting on new belts
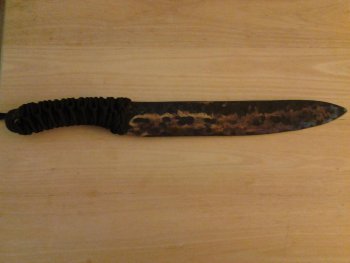
Here is my first attempt at a zombie cutter, my 3rd blade forged, full convex grind. It's not cleaned up after HT, waiting on new belts
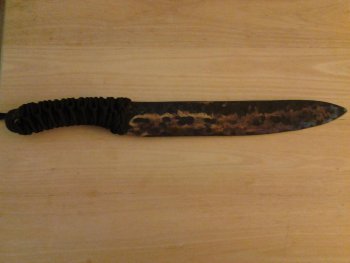