Stormcrow
Well-Known Member
This is something that has been in development for a very long time and has finally come to fruition: a line of tactical tomahawks. I've hinted at them recently, but did not want to reveal what I was working on until they were ready for sale, and would not put them up for sale until I could trust a soldier's life on my work. That meant a lot of prototyping and thorough testing, part of which resulted in this picture I've posted a few times:
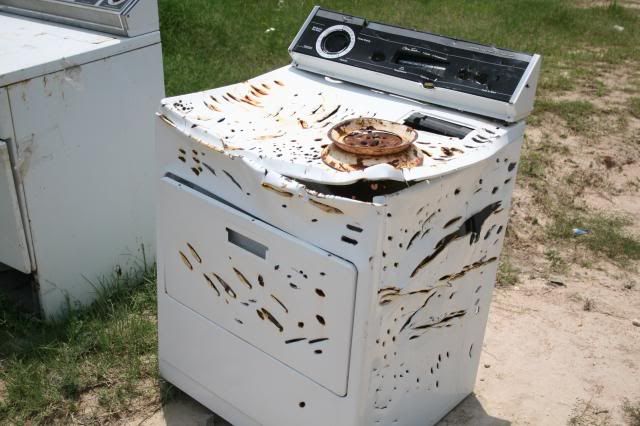
On top of the clothes dryer is the end of a propane tank that has been forcibly converted into a sieve by the prototype spike 'hawks. The second, untouched dryer in the background is destined to get mangled by the finalized tomahawks for a Youtube video.
For a long time I planned on building them with a traditional construction using a forged head with an eye and a separate handle. I used nylon 6/6 for the handle, which felt very much like hickory as far as shock transfer while chopping. I was mostly happy with the results, but still had some questions in my head about them. One such question was the handle, while plenty stiff enough to transfer power when chopping, would flex too much when prying. Since breaching is a major usage of a modern military tomahawk, it concerned me.
Then a Navy SEAL, who has become my best customer, requested a full tang tomahawk. Logistically, it makes more sense to build something like that in a batch than individually, and it would solve the questions I had. It's all a matter of balancing what the end user needs, and military end users have a greater need of being able to use their tomahawks as a multitool or wrecking bar that they can also fight with if the need arises.
So I shifted direction on the entire project and went the stock removal route, something very different from my usual approach of forging. I drew sketches, lined up material suppliers, got CAD files built, and found a local waterjetter. After the prototyping phase and a few minor tweaks in angles that had substantial increases in utility, I got my first batch waterjet cut.
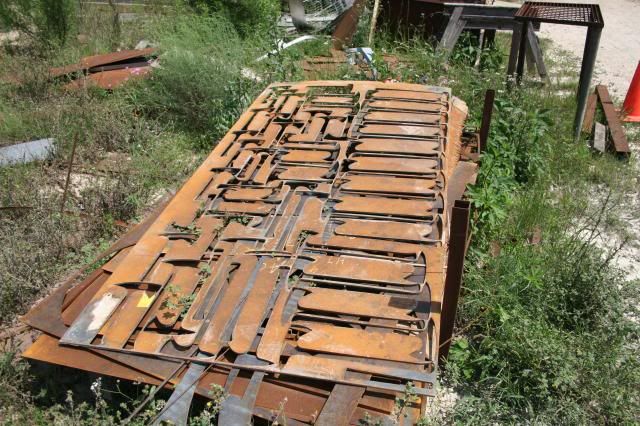
The steel is 1/4" thick 4140, the same alloy I have built my own power hammer dies from; very tough stuff. There are three different back ends available: hammer poll, combat spike, and pry spike. Each one is available in either 12" overall length or 18" overall length, and with or without sharpened inner beards. The handle slabs are 1/4" thick canvas Micarta with stainless steel flared tube rivets. The steel is coated in Durabake in one of three colors with matching Micarta colors: black, desert, and olive drab.
Here are blanks of one of each design prior to normalizing or grinding:
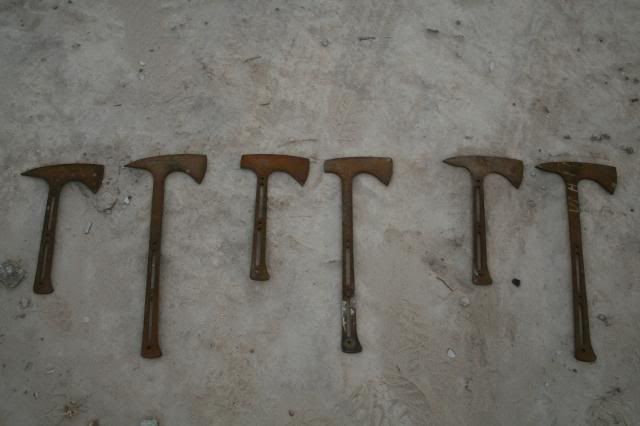
Pry spikes:
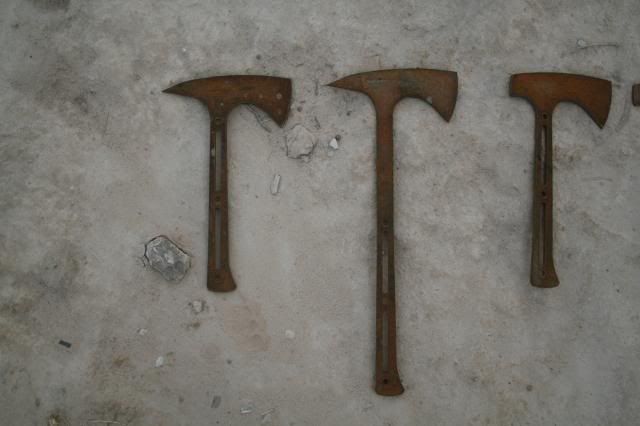
Hammer polls:
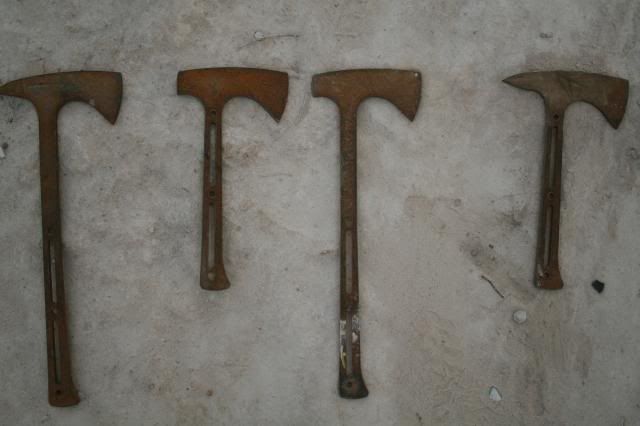
Combat spikes:
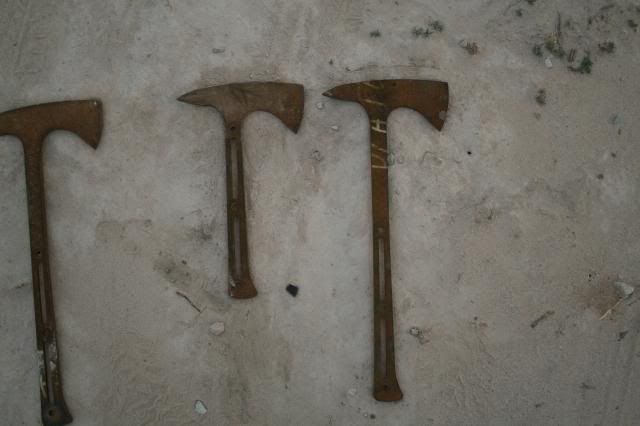
Stacks of blanks in the background and a blank cooling from normalizing in the foreground:
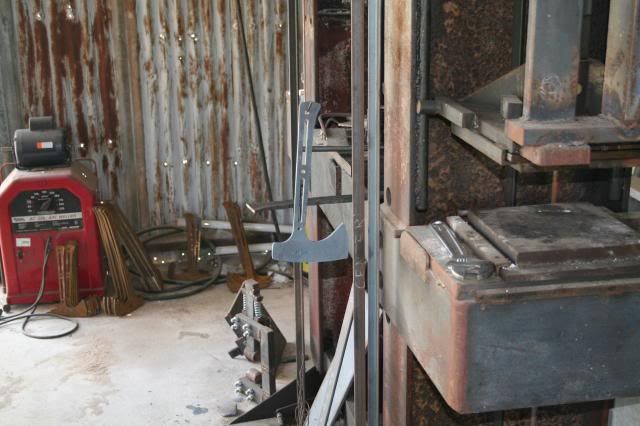
I really wanted to be able to debut the 'hawks at the Blade Show, and things came together just in time to do so (though the rivet tubing I ordered in plenty of time only got there the day before I drove to Atlanta! ). I grabbed out one blank of each design to get ready for the show.
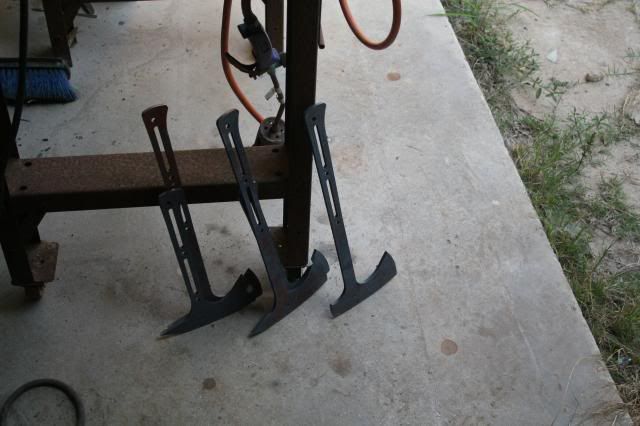
Then I got to grinding.

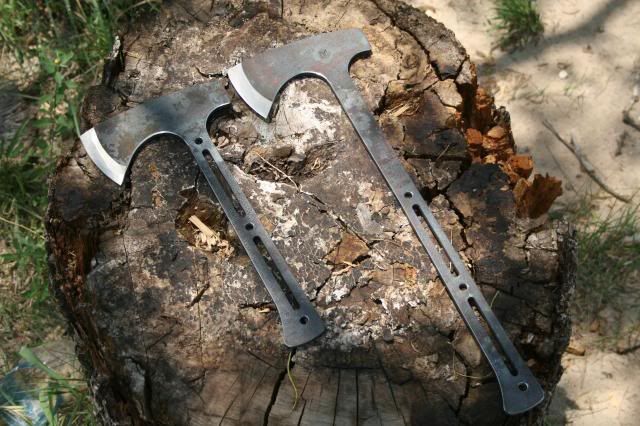
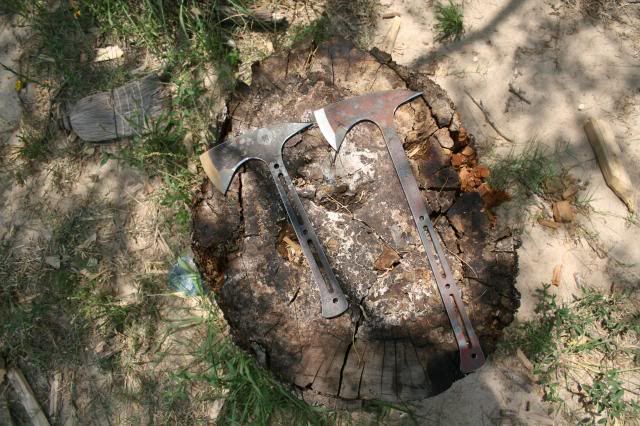
And heat treated them.
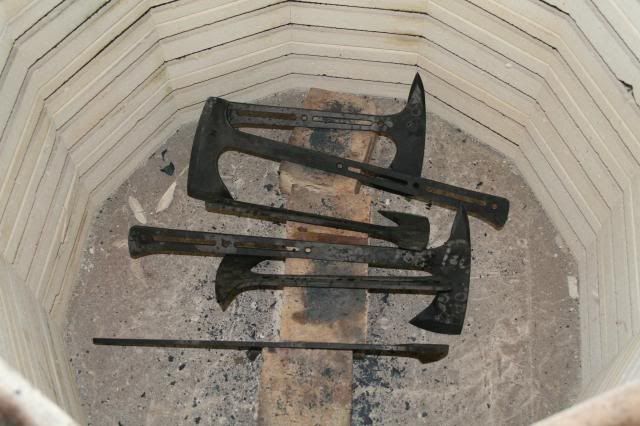
Then Durabaked, installed handles, and sharpened.
Hammer polls, unsharpened beards:
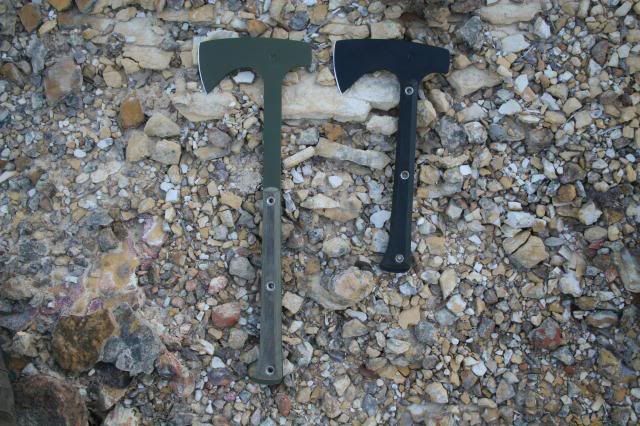
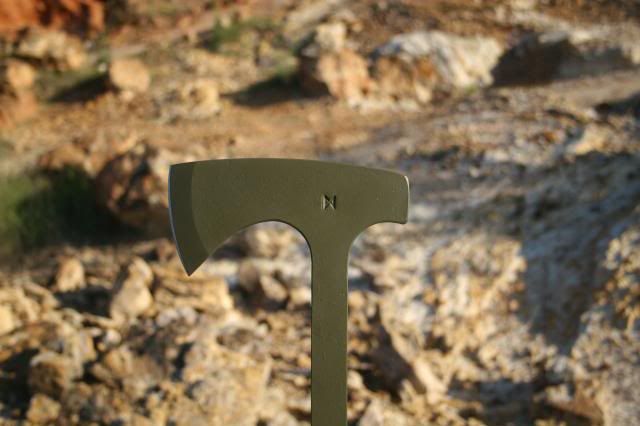
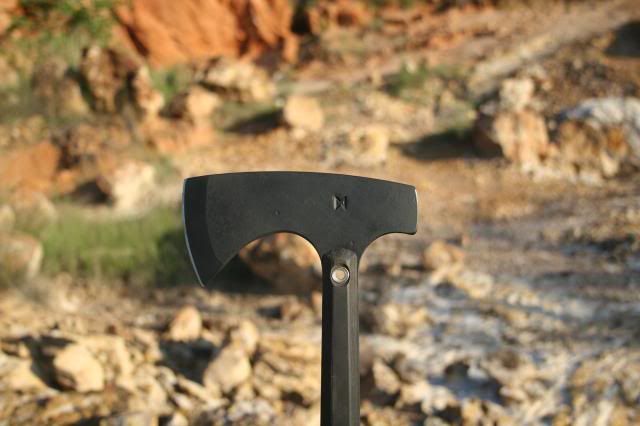
Combat spike, sharpened beard. The long one is black and is with a Kydex sheath maker.
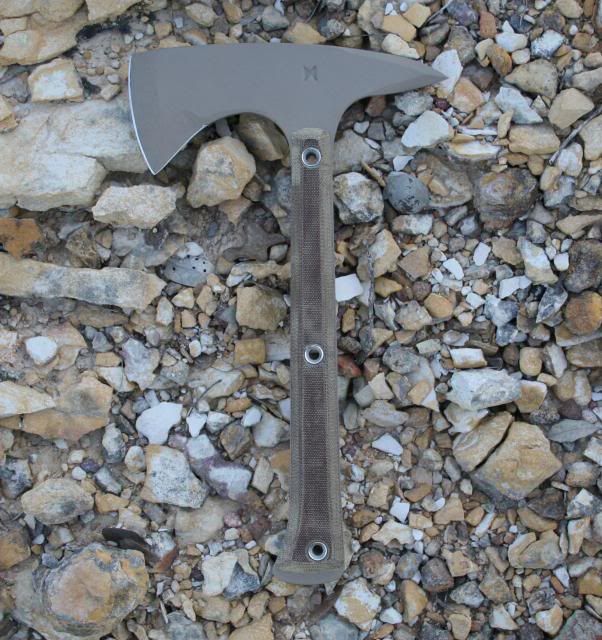
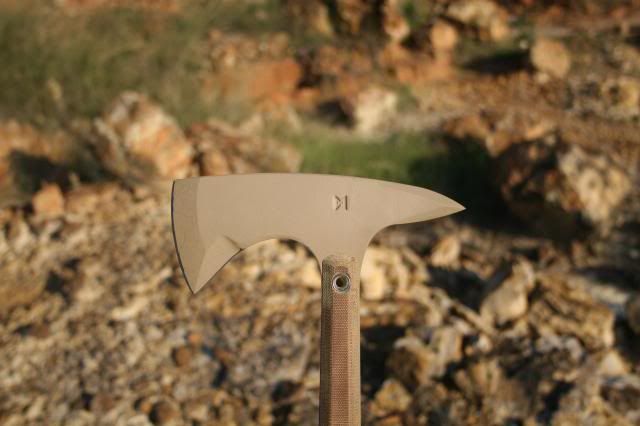
The combat spike is designed to penetrate well and then withdraw quickly for any needed follow-up shots. It excels at that, and the spike punches through the propane tank end like butter.
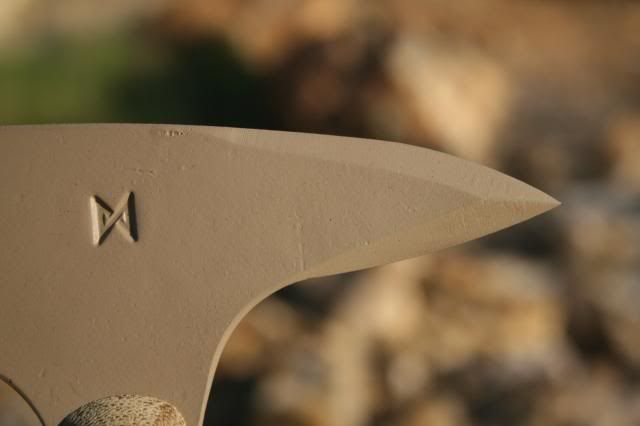
Pry spike, sharpened beard.

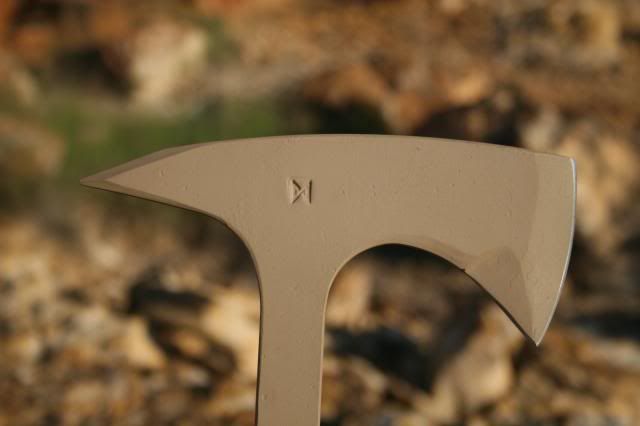
The pry spike is narrow enough to fit easily into a door jamb, while stout enough that it also penetrates the propane tank end without taking damage. Once the spike is nicely seated, the rounded top acts like a roller head pry bar, providing plenty of leverage.
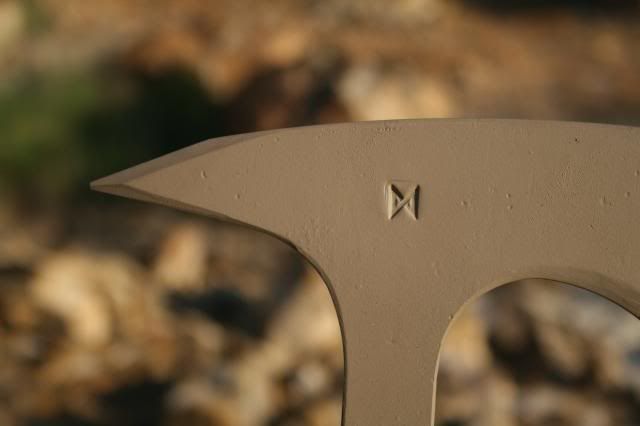
The short one (olive drab) sold at the Blade Show, and this was the only picture I managed to get.
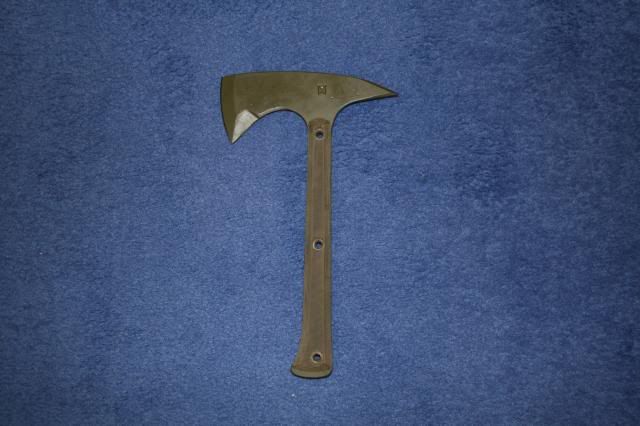
The handles have exposed pommels, allowing for some hammering ability with all designs and an extra striking area for CQB.
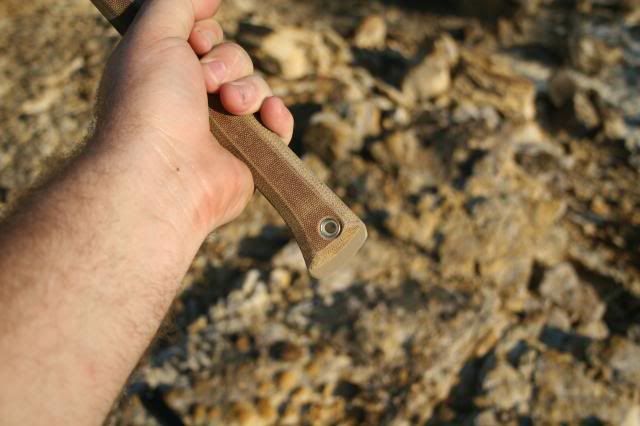
One advantage of shifting over to waterjetting is that I can build trainers fairly easily. These are cut from 3/4" ABS plastic and are the same pattern as the hammer polls, but with the corners rounded for safety. They are the same thickness as the handles of the real tomahawks and are beveled all over the same as the handles.
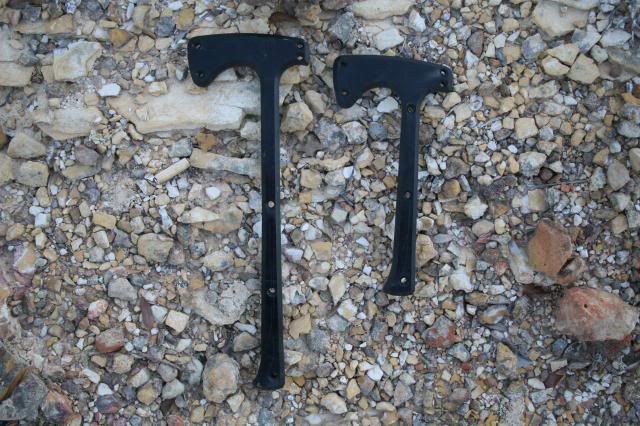
The extra holes allow you to slip a piece of foam pipe insulation or pool noodle over the ends and anchor them so you don't damage your sparring partner as much. The hammer polls are a bit shorter than the spikes, but are still long enough to practice hooking and deflecting limbs. The holes in the trainer handles allow practice with a lanyard.
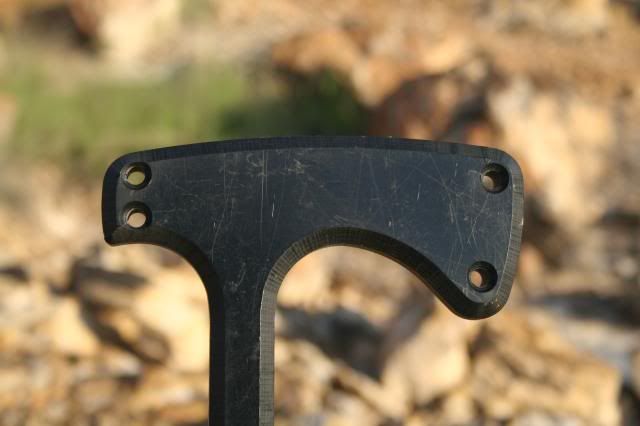
Sheaths are forthcoming, but should be Kydex, bottom eject, jump-ready, ambidextrous, MOLLE compatible, with multiple carry options.
These have been a long time coming, and I'm quite pleased to be able to finally have them on the table, ready to serve.
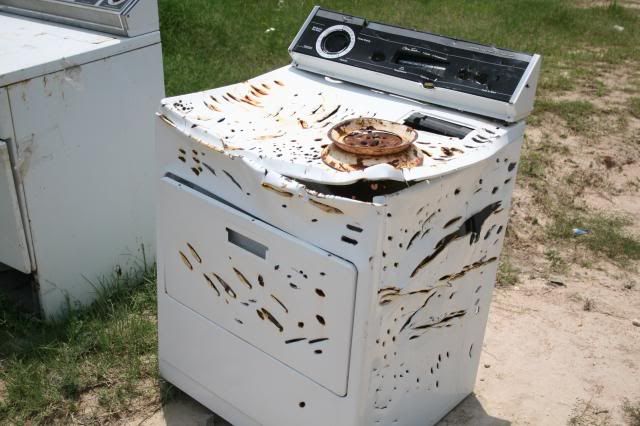
On top of the clothes dryer is the end of a propane tank that has been forcibly converted into a sieve by the prototype spike 'hawks. The second, untouched dryer in the background is destined to get mangled by the finalized tomahawks for a Youtube video.
For a long time I planned on building them with a traditional construction using a forged head with an eye and a separate handle. I used nylon 6/6 for the handle, which felt very much like hickory as far as shock transfer while chopping. I was mostly happy with the results, but still had some questions in my head about them. One such question was the handle, while plenty stiff enough to transfer power when chopping, would flex too much when prying. Since breaching is a major usage of a modern military tomahawk, it concerned me.
Then a Navy SEAL, who has become my best customer, requested a full tang tomahawk. Logistically, it makes more sense to build something like that in a batch than individually, and it would solve the questions I had. It's all a matter of balancing what the end user needs, and military end users have a greater need of being able to use their tomahawks as a multitool or wrecking bar that they can also fight with if the need arises.
So I shifted direction on the entire project and went the stock removal route, something very different from my usual approach of forging. I drew sketches, lined up material suppliers, got CAD files built, and found a local waterjetter. After the prototyping phase and a few minor tweaks in angles that had substantial increases in utility, I got my first batch waterjet cut.
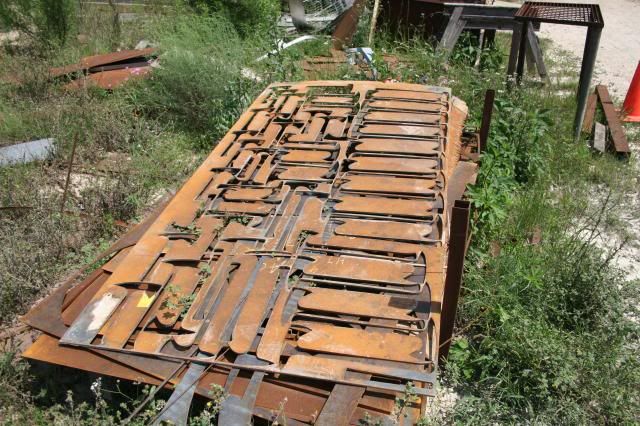
The steel is 1/4" thick 4140, the same alloy I have built my own power hammer dies from; very tough stuff. There are three different back ends available: hammer poll, combat spike, and pry spike. Each one is available in either 12" overall length or 18" overall length, and with or without sharpened inner beards. The handle slabs are 1/4" thick canvas Micarta with stainless steel flared tube rivets. The steel is coated in Durabake in one of three colors with matching Micarta colors: black, desert, and olive drab.
Here are blanks of one of each design prior to normalizing or grinding:
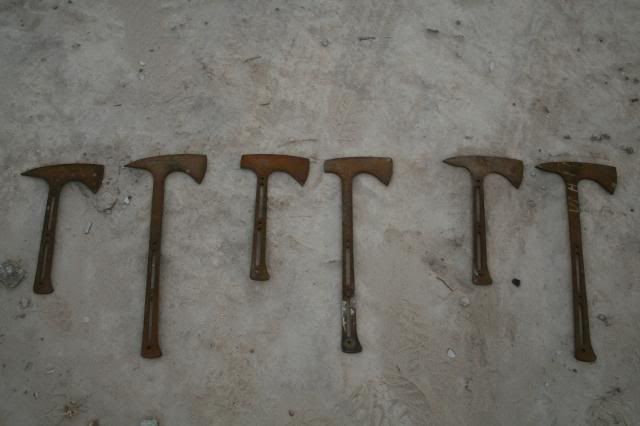
Pry spikes:
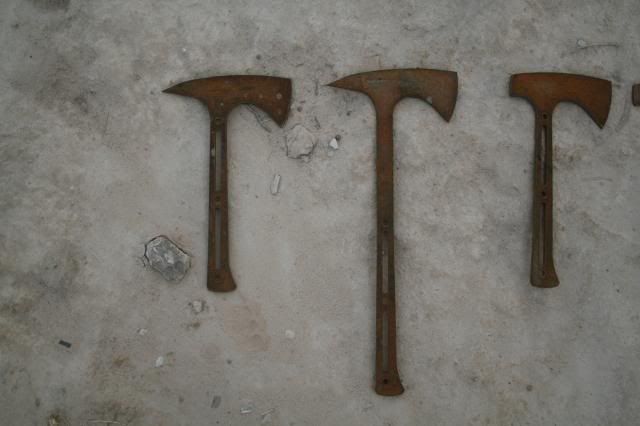
Hammer polls:
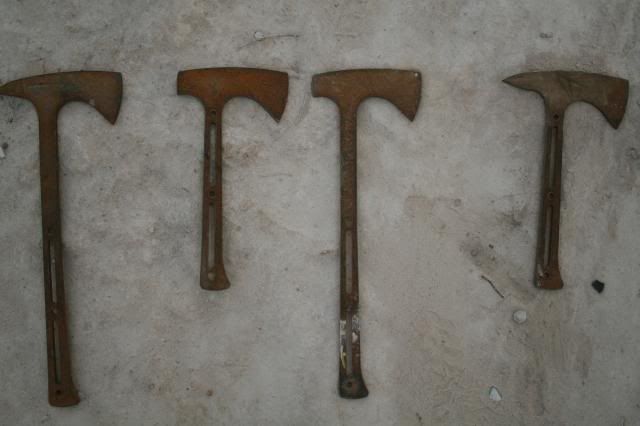
Combat spikes:
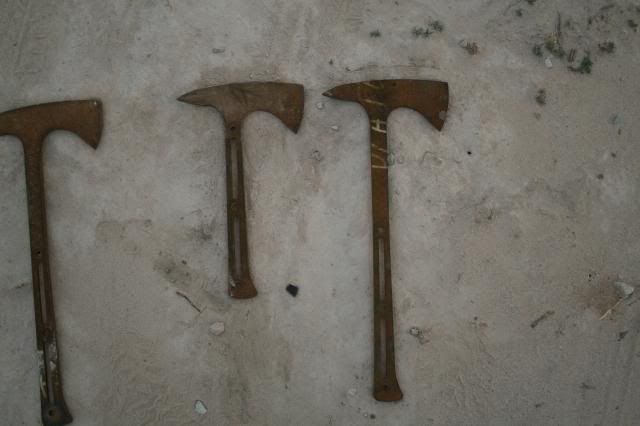
Stacks of blanks in the background and a blank cooling from normalizing in the foreground:
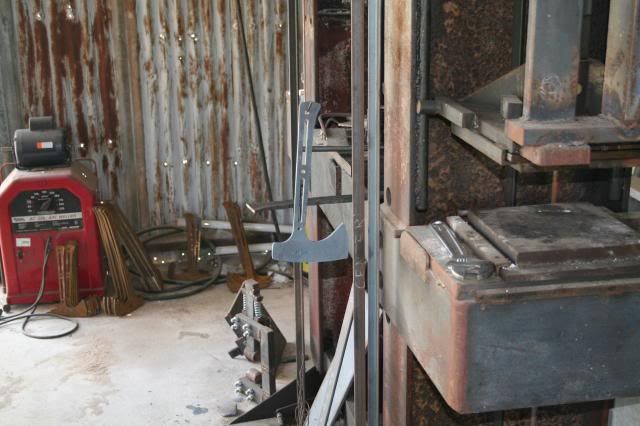
I really wanted to be able to debut the 'hawks at the Blade Show, and things came together just in time to do so (though the rivet tubing I ordered in plenty of time only got there the day before I drove to Atlanta! ). I grabbed out one blank of each design to get ready for the show.
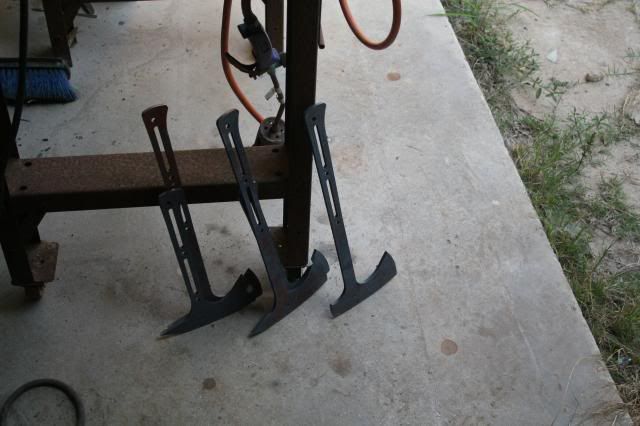
Then I got to grinding.

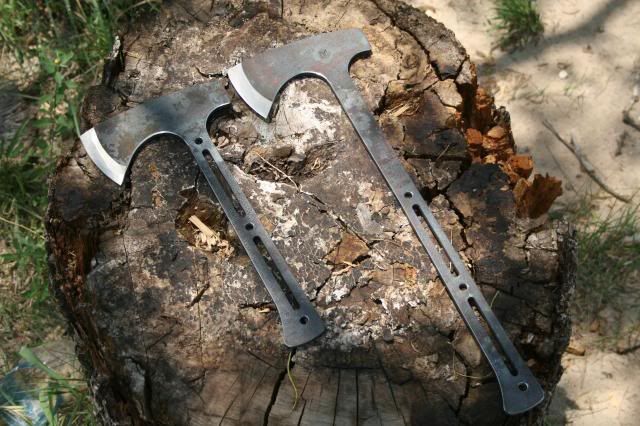
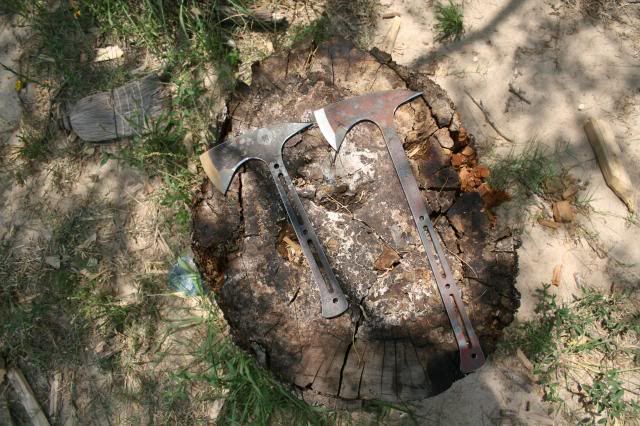
And heat treated them.
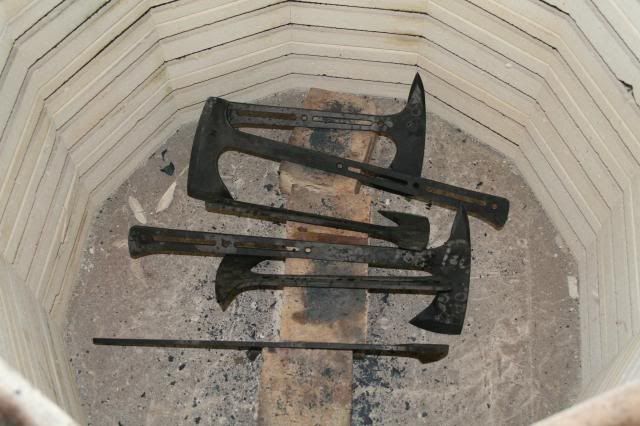
Then Durabaked, installed handles, and sharpened.
Hammer polls, unsharpened beards:
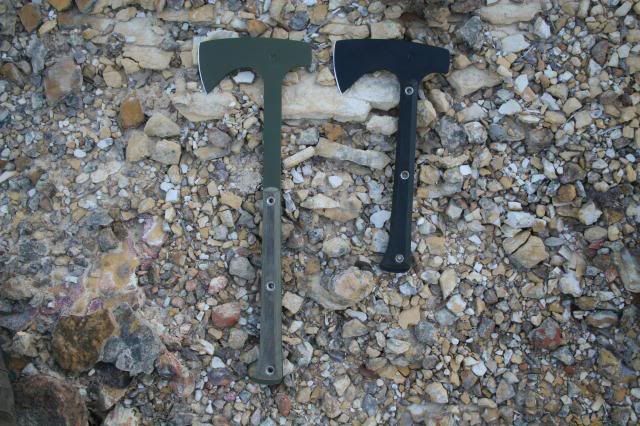
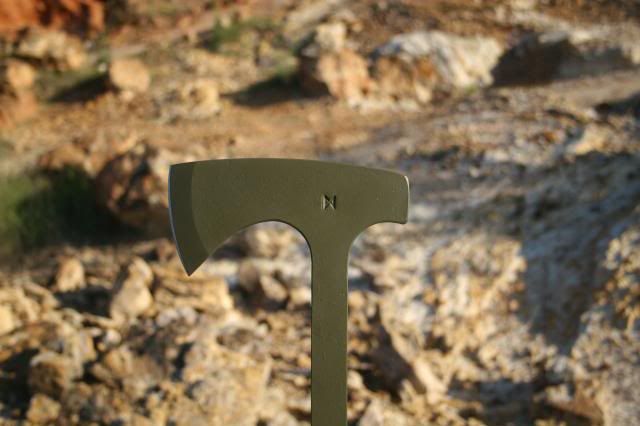
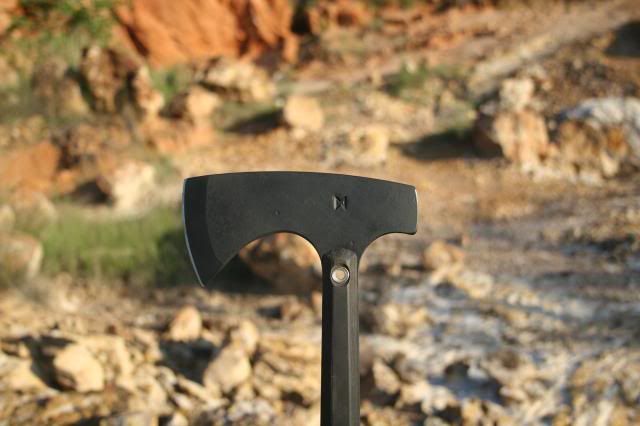
Combat spike, sharpened beard. The long one is black and is with a Kydex sheath maker.
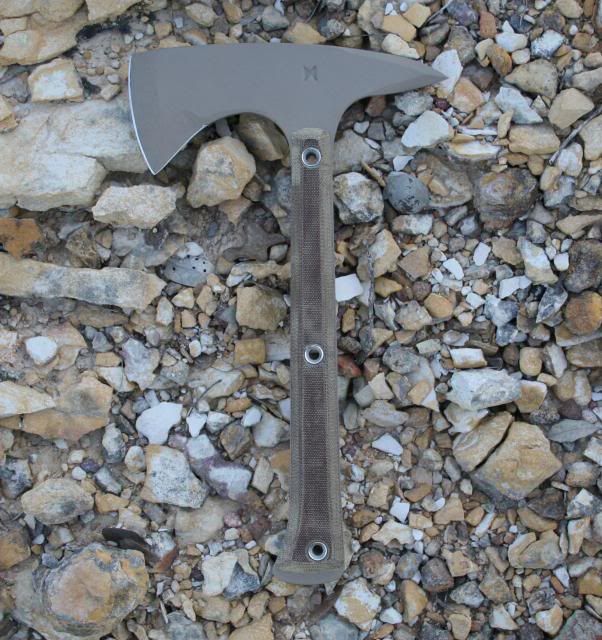
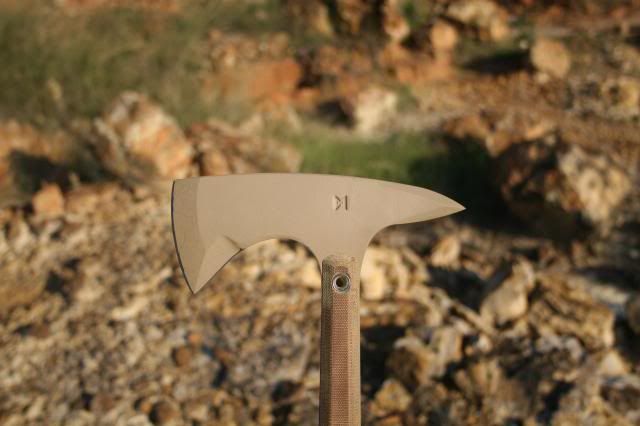
The combat spike is designed to penetrate well and then withdraw quickly for any needed follow-up shots. It excels at that, and the spike punches through the propane tank end like butter.
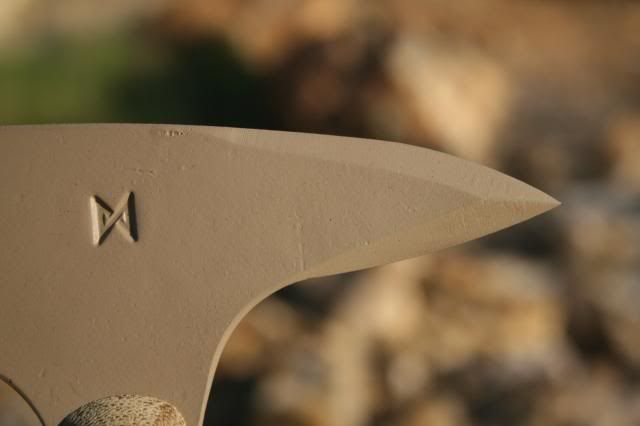
Pry spike, sharpened beard.

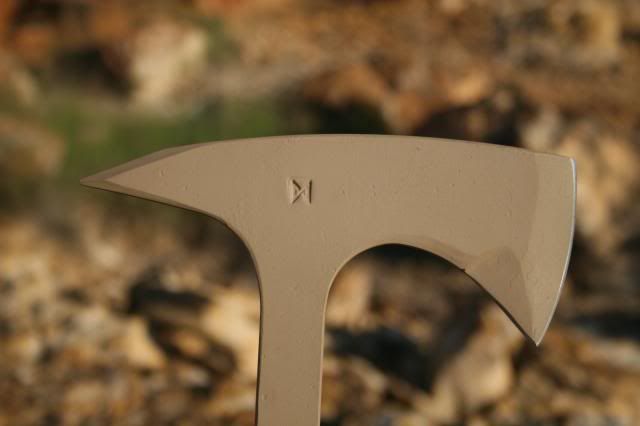
The pry spike is narrow enough to fit easily into a door jamb, while stout enough that it also penetrates the propane tank end without taking damage. Once the spike is nicely seated, the rounded top acts like a roller head pry bar, providing plenty of leverage.
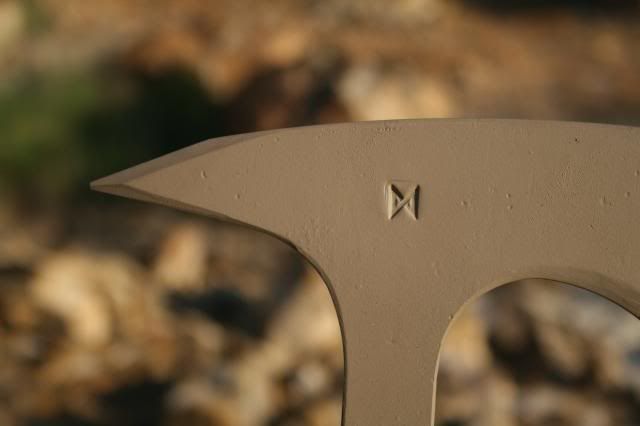
The short one (olive drab) sold at the Blade Show, and this was the only picture I managed to get.
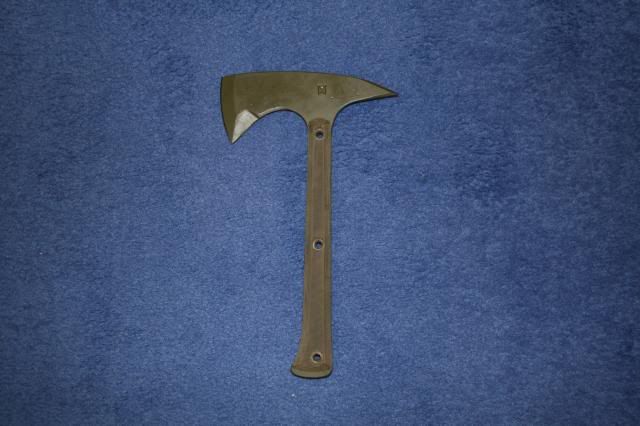
The handles have exposed pommels, allowing for some hammering ability with all designs and an extra striking area for CQB.
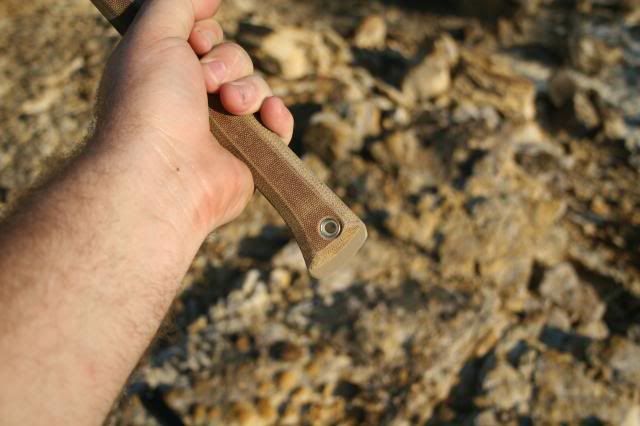
One advantage of shifting over to waterjetting is that I can build trainers fairly easily. These are cut from 3/4" ABS plastic and are the same pattern as the hammer polls, but with the corners rounded for safety. They are the same thickness as the handles of the real tomahawks and are beveled all over the same as the handles.
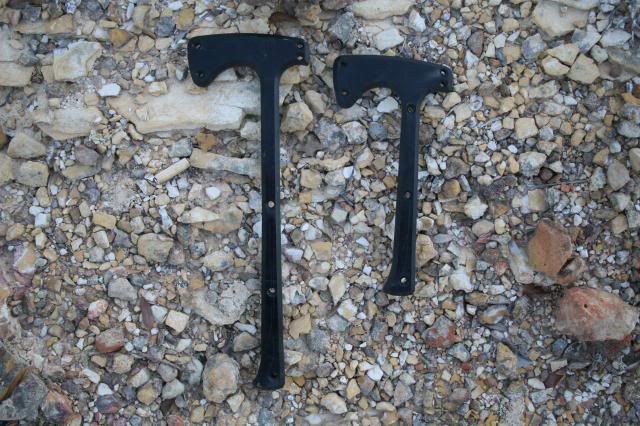
The extra holes allow you to slip a piece of foam pipe insulation or pool noodle over the ends and anchor them so you don't damage your sparring partner as much. The hammer polls are a bit shorter than the spikes, but are still long enough to practice hooking and deflecting limbs. The holes in the trainer handles allow practice with a lanyard.
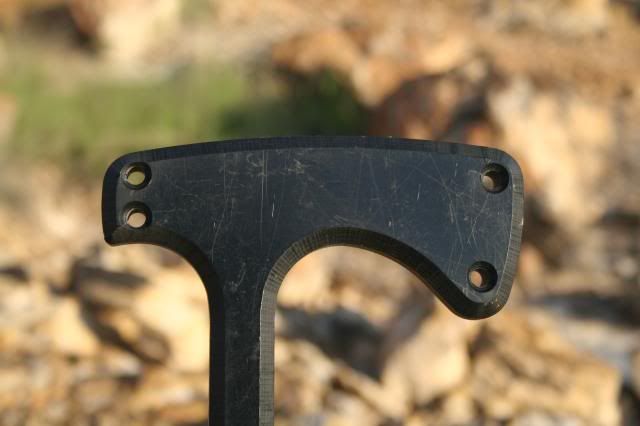
Sheaths are forthcoming, but should be Kydex, bottom eject, jump-ready, ambidextrous, MOLLE compatible, with multiple carry options.
These have been a long time coming, and I'm quite pleased to be able to finally have them on the table, ready to serve.