I tried putting a hamon on knife for the first time and ran into a snaffu while tempering. After tempering the blade cracked at the the choil. I heat treated 2 other 1084 blades at the same time, and had no issues. The only difference was the attempt at a hamon on this one, but it doesn't look the crack is any where near the hamon. Attached are pics showing after hardening and after tempering. The blade is 1/8" thick 1084 created using stock removal. Here's the process i went with:
Blade was shaped and ground to 220 grit. Washed the blade with dish soap and hot water. Dried the blade. Applied refractory cement. Let dry (ended up being about 2 days). Heat treated in a small forge. Brought up to nonmagnetic. Quenched in 130-140 degree canola oil. Let cool to room temperature. Scraped of clay, and lightly sanded to remove scale. Rinsed off scale. (1st pic was taken) Placed in oven at 375 degrees for 1 1/2hrs. Removed and cooled to room temperature. Placed back in oven at 375 for 1 1/2 hours. (2nd pic was taken)
Any advice as to why this would have happened or improvements in my process would be great.
Thank you,
Aaron
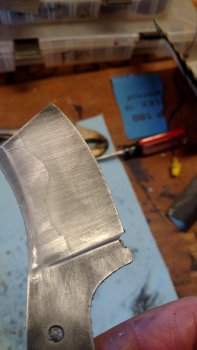
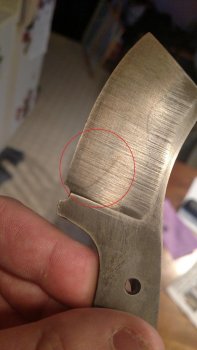
Blade was shaped and ground to 220 grit. Washed the blade with dish soap and hot water. Dried the blade. Applied refractory cement. Let dry (ended up being about 2 days). Heat treated in a small forge. Brought up to nonmagnetic. Quenched in 130-140 degree canola oil. Let cool to room temperature. Scraped of clay, and lightly sanded to remove scale. Rinsed off scale. (1st pic was taken) Placed in oven at 375 degrees for 1 1/2hrs. Removed and cooled to room temperature. Placed back in oven at 375 for 1 1/2 hours. (2nd pic was taken)
Any advice as to why this would have happened or improvements in my process would be great.
Thank you,
Aaron
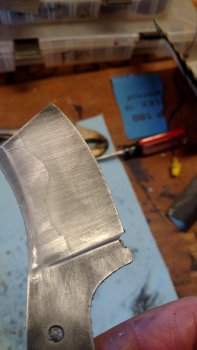
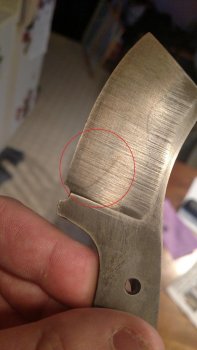